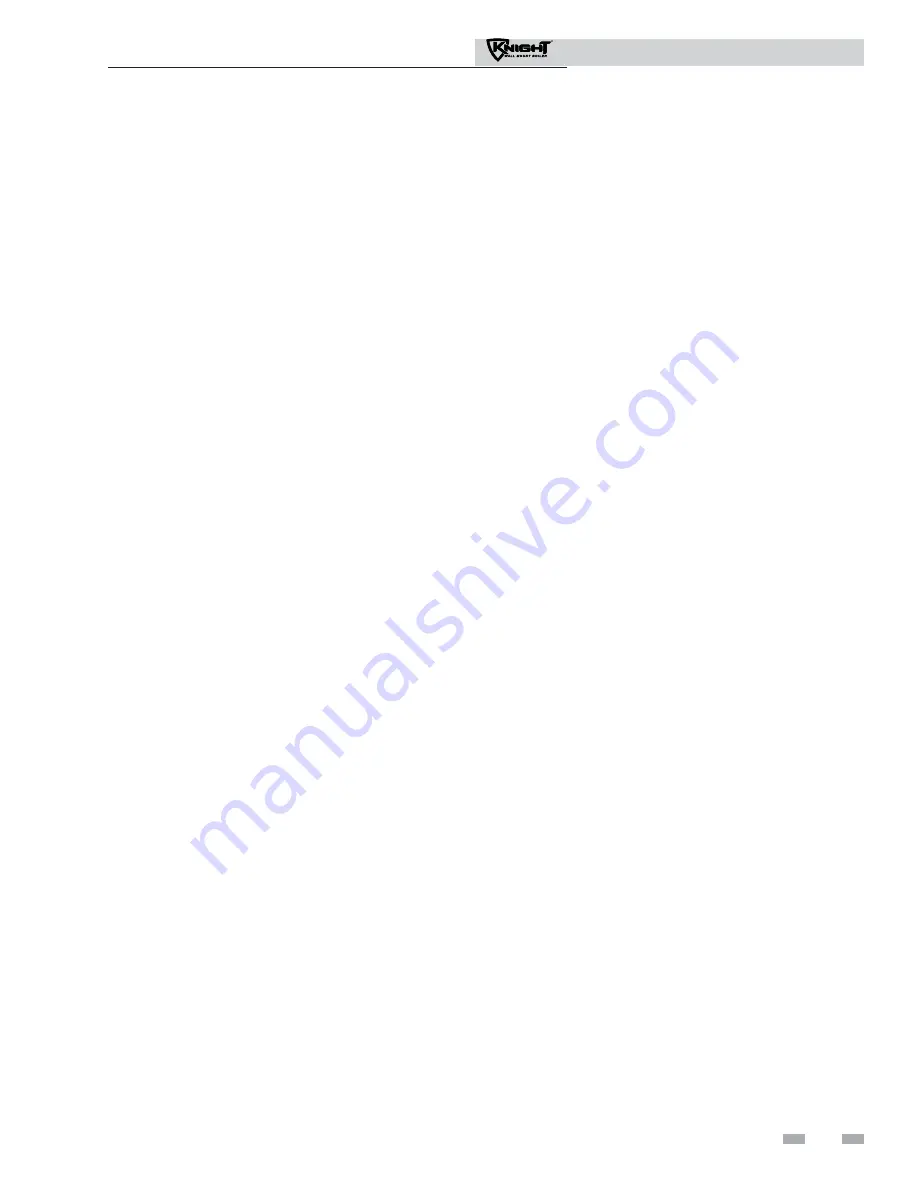
Service Manual
5
What is in this manual?
Service
Near boiler piping
• Typical system components
The Knight wall mount boiler display
• Display panel readout, buttons and their functions
Control module inputs
• Control module inputs and options
Control module outputs
• Control module outputs and options
General
• How the boiler operates
• How the control module operates
• Access modes -- user and installer
• Sequence of operation -- Domestic Hot Water
(DHW)/space heating
Control panel menu access
• Accessing programming mode and locating menus
(See separate guide covering the PC interface.)
Control panel parameter access
• Accessing and changing parameters from the display panel
Quick start information -- parameter
table
• An index of available adjustments and readouts, where to
access them and where to find detailed information.
Knight wall mount boiler operation
• A: General
• B: Temperature Setting
• C: Data Logging
• D: Functions
• E: DHW Settings
• F: Outdoor Reset
• G: Anti-cycling
• H: Control Modes
• I: Circulation Pumps
• J: Building Management System (BMS)
• K: Service Notification
Maintenance
• Service and maintenance schedules
• Address reported problems
• Inspect boiler area and boiler interior
• Clean condensate trap
• Check all piping for leaks
• Check air openings
• Flue vent system and air piping
• Check water system
• Check expansion tank
• Check boiler relief valve
• Inspect ignition electrode
• Check ignition ground wiring
• Check all boiler wiring
• Check control settings
• Perform start-up and checks
• Check burner flame
• Check flame signal
• Check flue gas temperature
• General maintenance
• Review with owner
• Cleaning boiler heat exchanger
• Oiled bearing circulators
Troubleshooting
• Troubleshooting table - No display
• Checking temperature sensors
• Sensor tables
• Troubleshooting table - Fault messages displayed on
boiler interface
• Combustion analysis procedure
• Gas valve adjustment procedure
Summary of Contents for Knight 151 - 211
Page 46: ...46 NOTES...
Page 47: ...47 NOTES...