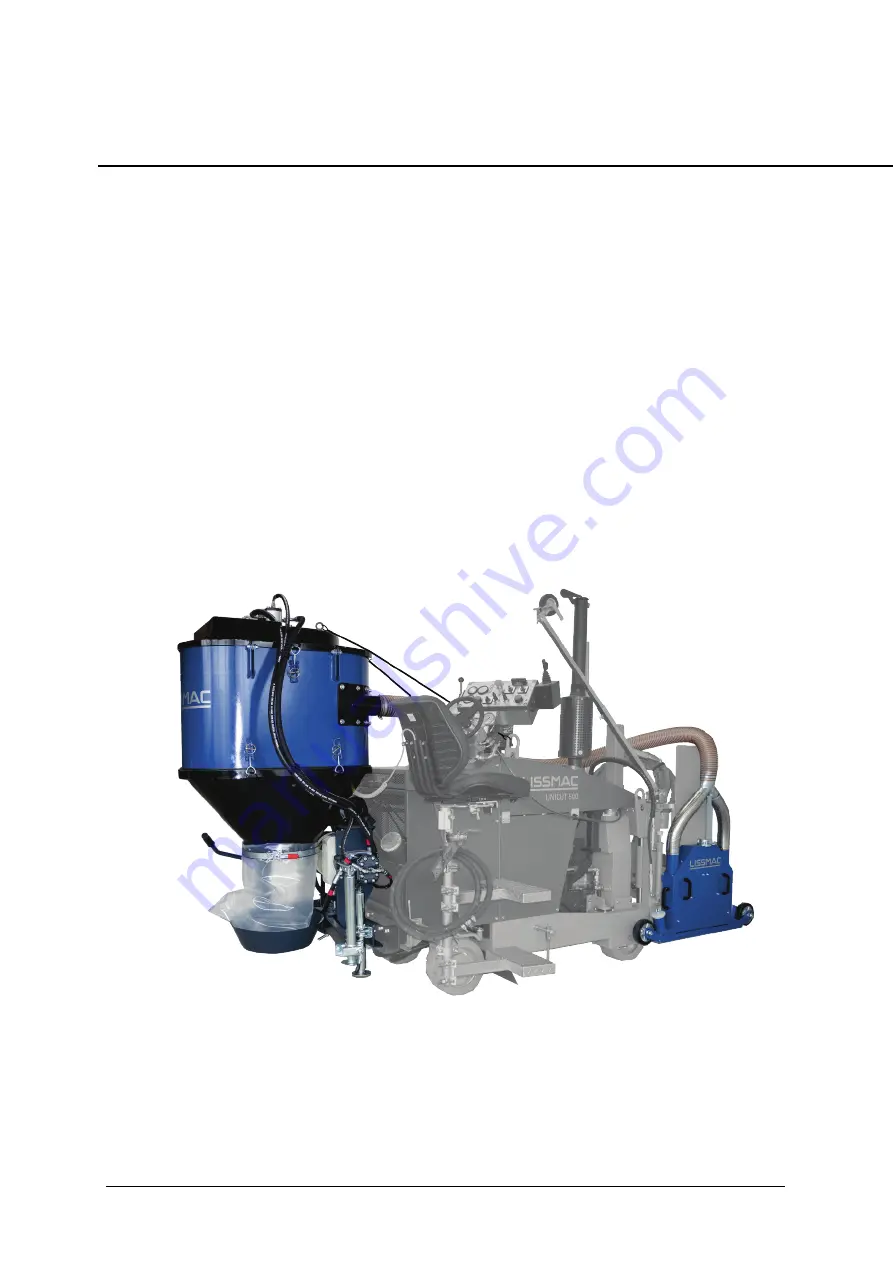
8/30
1.
1. FEARURES & BENEFITS
VACUUM DRY dry extraction removes the sawdust and the sawing particles quickly and easily from the
joint already during the sawing works. The saw blade must thus not machine any additional material.
The machine works more effectively thereby. The extraction has additionally a positive effect and cools
the saw blade additionally.
•
The Quick and simple attachment to the joint cutter UNICUT 500: Closed system, which is attached directly
to the joint cutter and is driven via a hydraulic interface at the machine
•
Can be converted or upgraded quickly and easily with corresponding accessories such as a special saw blade
protection hood and a flange cooling for dry cut
•
Simple emptying of the sawdust and particles by swinging out as well as the exchange of the filter bags
•
The extraction cleans the filters automatically during extraction
•
The clean, dry joint can be processed immediately (grouting)
Fig. VACUUM WET 500 with the joint cutter UNICUT 500