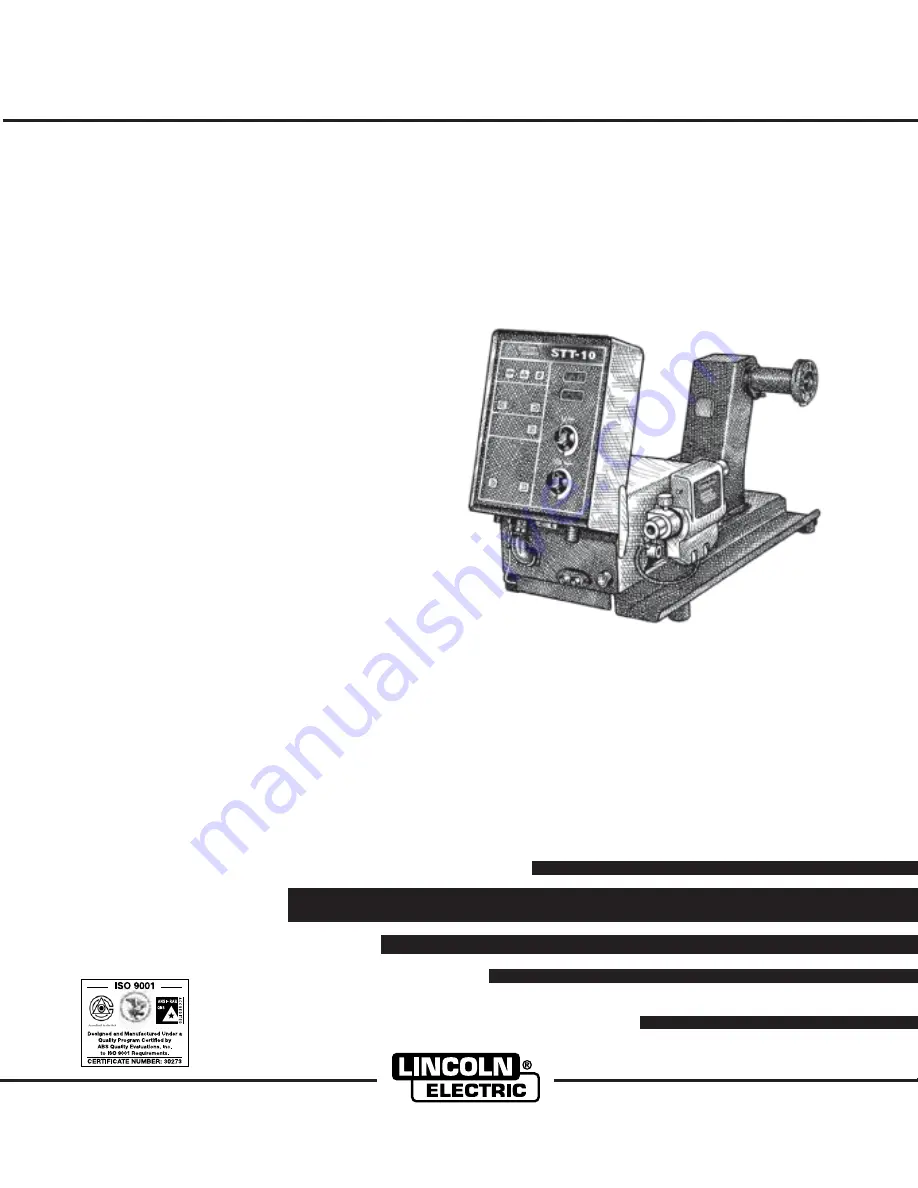
STT-10 Head & Controls
Boom Mount or Bench Models
OPERATOR’S MANUAL
IM586-B
August, 2007
Safety Depends on You
Lincoln arc welding and cutting
equipment is designed and built
with safety in mind. However, your
overall safety can be increased by
proper installation ... and thought-
ful operation on your part.
DO
NOT INSTALL, OPERATE OR
REPAIR THIS EQUIPMENT
WITHOUT
READING
THIS
MANUAL AND THE SAFETY
PRECAUTIONS CONTAINED
THROUGHOUT.
And,
most
importantly, think before you act
and be careful.
For use with: STT-10 Control - Boom Mount Code 10447, 10832
10 Series Wire Drive - Boom Mount Code 10443, 10763, 10818
STT-10 Boom Package Code 10448
Synergic 7F Wire Drive Code 10190, 10191
STT-10 - Bench Model Code 10446, 10766, 10821
STT-10 - Zipline Boom Package Code 10499, 10500, 10773
• Sales and Service through Subsidiaries and Distributors Worldwide •
Cleveland, Ohio 44117-1199 U.S.A. TEL: 216.481.8100 FAX: 216.486.1751 WEB SITE: www.lincolnelectric.com
• World's Leader in Welding and Cutting Products •
Copyright © 2007 Lincoln Global Inc.
Summary of Contents for STT-10
Page 42: ...F 4 CONNECTION DIAGRAMS F 4 STT 10 ...
Page 46: ...NOTES STT 10 ...
Page 47: ...NOTES STT 10 ...