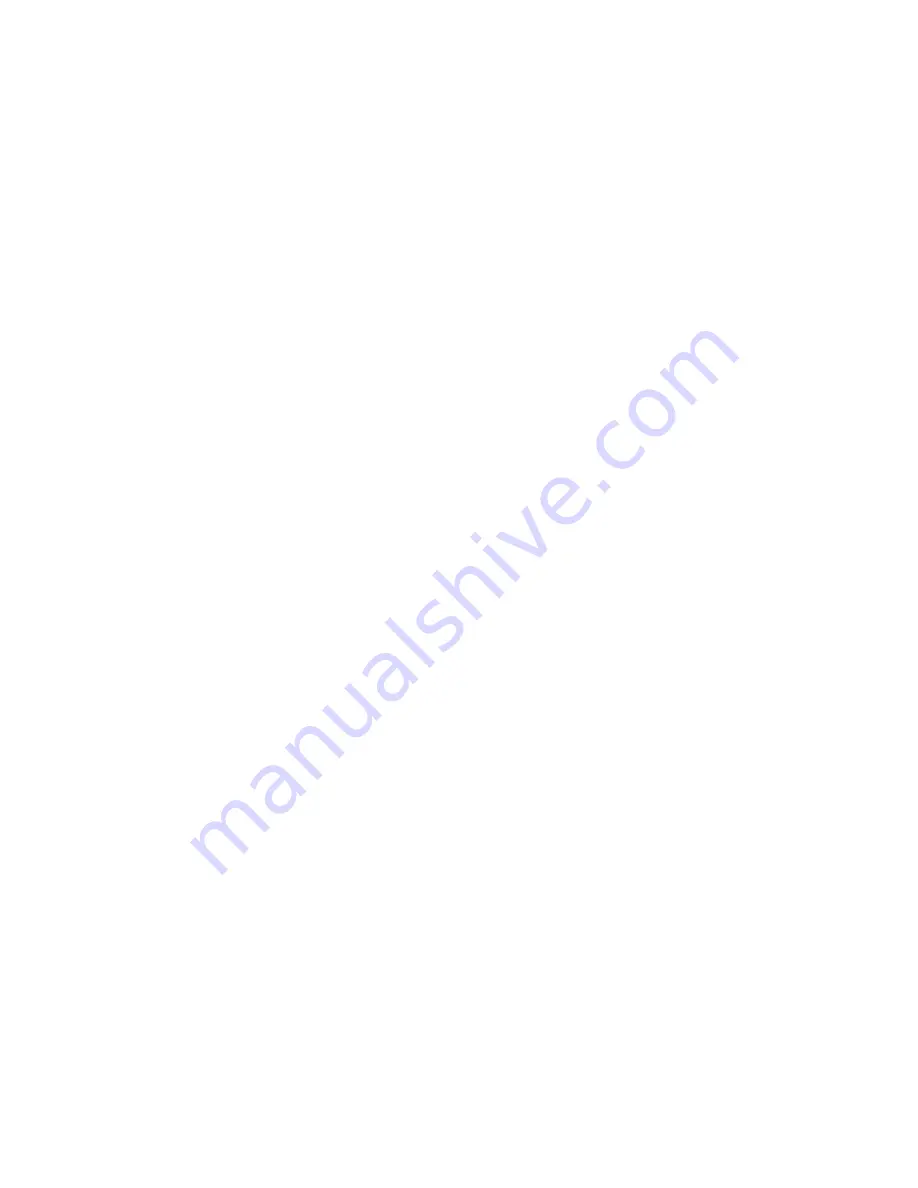
Impinger II –Advantage Service Manual - Domestic
11
Speed
Adjustment
Potentiometer
This is a 0 to 10 K ohm, 1 turn potentiometer. With
power off, remove the black and white pot leads
from the motor control board at terminals P1, P2.
Place the meter leads on the black lead (P2) and on
the white lead (P1). Rotating the pot., slowly, from
low to high, the meter readings should show an even
transition from 0 to 10 K ohms ± 5%. There should
be no dead or open spots through out the 1 turn of
the pot. Check both leads to ground. There should
be no continuity to ground. If any of the above
checks fail, replace the pot.
DC Motor Control Board
Check for 120 VAC input to the control board at
terminals L1 and L2. If not present, check wiring
back to the oven fan switch. If 120 VAC is present
at L1 and L2, check both fuses on control board (8A
line and 1A armature), check the VDC output at
terminals A+ and A-. If 120 VAC is present at
terminals L1 and L2 and DC voltage is present at
A+ and A-, but the motor does not run, check gear
motor as follows:
Conveyor Gear Motor
If DC voltage is present at A+ and A- and the motor
does not run, first check the mini breaker and then
the conveyor. Refer to the next possible cause.
Check the leads to the motor for evidence of any
shorts or opens, and each lead to ground. Check
motor brushes. From the top of the motor, rotate
motor shaft to determine if there is a locked rotor or
a locked gear box (use care so magnet and H.S.
board are not damaged). Replace motor as needed.
Conveyor
Check for any mechanical misalignment. Also,
check for worn bearings. A conveyor belt that is
over tightened will cause excessive bearing wear
and sometimes, irregular speed.
Conveyor speed varying or
intermittent
Power Supply
Check power supply at the DC control board for the
120 VAC at board terminals L1 and L2.
Motor Control Board
Place the test meter probes on terminals A+ and A-.
(With speed potentiometer set to maximum speed
(Approximately 2 min.) The meter reading should be
approximately 100 VDC (±3%), if voltage is not
steady within limits, then the board is probably bad.
Always check the speed pot., be sure it is okay
before changing a board. This test is not always
100% accurate as this test is not performed at
operating speeds. However, this test is the best
method currently available.
DC Gearmotor
If the DC control board is steady then the problem
may be the motor or gearbox. Check the brushes in
the motor for excessive arching and/or unusual
wear. Check the motor and gearbox from instruction
located on Page 11 under "possible cause" listing
"conveyor gear motor."
Magnet
Check to insure that the magnet (cemented to shaft
of conveyor drive motor) has not been damaged, or
come loose from motor shaft. Replace as needed.
Hall Effect Sensor
Check for any physical damage to hall effect sensor
(mounted on conveyor drive motor.) Check all wiring
and connections for damage. Check all connections
for tightness or proper location and check all wiring
for visible damage. Replace as needed. Connect
new hall effect to system and check for steady
operation.
Summary of Contents for Impinger II - Advantage Series
Page 5: ...Impinger II Advantage Service Manual Domestic 5 SCHEMATIC 1116 000 A 1117 000 A...
Page 6: ...Impinger II Advantage Service Manual Domestic 6 SCHEMATIC 1130 000 A 1131 000 A...
Page 7: ...Impinger II Advantage Service Manual Domestic 7 SCHEMATIC 1132 000 A 1133 000 A...
Page 25: ...Impinger II Advantage Service Manual Domestic 25 This page intentionally left blank...
Page 27: ...Impinger II Advantage Service Manual Domestic 27 BLOW UP GENERAL...
Page 29: ...Impinger II Advantage Service Manual Domestic 29 BLOW UP CONTROL BOX 1116 000 A 1117 000 A...
Page 33: ...Impinger II Advantage Service Manual Domestic 33 BLOW UP CONVEYOR DOOR...
Page 35: ...Impinger II Advantage Service Manual Domestic 35 BLOW UP OVEN BACK ASSEMBLY...
Page 36: ...Impinger II Advantage Service Manual Domestic 36...