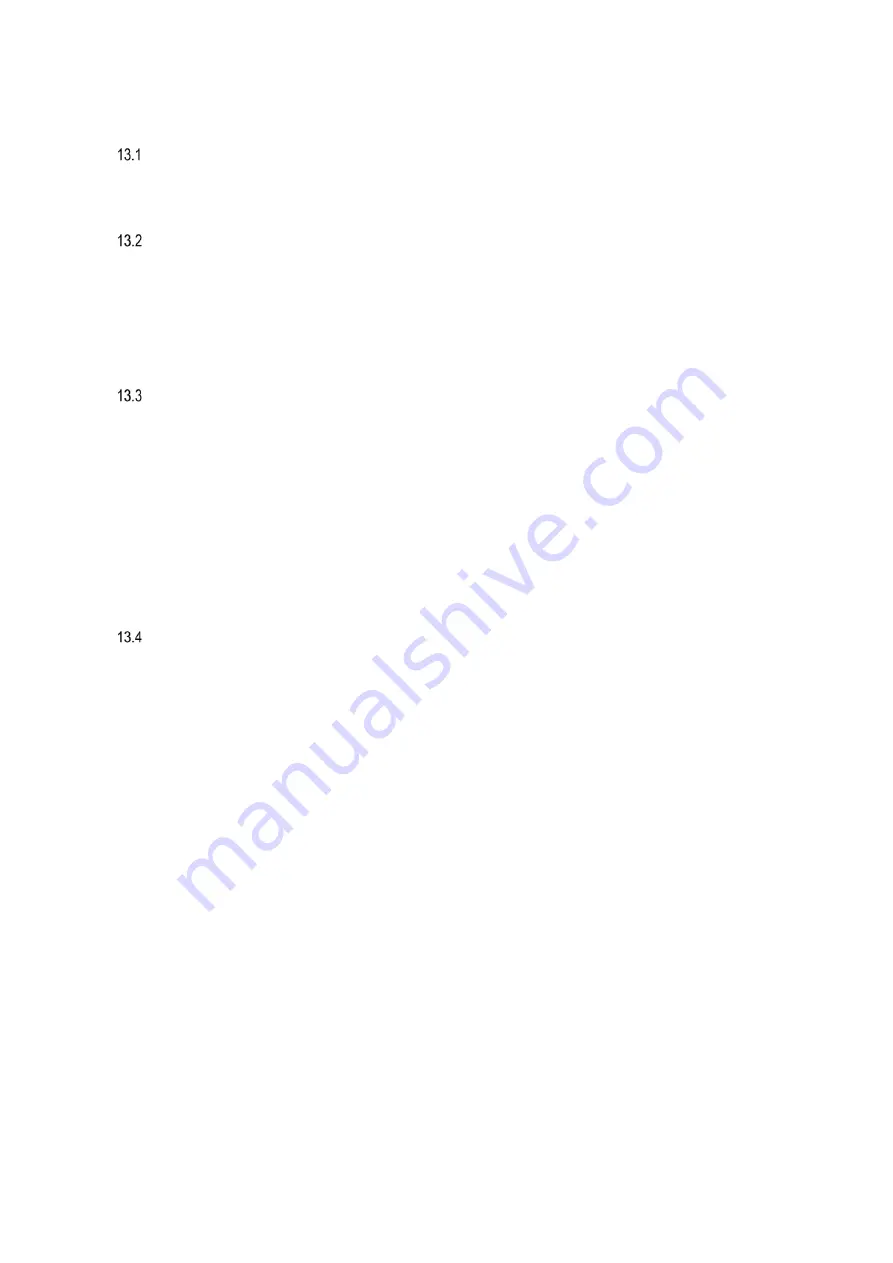
24
13.0
FAULT FINDING
HEAT EXCHANGER PLATE PACK ASSEMBLY
1.
Nuts and fittings are tight to turn - insufficient oil on threads.
2.
Plates move out of alignment: remove plates & degrease, then dry, inspect plate hanging system for damage.
EXCESSIVE PRESSURE DROPS
1.
Liquid flows higher than design: Check & adjust.
2.
Plate channels blocked: Back flush, Power flush or dismantle to clean.
3.
Inaccurate measurement: Check pressure gauge for accuracy.
4.
Ensure measurement does not include any bend, valve / fitting, & pipe run losses.
5.
Liquid temp. below design: Viscous media generate higher resistance to flow at lower temperatures.
6.
Media used not as per design: The addition of glycol or other additives can increase the pressure drop.
LEAKAGE
1.
leakage near connection: First heat transfer plate gasket damaged
–
dismantle heat exchanger plate pack, and check condition.
If the threaded connections are rotated when in situ, damage can occur to the backing O-rings. Refer to connection tightening
section of the manual.
2.
Flange gaskets leaking
–
check / replace.
3.
Crack in weld at joint
–
Dye Pen. Check and repair (remove plates out of heat exchanger before welding).
4.
Cross contamination: Check all plates for cracks and / or holes.
5.
Leakage from plate pack: Check tightening dimension Check condition of the gaskets. Check that all gaskets are seated
correctly.
6.
For nearly all leakage problems, it will be required to dismantle the plate pack before any attempts to rectify the fault can be
made. Mark the area(s) from where the leaks are occurring before taking apart the exchanger to assist in fault finding once
plates are taken out of exchanger.
DECREASE IN THE PERFORMANCE
1.
Plate surfaces require cleaning or de-scaling.
2.
Pumps or associated controls have failed.
3.
Liquid flows not as per the design specification - as shown in technical table.
4.
Associated boiler under sized.
5.
Primary temperature lower than design figures.
6.
Sensors faulty.
7.
Plate pack has not been assembled correctly.
8.
Unit running in co-current flow, instead of counter current - check with contract drawing and alter pipe work if necessary., and
check direction of pump flows.
9.
Air lock has developed in the plate pack
10.
Summary of Contents for LOKE8-100
Page 2: ...2 BLANK PAGE...
Page 16: ...16 Schematic LOKE instantaneous installation...
Page 17: ...17 Schematic LOKE with storage vessel schematic...
Page 23: ...23 12 7 1 EXAMPLES OF GASKET AND PLATE TYPES...
Page 25: ...25 14 0 DECLARATION OF CONFORMITY NOTES...
Page 26: ...26...
Page 27: ...27...
Page 28: ...28...