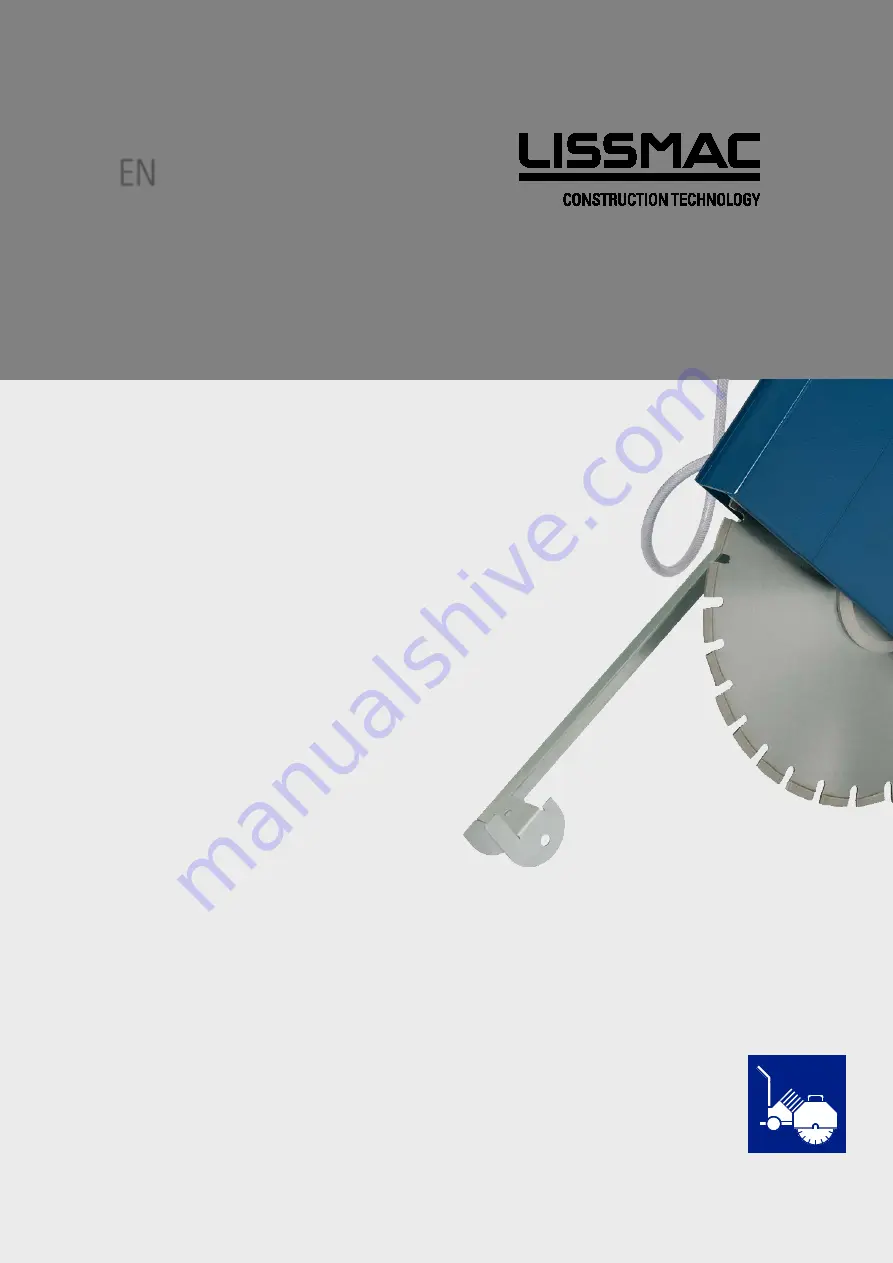
1/72
OPERATING MANUAL
FLOOR SAW
COMPACTCUT 201 P
LISSMAC Maschinenbau GmbH
Lanzstrasse 4
D-88410 Bad Wurzach
Tel49 (0) 7564 / 307 - 0
Fax +49 (0) 7564 / 307 - 500
[email protected]
www.lissmac.com
EN
Summary of Contents for COMPACTCUT 201 P
Page 2: ...2 72 ...
Page 45: ...45 72 10 SPARE PARTS ...
Page 46: ...46 72 Abb 0 ...
Page 47: ...47 72 Abb 01 ...
Page 48: ...48 72 Abb 01 1 ...
Page 50: ...50 72 Abb 01 2 ...
Page 52: ...52 72 Abb 01 3 ...
Page 54: ...54 72 Abb 02 ...
Page 56: ...56 72 Abb 03 ...
Page 57: ...57 72 Abb 03 1 ...
Page 59: ...59 72 Abb 03 2 ...
Page 61: ...61 72 Abb 03 3 ...
Page 63: ...63 72 Abb 03 4 ...
Page 65: ...65 72 Abb 03 5 Abb 03 6 ...
Page 67: ...67 72 Abb 03 4 ...
Page 69: ...69 72 Abb 05 Abb 06 ...
Page 72: ...72 72 ...