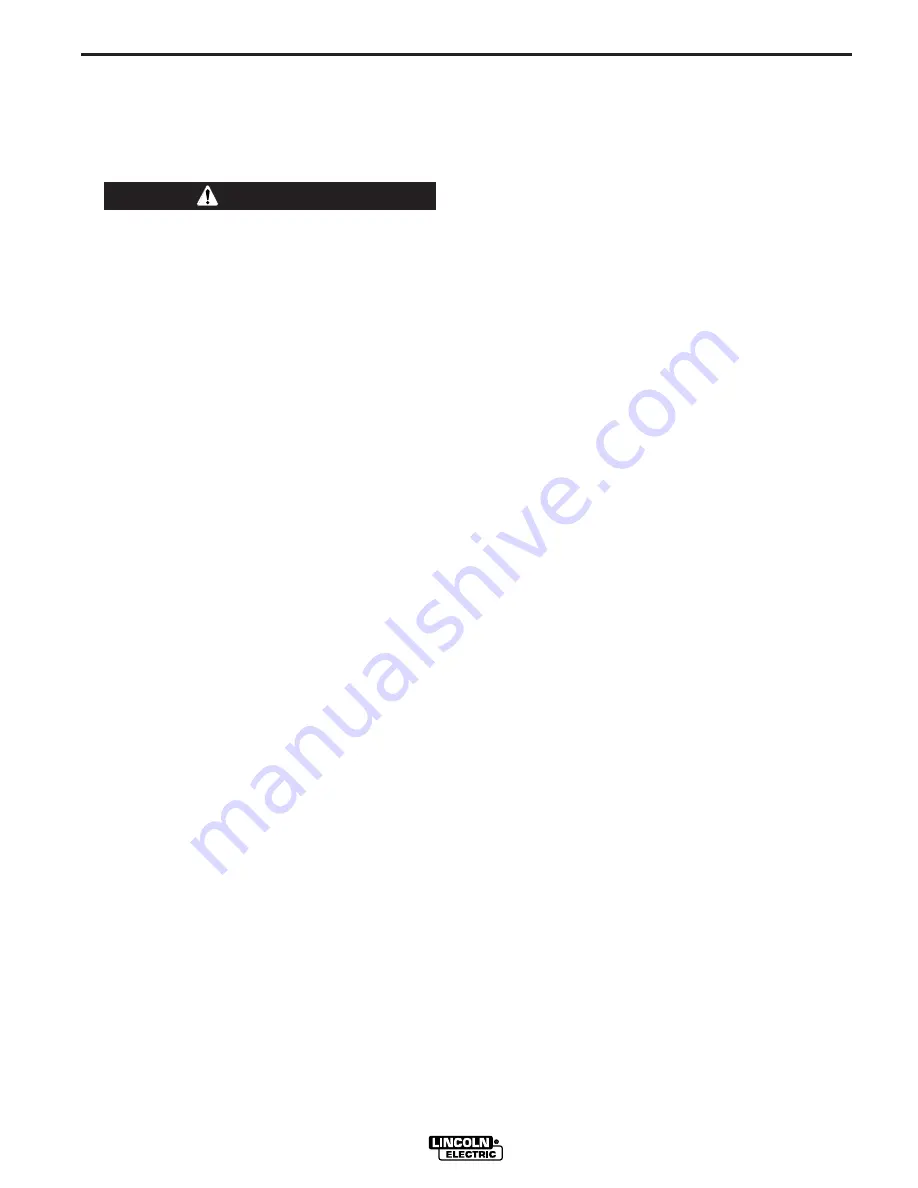
B-9
B-9
OPERATION
POWER MIG 300
4. Re-install the Retaining Collar. Make sure that the
Release Bar
“
pops up
”
and that the collar retainers
fully engage the retaining ring groove on the spin-
dle.
FEEDING WIRE ELECTRODE
When triggered, the electrode and drive mecha-
nism are electrically
“
hot
”
relative to work and
ground and remain
“
hot
”
several seconds after
the gun trigger is released.
------------------------------------------------------------------------
NOTE: Check that drive rolls, guide plates and gun
parts are proper for the wire size and type being used.
Refer to Table C.1 in ACCESSORIES section.
1. Turn the Readi-Reel or spool until the free end of
the electrode is accessible.
2. While securely holding the electrode, cut off the
bent end and straighten the first six inches. (If the
electrode is not properly straightened, it may not
feed properly through the wire drive system).
3. Release the pressure on the idle roll by swinging
the adjustable pressure arm down toward the back
of the machine. Lift the cast idle roll assembly and
allow it to sit in an upright position. Leave the outer
wire guide plate installed. Manually feed the wire
through the incoming guide bushing and through
the guide plates (over the drive roll groove). Push a
sufficient wire length to assure that the wire has fed
into the gun and cable assembly without restriction.
Reposition the adjustable pressure arm to its origi-
nal position to apply pressure to the wire.
4. Press gun trigger to feed the electrode wire through
the gun.
IDLE ROLL PRESSURE SETTING
The idle roll pressure adjustment knob is set at the
factory at the #2 hash mark. This is an approximate
setting. The optimum idle roll pressure varies with
type of wire, wire diameter, surface conditions, lubri-
cation, and hardness. As a general rule, hard wires
may require greater pressure, and soft, or aluminum
wire, may require less pressure than the factory set-
ting. The optimum idle roll setting can be determined
as follows:
1. Press end of gun against a solid object that is elec-
trically isolated from the welder output and press
the gun trigger for several seconds.
2. If the wire
“
birdnests
”
, jams or breaks at the drive
roll, the idle roll pressure is too great. Back the
adjustment knob out 1/2 turn, run new wire through
gun, and repeat above steps.
3. If the only result was drive roll slippage, loosen the
adjustment knob on the conductor plate and pull
the gun cable forward about 6" (15 cm). There
should be a slight waviness in the expose wire. If
there is not waviness, the pressure is too low.
Tighten the adjustment knob 1/4 turn, reinstall the
gun cable and repeat the above steps.
AVOIDING WIRE FEEDING
PROBLEMS
Wire feeding problems can be avoided by observing
the following gun handling procedures:
a. Do not kink or pull cable around sharp corners.
b. Keep the gun cable as straight as possible when
welding or loading electrode through cable.
c. Do not allow dolly wheels or trucks to run over
cables.
d. Keep cable clean by following maintenance instruc-
tions.
e. Use only clean, rust-free electrode. Lincoln elec-
trodes have proper surface lubrication.
f. Replace the contact tip when the arc starts to
become unstable or the contact tip end is fused or
deformed.
g. Keep wire reel spindle brake tension to the mini-
mum required to prevent excess reel over-travel
which may cause wire
“
loop-offs
”
from the coil.
h. Use proper drive rolls and wire drive/idle roll pres-
sure for wire size and type being used.
WARNING
Summary of Contents for POWER MIG 300
Page 43: ...DIMENSION PRINT F 5 POWER MIG 300 F 5 3 00F M19231 ...
Page 44: ...NOTES POWER MIG 300 ...
Page 45: ...NOTES POWER MIG 300 ...