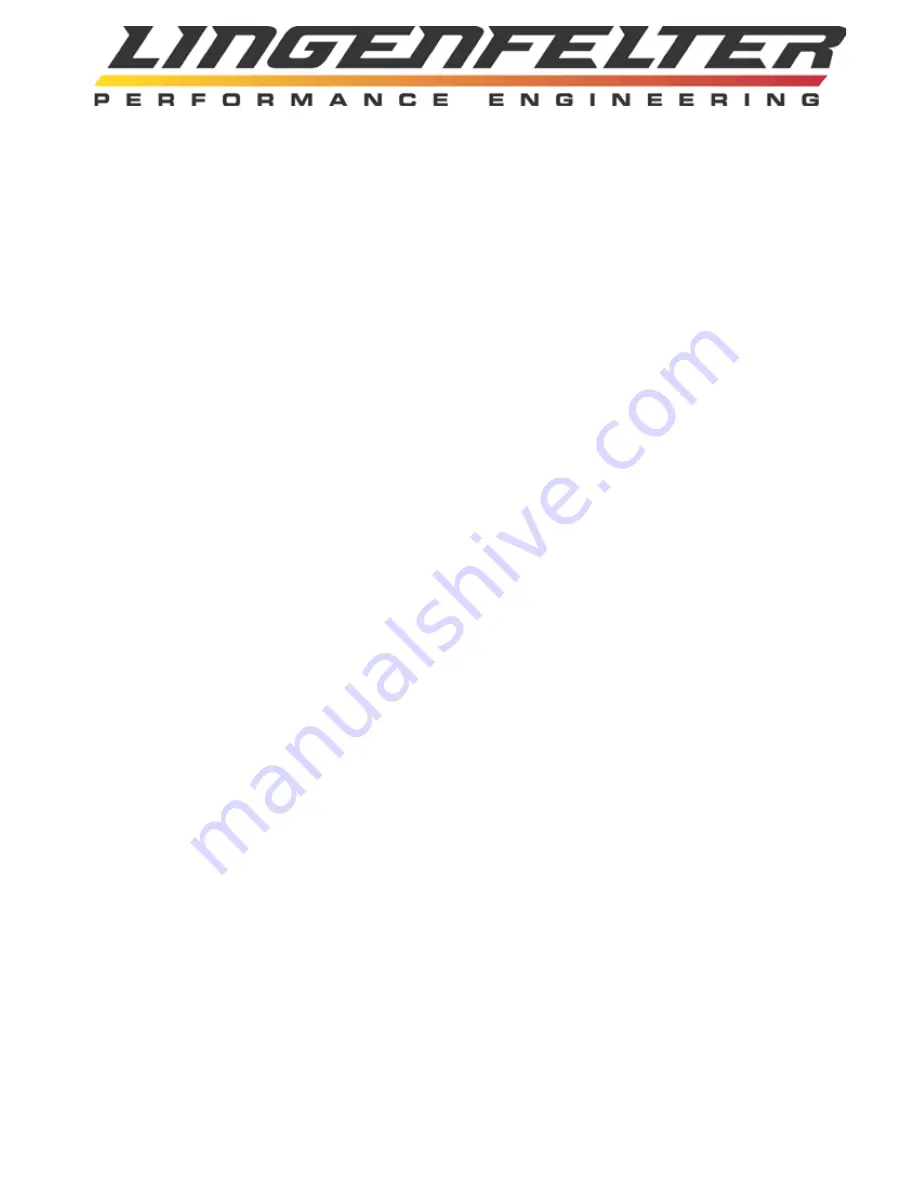
Page
7
3. With the vehicle keyed on, the engine off, and the clutch or accelerator pedal fully released, press the green
programming button on the back of the RPM-003. The LED should now be blinking RED+GREEN. The RPM-003 will
now take the current closed throttle voltage or released clutch voltage, depending on which sensor you connected the
RPM-003’s purple analog input wire to.
4. Fully depress and then fully release the pedal that the RPM-003 is connected to (throttle or clutch) two times. The
RPM-003 will find the average of the two depressed voltages and then compare the average to the released voltage
to determine whether the calibration is valid. If the LED turns solid RED, the calibration was successful and is
programmed into memory. If the LED begins to blink RED, the calibration was unsuccessful for one of the following
reasons:
•
The range between the closed throttle/released clutch signal and the wide open throttle (WOT)/depressed clutch
voltages must be at least 1.5 volts.
• The difference between the first WOT/depressed voltage and the second WOT/depressed voltage must be less than
or equal to 0.1 volts.
5. If an error occurs, simply power down the RPM-003 and re-program the pedal position voltages.
Example settings:
GM LS1/LS6/LS2 V8 engines with tachometer signal from ECM/PCM (1997-2013 Corvette, 1998-2002 Camaro/
Firebird, 1999-2006 C/K truck, 2004-2006 GTO):
•
Connect white Tachometer Input Signal wire to ECM/PCM tachometer output -- see page 15 for tachometer signal wire
information.
• (
1800 RPM) RPM switch mode example with no hysteresis, analog input, or pull-up resistor:
o
Sixteen position Input Signal Pulse Per Revolution switch set to Low Range and 2 pulses per revolution
o
RPM #1 programming switch for thousands of RPM (X000) on position 1
o
RPM #1 programming switch for hundreds of RPM (0X00) on position 8
○
Both RPM #2 programming switches on position 0
○
DIP switches 1-5 flipped down (all DIP switches in OFF position)
•
NOTE - if this is a custom vehicle application using one of these ECM/PCM's and nothing is connected to the
tachometer signal or your aftermarket tachometer does not have a pull-up resistor then you will need to enable
the pull-up resistor using DIP switch # 5
•
(1800 RPM - 6000 RPM) Window switch mode example with no hysteresis, analog input, or pull-up resistor
o
Sixteen position Input Signal Pulse Per Revolution switch set to Low Range and 2 pulses per revolution
o
RPM #1 programming switch for thousands of RPM (X000) on position 1
o
RPM #1 programming switch for hundreds of RPM (0X00) on position 8
o
RPM #2 programming switch for thousands of RPM (X000) on position 6
o
RPM #2 programming switch for hundreds of RPM (0X00) on position 0
○
DIP switches 1-5 flipped down (all DIP switches in OFF position)
•
NOTE - if this is a custom vehicle application using one of these ECM/PCM's and nothing is connected to the
tachometer signal or your aftermarket tachometer does not have a pull-up resistor then you will need to enable
the pull-up resistor using DIP switch # 5