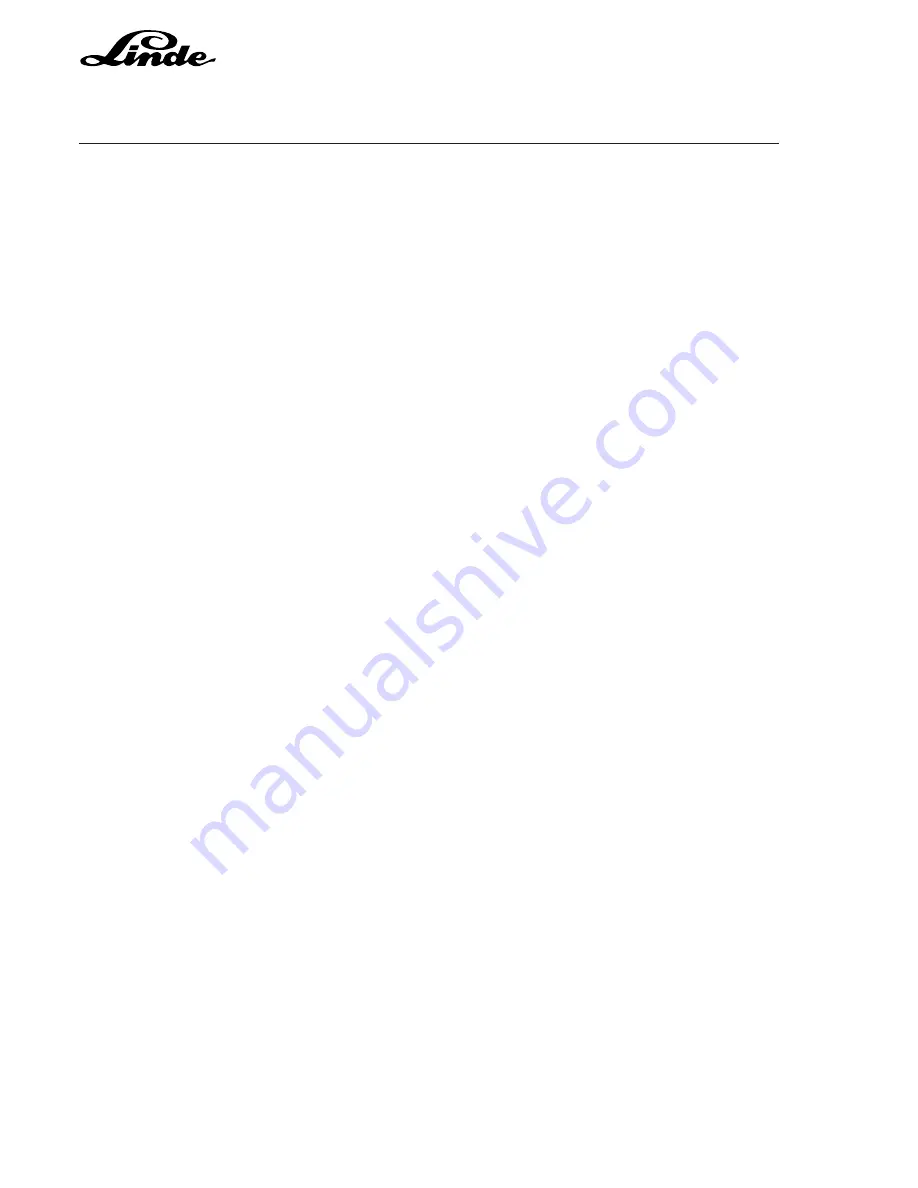
Service Training
Section
4.9
Page
54
12.05
ADJUSTING THE CO CONTENT
Prerequisites for adjustment:
- Firing point checked and if necessary corrected: desired value 18 ± 2 ° before TDC
(from 01/2005: 8 ± 2 ° before TDC).
- With truck warmed up, hydraulic oil at 60 – 70 °C, operating hydraulics pressure relief valve set to 265
bar.
- Parking brake locked in braked position.
Adjustment:
- Turn idling mixture adjustment screw (3) to its limit stop and then unscrew by three turns.
- Connect CO meter.
- Start engine and when truck is warmed up at a low idling speed (750 – 800 rpm) determine CO value.
