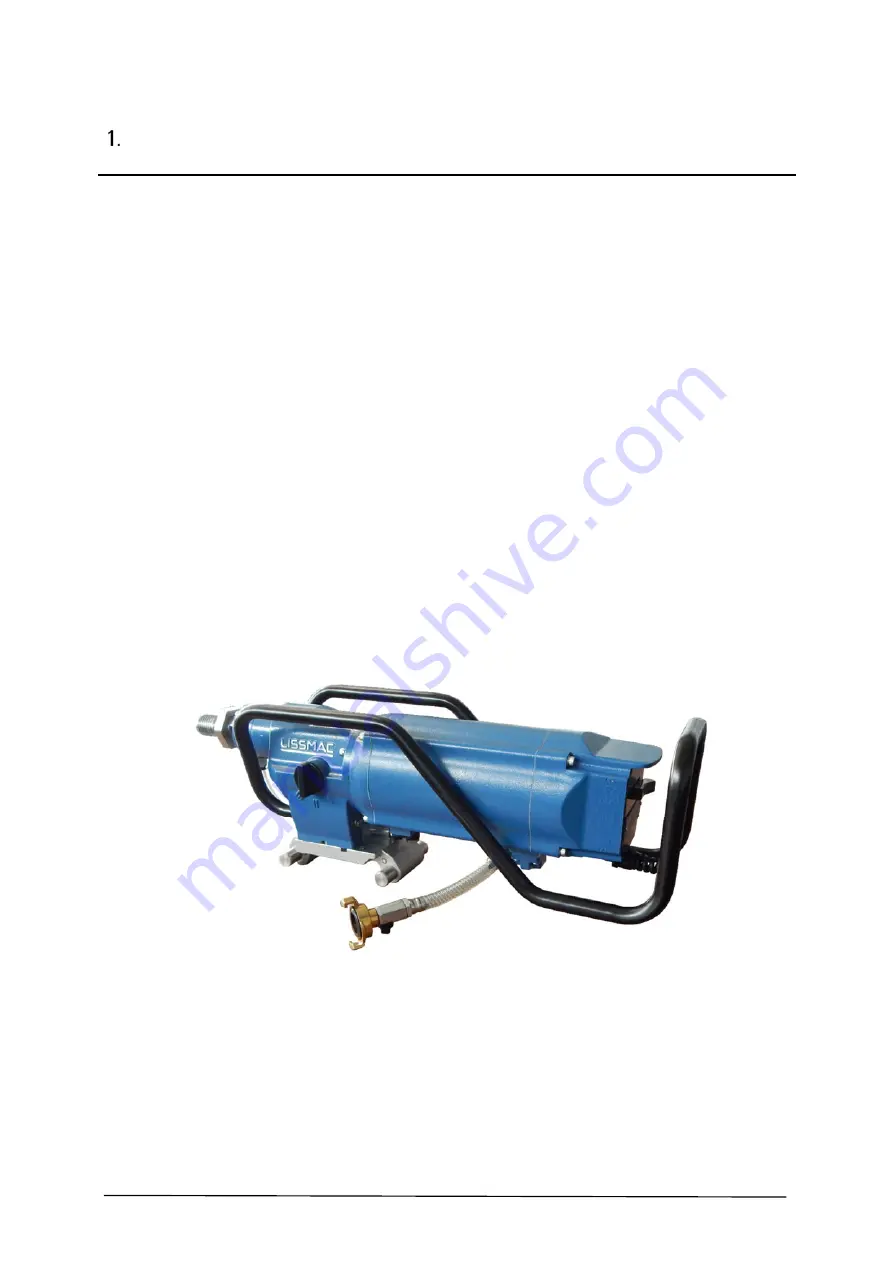
7/30
DESCRIPTION OF PERFORMANCE
With their compact, robust design, the CDM 46 W and CDM 63 W provide reliable, user-friendly,
professional wet drilling every day on the construction site. The closed core drill motor (water
cooled) enables easy overhead drilling without any sealing measures. The careful design of the
safety clip secures the core drill in the harsh construction site environment as well as acting as a
functional handle for daily transport and simple mounting on drilling stands.
User-friendly - Three gear levels permit optimum speed selection adapted to the specific core
drill diameter
Drill crown collet with integrated spindle protection
Electro-mechanical on/off switch on the control box is quick and easy to operate even in
difficult situations
MULTI-TRONIC
The integrated, automatic phase inverter spares controlling the direction of rotation of the
drill spindle – it automatically regulates the direction of rotation
Overload protection for the maximum possible operating comfort and long service life -
Stotter Elektronik
Integrated smooth start makes operation easier when starting the drilling process
Maximum safety due to electronic and mechanical overload coupling as well as additional
thermal overload protection
Summary of Contents for CDM 46 W
Page 2: ...2 30...
Page 6: ...6 30 Notes...
Page 28: ...28 30 CDM 20 U CDM 20 W 230V YELLOW GREEN BLUE 2 1 3 4 GREEN YELLOW RED 19 05 2015 46 63 W 400...
Page 30: ...30 30...