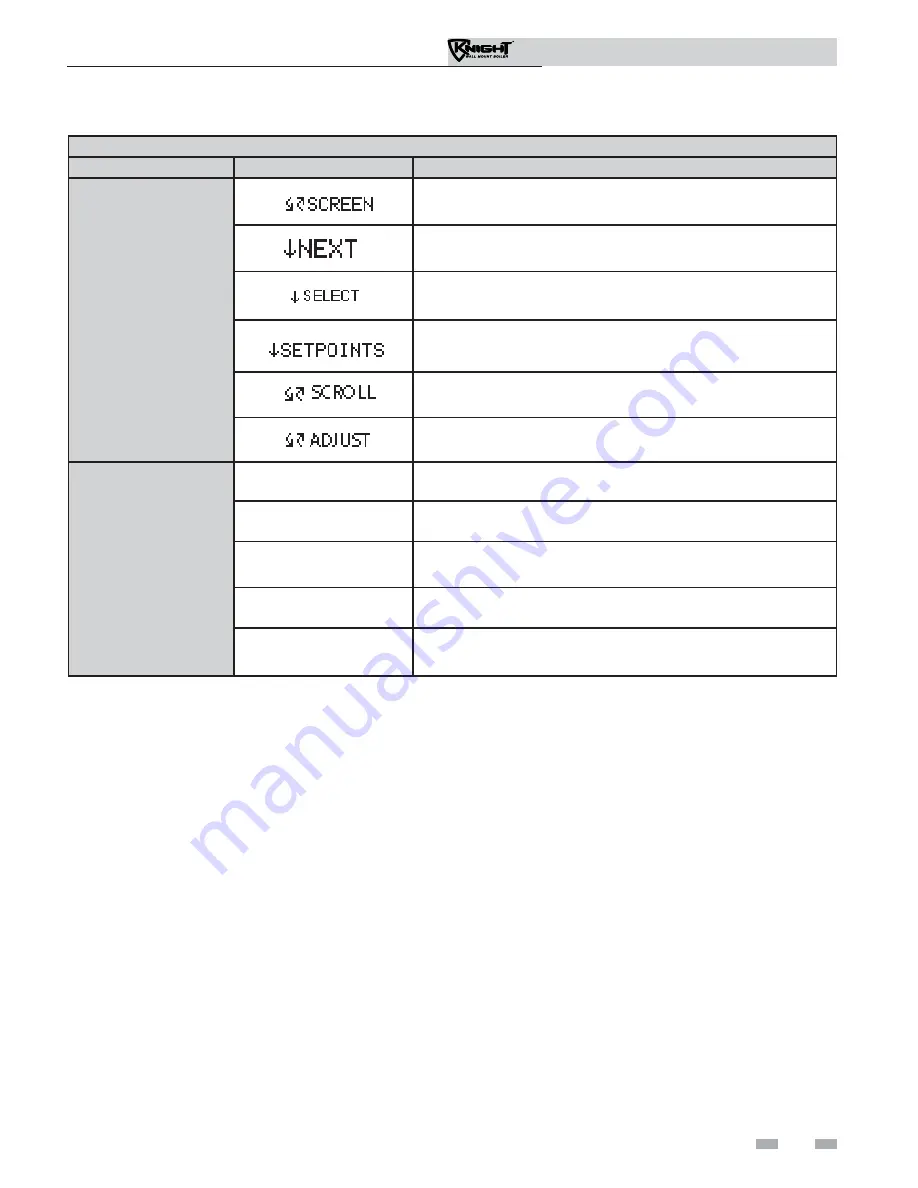
Installation & Operation Manual
73
11
Operating information
(continued)
Status Display Screens
(cont’d)
Section
Display
Description
E
(NAVIGATION
dial function)
Turning the NAVIGATION dial will select the next or previous Status
Screen.
Pressing the NAVIGATION dial will show the next fault, NSB (Night
Setback) trigger, or ramp delay setting.
Pressing the NAVIGATION dial will select the setting indicated by
the cursor.
Pressing the NAVIGATION dial will display the Set Points Screen.
Turning the NAVIGATION dial will move the cursor up or down.
Turning the NAVIGATION dial will increase or decrease the current
setting.
F
(RIGHT SELECT
key function)
SHDN
Press the RIGHT SELECT key to turn the boiler OFF.
ON
Press the RIGHT SELECT key to turn the boiler ON.
NO
Press the RIGHT SELECT key to cancel the shutdown operation.
SAVE
Press the RIGHT SELECT key to save the current change.
HOME
Press the RIGHT SELECT key to return to the Status Screen and
upload parameter changes.