Target value:
CO
≤
0.1 % by volume
If CO > 0.1 % by volume, unscrew screw (3) more, engine must be running in idling mode
but clearly regularly.
- Place full-load mixture adjustment screw (2) in the middle between L and R (the screw is located at the
gas intake in the mixer).
- Connect CO meter.
- With the footbrake on, bring the engine to maximum running speed, activate tilt control lever fully to the
limit stop and hold there, at the same time turn the steering to the limit stop too, and hold, thereby applying
a load to the engine.
- Determine CO value of the engine under this load.
Target value:
CO
≤
0.1 % by volume
Correction:
To reduce CO value
= turn adjustment screw in direction L.
To increase CO value
= turn adjustment screw in direction R.
(to enhance engine performance)
NOTE:
The engine cannot be set to this setting with a running speed lower than 1750 rpm.
In models with catalysers, the speed cannot go below 1850 rpm.
- Screw in limit stop screw (9) against limit stop (8) to the point that when pressing the magnet axis up to
the limit stop, the running speed is kept at about 500 rpm.
Summary of Contents for H 50 D
Page 2: ......
Page 8: ...Service Training 12 05 ...
Page 58: ...Page 50 Section 4 1 Service Training 09 06 ...
Page 59: ...Service Training Page 4 2 Section 1 4 2 TRANSMISSION ...
Page 67: ...Seite 9 Abschnitt 4 2 Service Training HYDRAULIKSCHALTPLAN H 50 60 70 80 TYP 353 ...
Page 70: ......
Page 71: ...Service Training Page 4 2 Section 13 05 00 ...
Page 76: ...Section 4 2 Page 18 Service Training 09 04 ...
Page 77: ...Service Training Page 4 2 Section 19 09 04 ...
Page 80: ...Service Training Page 4 2 Section 22 09 04 ...
Page 87: ...Service Training Page 4 2 Section 29 09 04 ...
Page 107: ...Service Training Page 4 2 Section 49 09 04 ...
Page 141: ...Service Training Section 4 3 Page 1 4 3 CHASSIS ...
Page 145: ...Service Training Section 4 4 Page 1 4 4 STEERING SYSTEM ...
Page 158: ...Service Training Section 4 4 Page 14 ...
Page 159: ...Service Training Page 1 Section 4 5 4 5 CONTROLS ...
Page 161: ...Service Training Page 3 Section 4 5 ...
Page 173: ...Service Training Page 1 Section 4 6 4 6 ELECTRICALSYSTEM ...
Page 175: ...Page 3 Section 4 6 Service Training CIRCUIT DIAGRAMM H 50 60 70 80 TYPE 353 ...
Page 176: ......
Page 177: ...Service Training Page 5 Section 4 6 05 00 ...
Page 180: ......
Page 183: ...Page 11 Section 4 6 Service Training 05 00 CIRCUIT DIAGRAMM H 50 60 70 80 02 TYPE 353 ...
Page 184: ......
Page 188: ......
Page 191: ...Page 19 Section 4 6 Service Training 09 04 CIRCUIT DIAGRAMM H 50 60 70 80 03 TYPE 353 DIESEL ...
Page 192: ...Section 4 6 Page 20 Service Training 09 04 ...
Page 199: ...Page 27 Section 4 6 Service Training 09 04 CIRCUIT DIAGRAMM H 50 60 70 80 03 TYPE 353 LPG ...
Page 200: ...Section 4 6 Page 28 Service Training 09 04 ...
Page 205: ...Service Training Page 33 Section 4 6 09 04 ...
Page 213: ...Service Training Section 4 7 Page 1 4 7 WORKING HYDRAULICS ...
Page 220: ...Service Training Section 4 7 Page 8 ...
Page 221: ...Service Training Page 1 Section 4 8 4 8 MAST ...
Page 226: ...Page 6 Section 4 8 Service Training ...
Page 239: ...Service Training Section 4 9 Page 13 12 05 ...
Page 254: ......
Page 255: ...Service Training Section 4 9 Page 29 12 05 ...
Page 258: ...Section 9 Page 32 Service Training ...
Page 276: ...Service Training Section 4 9 Page 50 12 05 ...
Page 281: ......