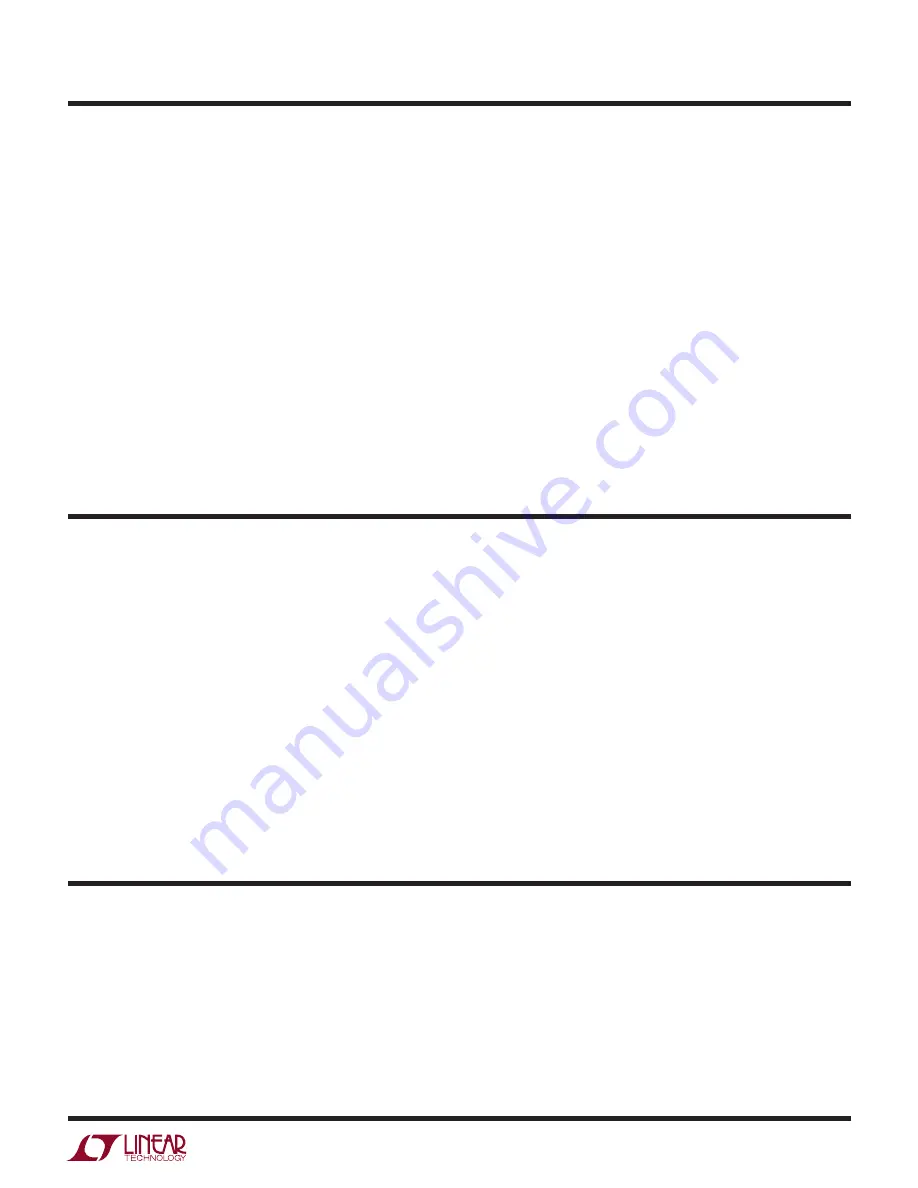
3
dc1805af
DEMO MANUAL DC1805A
Dc718 Quick start proceDure
Check to make sure that all switches and jumpers are
set as shown in the connection diagram of Figure 1. The
default connections configure the ADC to use the onboard
reference and regulators to generate the required common
mode voltages. The analog input is DC coupled. Connect
the DC1805A to a DC718 USB high speed data collection
board using connector J4. Then, connect the DC718 to a
host PC with a standard USB A/B cable. Apply 9V to the
indicated terminals. Then apply a low jitter signal source
to J3. Connect a low jitter 100MHz 3.3V
P-P
sine wave or
square wave to connector J1. Note that J1 has a 50Ω
termination resistor to ground.
Run the QuikEval-II software (Pscope.exe version K72
or later) supplied with the DC718 or download it from
www.linear.com
.
Complete software documentation is available from the
Help menu. Updates can be downloaded from the Tools
menu. Check for updates periodically as new features
may be added.
The PScope™ software should recognize the DC1805A
and configure itself automatically.
Click the Collect button (see Figure 4) to begin acquiring
data. The Collect button then changes to Pause, which
can be clicked to stop data acquisition.
Dc590B setup
IMPORTANT! To avoid damage to the DC1805A, make
sure that VCCIO (JP5) is set to 3.3V before connecting
the DC590B to the DC1805A.
Connect the DC590B to a host PC with a standard USB
A/B cable. Connect the DC1805A to a DC590B USB serial
controller using the supplied 14-conductor ribbon cable.
Run the evaluation software supplied with the DC590B or
download it from
www.linear.com
.
The correct control panel will be loaded automatically. Click
the Collect button to begin reading the ADC.
This board is tested by measuring the distortion at the
differential output given a –1dBFS, 2kHz single-ended
input as shown in Figure 2.
For SINAD, THD or SNR testing a low noise, low distor-
tion generator such as Audio Precision SYS-2722, B&K
Type 1051 or Stanford Research DS360 should be used.
A low jitter RF oscillator such as the Marconi Instruments,
Multisource Generator 2026 should be used as the clock
source.
To test the boards please follow the steps below:
1) Make sure that all the jumpers are set as shown in
Figure 2 (DC1805A Test Diagram).
2) Power up the board by applying 9VDC.
3) Apply the clock signal to connector J1. Clock frequency
99.2MHz (to achieve 1.6Msps conversion rate, please
refer to the Clock Source section for more detailed
information), V
IN
3.3V
P-P
.
4) A single pole lowpass filter should be used for best
SNR measurement data. One option is to create an on-
board RC low pass filter by populating R5 with 200Ω
and C33 with 0.22µF. It is very important to use a very
low distortion capacitor. In order to balance both inputs
of the LTC6362 populate R12 with a 200Ω resistor in
parallel with a 0.22µF capacitor.
5) Apply a 2kHz, –1dBFS signal to connector J3.
The performance that results from these connections are
displayed in Figure 4.
Quick start proceDure