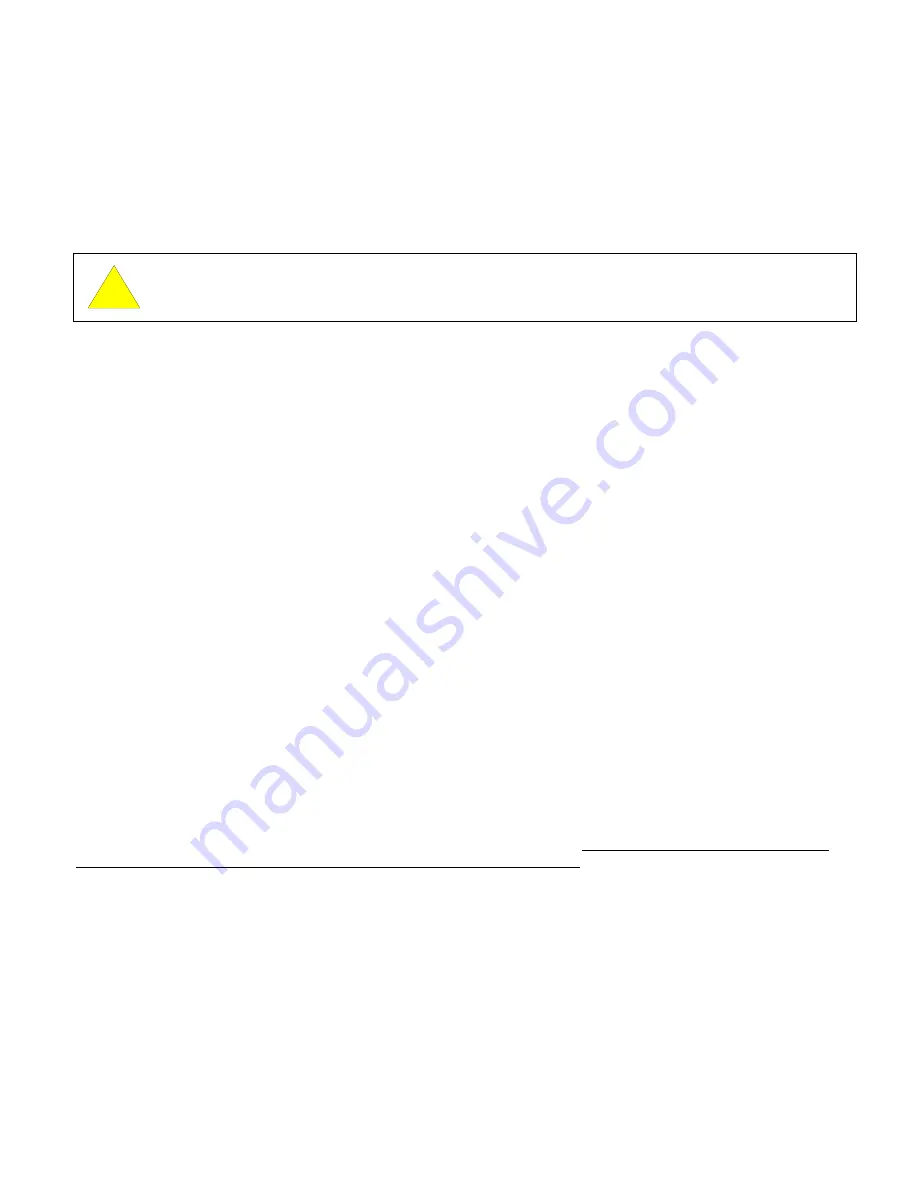
Impinger II – Installation & Operation Manual
11
Oven must be operated on an approved base only.
!
CAUTION:
SPACING
The oven must have 6 inches (152 mm) of clearance from combustible surfaces. In case other equipment is
located on the right side of oven, a minimum clearance of 24 inches (609 mm) is required from that equipment.
FOR ALL OVENS: A 24-inch (609 mm) clearance at the rear of the oven must be obtainable for service access.
FOR IMPINGER
®
II OVENS: A permanently installed (unmovable) oven requires a minimum of 4 feet clearance on
the right hand side to allow for conveyor removal, cleaning, and servicing.
NOTE: Do not install this (these) oven(s) in any area with an ambient temperature in excess of 95° F / 35° C.
Doing so will cause damage to the unit.
VENTILATION
A VENT IS REQUIRED: Local codes prevail. These are the “authority having jurisdiction” as stated by the
NATIONAL FIRE PROTECTION ASSOCIATION, INC. in NFPA 96 latest edition. In addition, to be in compliance
with the NFPA 54 Section 10.3.5.2, this unit must be installed with a ventilation hood interlock that prevents the unit
from operating when the ventilation hood is off. For further ventilation information, see below.
VENTILATION GUIDELINES
A ventilation hood is required to remove heat and cooking odors. For gas ovens, a ventilation hood is also required
to remove the products of combustion. The hood and HVAC installation must meet local codes to gain approval by
the authority having jurisdiction. Requirements may vary throughout the country depending on the location by city,
county, and state. Obtain information from the authority having jurisdiction to determine the requirements for your
installation. Obtain information and review copies of codes or documents that will be used to inspect and approve
your installation. Your ventilation hood supplier and HVAC contractor should be contacted to provide guidance. A
properly engineered and installed ventilation hood and HVAC system will expedite approval and reduce oven
maintenance costs. Proper ventilation is the oven owner’s responsibility.
The ventilation hood must operate in harmony with the building HVAC system. It typically requires between 750
and 2500 CFM exhaust. (The “Efficiency” of various hood designs makes it necessary to specify such a wide range
of ventilator CFM.) Make up air must be supplied by either a hood design or the HVAC system. This will vary with
hoods from various manufacturers.
CAUTION: Prevent airflow through the cooking tunnel. Air must NOT be directed onto the oven front or at
side of cooking area or rear of oven.
Performance will be evaluated during Start-up Checkout by conducting a smoke candle test. The hood must
capture all smoke from the oven. This is required to assure proper performance of the oven and to eliminate
additional service calls that occur when ambient temperatures are too high. In all cases, the ambient temperature
around the oven must be less than 95° F / 35° C when the oven is operating. In certain localities, other chemical or
gaseous methods of detecting adequate capture will be the requirement to meet the local code authority.
The drawing shown on the next page is a typical installation and is intended to be a guideline. It is not a rigid
specification. Hood dimensions and the positioning of the hood over the oven will vary with hood manufacturers.
NOTE: Lincoln can provide oven spec sheets that show the dimensions of the oven, KW or BTU ratings and other
information that will be useful to both the ventilation hood supplier and the HVAC contractor.
IN AUSTRALIA:
Refer to Standard AS 5601. This standard specifies the requirements for piping, flueing,
ventilation and appliance installation associated with use of or intended use of fuel gases. The requirements of AS
5601 are to be used in conjunction with, but do not take precedence over, any statutory regulations that may apply
in any area.