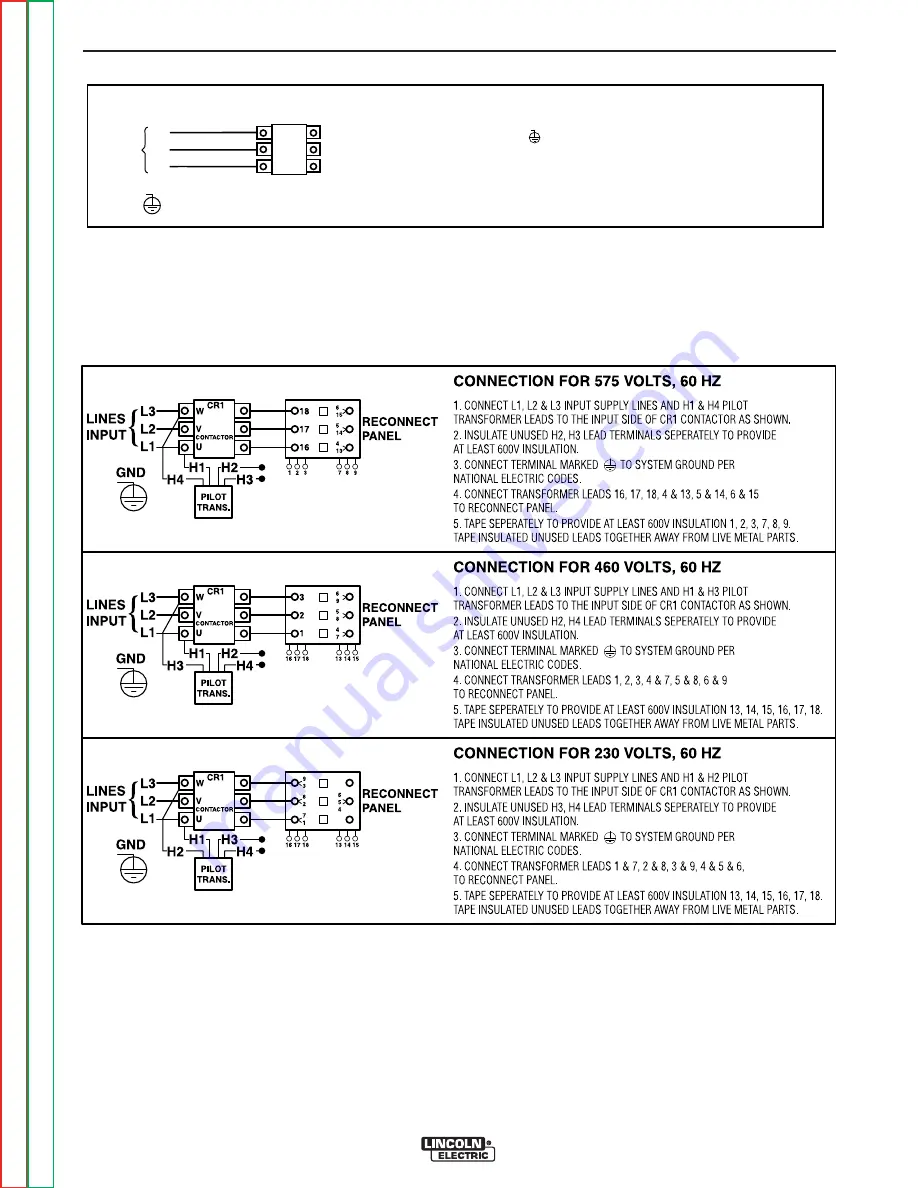
INSTALLATION
A-7
A-7
DC-600
Retur
n
to
Section
T
OC
Retur
n
to
Section
T
OC
Retur
n
to
Section
T
OC
Retur
n
to
Section
T
OC
Retur
n
to
Master
T
OC
Retur
n
to
Master
T
OC
Retur
n
to
Master
T
OC
Retur
n
to
Master
T
OC
FIGURE A.7-Reconnect Panel Board Positions for Single Voltage Machines
L3
L2
L1
LINES
INPUT
GND
SEE MACHINE RATING PLATE FOR REQUIRED INPUT SUPPLY VOLTAGE
1. TURN OFF THE INPUT POWER USING THE DISCONNECT SWITCH AT THE FUSE BOX
2. CONNECT TERMINAL MARKED TO GROUND PER NATIONAL ELECTRIC CODES.
3. CONNECT THE L1, L2, & L3 INPUT SUPPLY LINES TO INPUT SIDE OF THE CRI CONTACTOR AS SHOWN.
W
V
U
CONTACTOR
CRI
FIGURE A.8-Reconnect Panel Board Positions for 230/460/575 VAC Machines