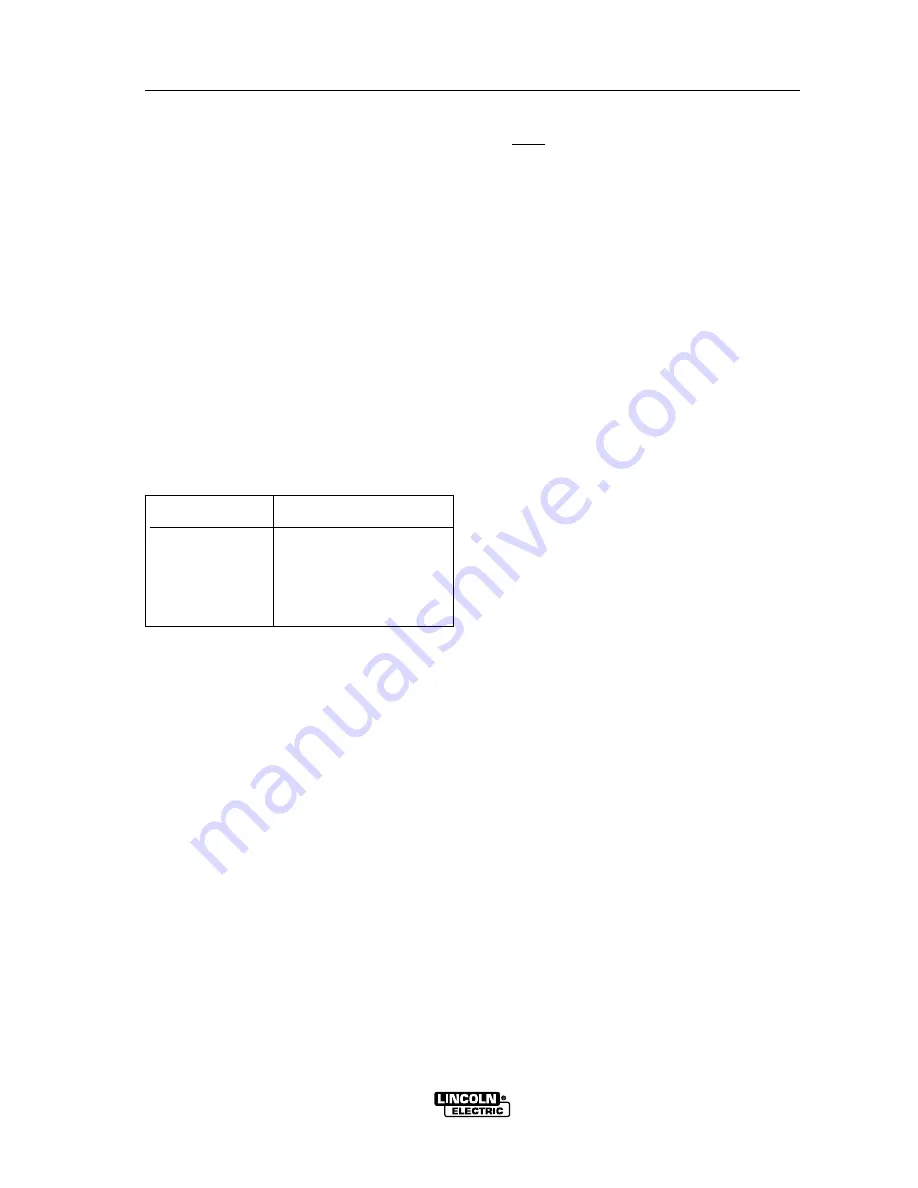
CV-WIRE MODE
Connect a wire feeder to the Vantage and set welder controls
according to the instructions listed earlier in this section.
The Vantage in the ”CV-WIRE” position, permits it to be used with
a broad range of flux cored wire (Innershield and Outershield)
electrodes and solid wires for MIG welding (gas metal arc
welding). Welding can be finely tuned using the “ARC
CONTROL”. Turning the ARC CONTROL clockwise from -
10(soft) to +10(crisp) changes the arc from soft and washed-in to
crisp and narrow. It acts as an inductance/pinch control. The
proper setting depends on the procedure and operator
preference. Start with the knob set at 0.
