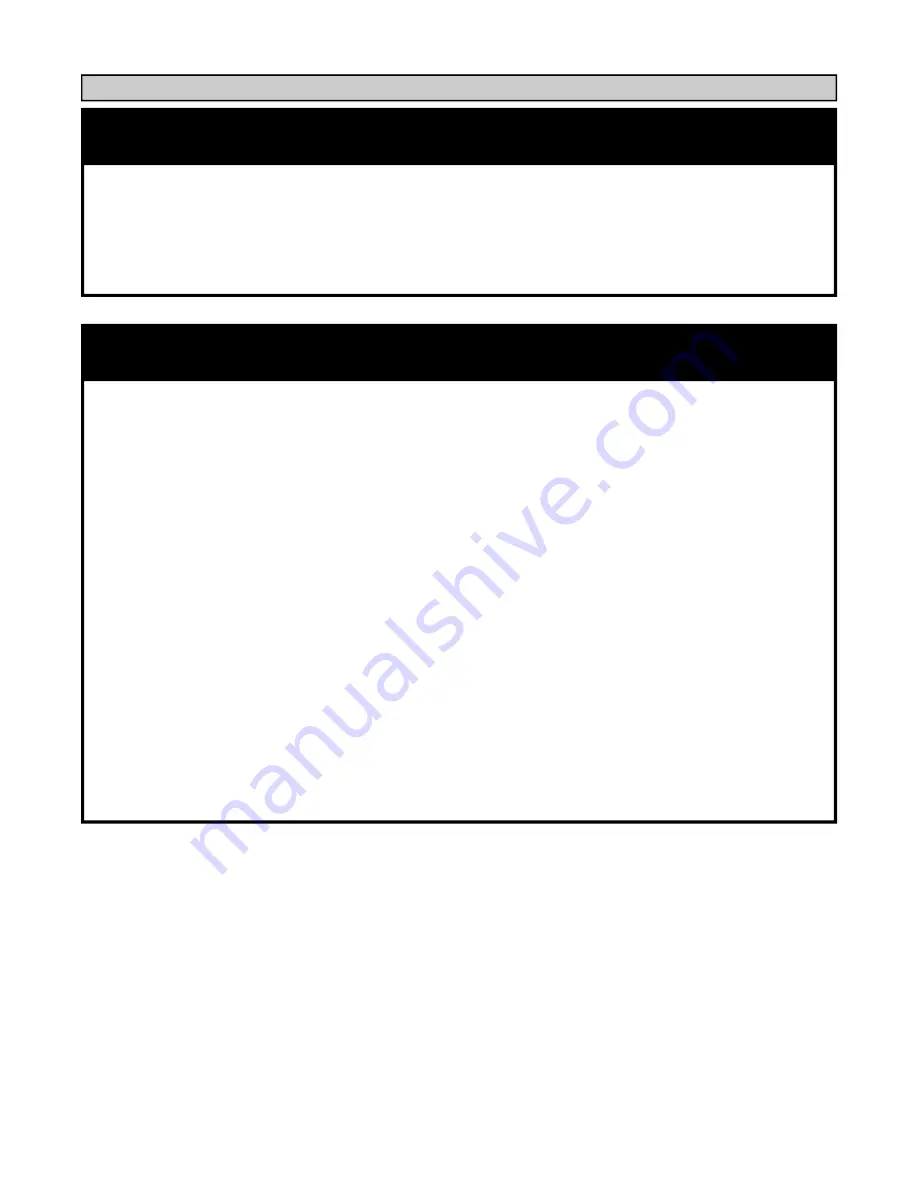
BIASI B/40
PAGE 24
Check for fouling or soot buildup in the combustion chamber at least every twelve (12)
months.
Caution: Black carbon soot in the combustion chamber can, under certain conditions, be
ignited by a spark or open flame. To prevent this unlikely occurrence, dampen the soot deposits with a
wet brush or a fine water spray before servicing or cleaning the combustion chamber. Fouling or
carbon soot buildup on the surfaces in the combustion chamber is caused by incomplete combustion,
and is a sign of combustion air and/or venting problems. As soon as any fouling is observed, the cause
of the fouling should be corrected and the combustion chamber should be cleaned as follows:
Disconnect the electrical power supply to the boiler, burner and controls. Close Fire-O-Matic thermal
shutoff valve at burner prior to servicing. Remove the front jacket panel (#9) and the loosen the two
(2) front boiler door nuts. Swing the boiler door open. Be careful not to damage the door stud threads
or the flexible oil line. Brush and vacuum combustion chamber and flue passages until all deposits are
removed. Reassemble components in reverse order, making sure any damaged gaskets are repaired or
replaced.
Other maintenance requirements are as follows: Inspect wiring and controls for damage. Insure
controls are operating correctly. Inspect oil or gas supply lines for damage, corrosion or leaks. Repair
any leaks immediately. Inspect, clean or replace oil filter as specified by manufacturer. Inspect vent
and fill pipes for any obstruction, damage or corrosion. Clean or replace as necessary. Lubricate the
burner motor if necessary during service. Finally, consult burner manual for specific burner
maintenance instructions.
14. Commissioning:
After installation of oil/gas-fired boiler, operation and performance tests shall be conducted to
make certain that the burner is operating in an acceptable manner and that all safety controls and
devices function properly. It is critical that the high limit, low water
cutoff and burner "cad cell" relay be checked for normal operation before leaving the job. Refer to the
back page of this manual to write down the System Checkout information.
15. Maintenance:
Summary of Contents for 6-12 SECTION
Page 16: ...BIASI B 40 PAGE 16...
Page 22: ...BIASI B 40 PAGE 22 B 40 Control Panel Wiring Diagram for Riello Oil Burner...
Page 26: ...BIASI B 40 PAGE 26...
Page 27: ...PAGE 27 BIASI B 40...