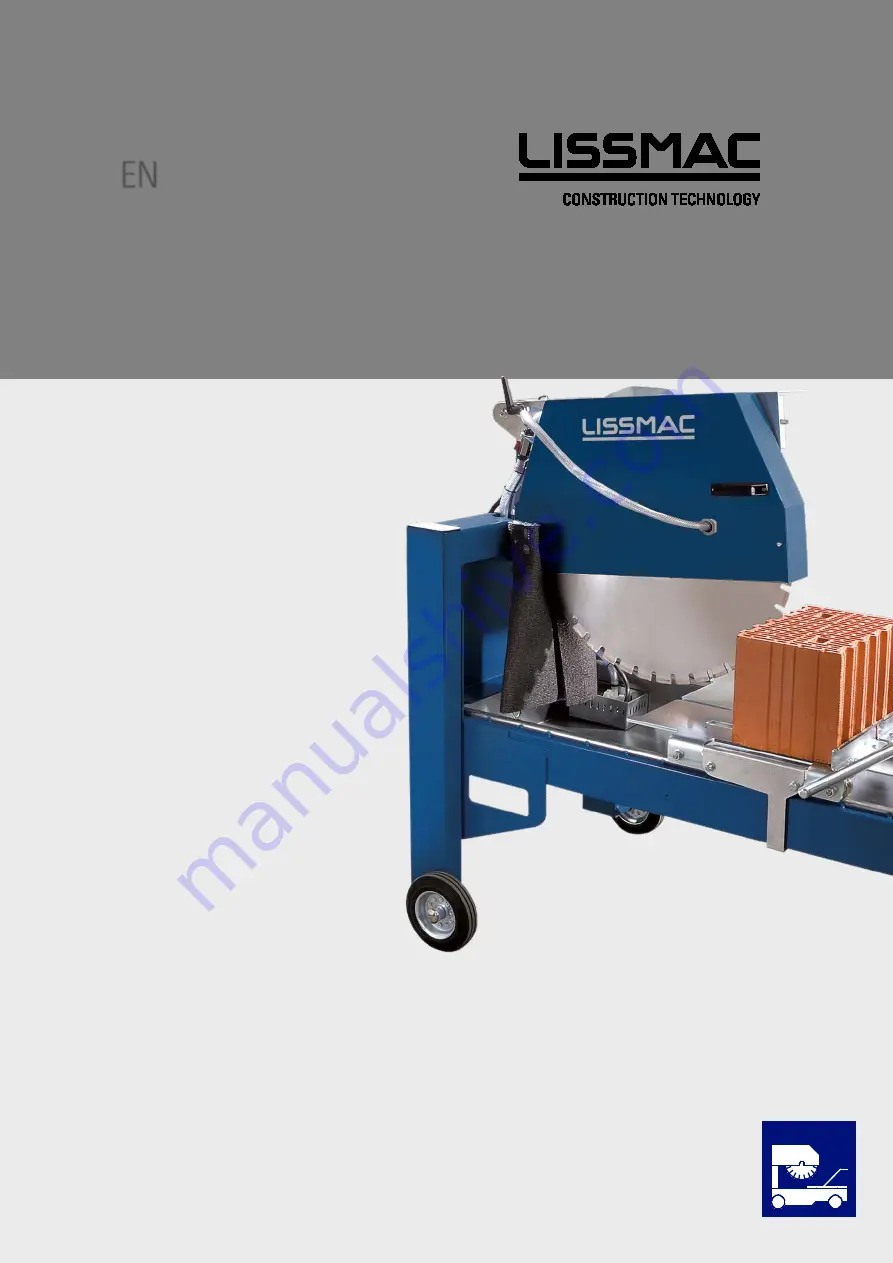
1/40
OPERATING MANUAL
MASONRY SAW DTS
DTS 700
LISSMAC Maschinenbau GmbH
Lanzstrasse 4
D-88410 Bad Wurzach
Tel49 (0) 7564 / 307- 0
Fax +49 (0) 7564 / 307 - 500
[email protected]
www.lissmac.com
EN
Summary of Contents for DTS 700
Page 2: ...2 40...
Page 6: ...6 40 Notes...
Page 32: ...32 40 10 SPARE PARTS LIST...
Page 33: ...33 40...
Page 34: ...34 40...
Page 39: ...39 40...
Page 40: ...40 40...