Note:
The 42V/115V Wire Feeder voltage switch position must
match voltage requirement of Wire Feeder.
For any electrodes the procedures should be kept within the
rating of the machine. For additional electrode information, See
www.lincolnelectric.com or the appropriate Lincoln publication.
ARC GOUGING
For optimal performance when arc gouging, set the Vantage
“WELD MODE” switch to the “CC - STICK” position, and the
“ARC CONTROL” to 10.
Set the “OUTPUT” knob to adjust output current to the desired
level for the gouging electrode being used according to the
ratings in the following table:
* Maximum current setting is limited to the Vantage maximum of
575 Amps.
PARALLELING
When paralleling machines in order to combine their outputs, all
units must be operated in the CC-STICK mode only at the same
output settings. To achieve this, turn the WELD MODE switch to
the CC-STICK position. Operation in other modes may produce
erratic outputs, and large output imbalances between the units.
AUXILIARY POWER OPERATION
Start the engine and set the IDLER control switch to the desired
operating mode. Full power is available regardless of the welding
control settings, if no welding current is being drawn.
The auxiliary power of the Vantage consists of two 20 Amp-380V
receptacle and one 220V receptacles.
The auxiliary power capacity is 10,000 watts of 50 Hz, single
phase power or 12,000 watts of 50Hz, three phase power. The
auxiliary power capacity rating in watts is equivalent to volt-
amperes at unity power factor. The maximum permissible current
of the 380 VAC output is 18.8 A. Output voltage is within ± 10%
at all loads up to rated capacity.
NOTE:
The 220V receptacles are connected to different phases
and cannot be paralleled.
The auxiliary power receptacles should only be used with three
wire or four wire earth type plugs or approved double insulated
tools with two wire plugs.
The current rating of any plug used with the system must be at
least equal to the current capacity of the associated receptacle.
SIMULTANEOUS WELDING AND AUXILIARY
POWER LOADS
It must be noted that the above auxiliary power ratings are with
no welding load. Simultaneous welding and power loads are
specified in table B.4. The permissible currents shown assume
that current is being drawn from either the 220VAC or 380VAC
supply (not both at the same time).
ELECTRODE
CURRENT RANGE
DIAMETER
(DC, electrode positive)
3.2mm (1/8”)
30-60 Amps
4.0mm (5/32”)
90-150 Amps
4.8mm (3/16”)
200-250 Amps
6.4mm (1/4”)
300-400 Amps
8.0mm (5/16”)
350-450 Amps
10mm (3/8”)
450-575 Amps*
B-8
OPERATION
B-8
Vantage 575
Summary of Contents for VANTAGE 575 CUMMINS
Page 37: ...Vantage 575 F 2 DIAGRAMS F 2 CONNECTION DIAGRAM...
Page 39: ...F 4 DIAGRAMS F 4 Vantage 575 CONNECTION DIAGRAM...
Page 40: ...Vantage 575 F 5 DIAGRAMS F 5 CONNECTION DIAGRAM...
Page 42: ...Vantage 575 F 7 DIAGRAMS F 7 CONNECTION DIAGRAM...
Page 43: ...Vantage 575 F 8 DIAGRAMS F 8 CONNECTION DIAGRAM...
Page 45: ...Vantage 575 F 10 DIAGRAMS F 10 CONNECTION DIAGRAM...
Page 46: ...Vantage 575 F 11 DIAGRAMS F 11 CONNECTION DIAGRAM...
Page 47: ...Vantage 575 F 12 DIAGRAMS F 12 CONNECTION DIAGRAM...
Page 48: ...Vantage 575 F 13 DIAGRAMS F 13 CONNECTION DIAGRAM...
Page 50: ...NOTES Vantage 575...
Page 51: ...NOTES Vantage 575...