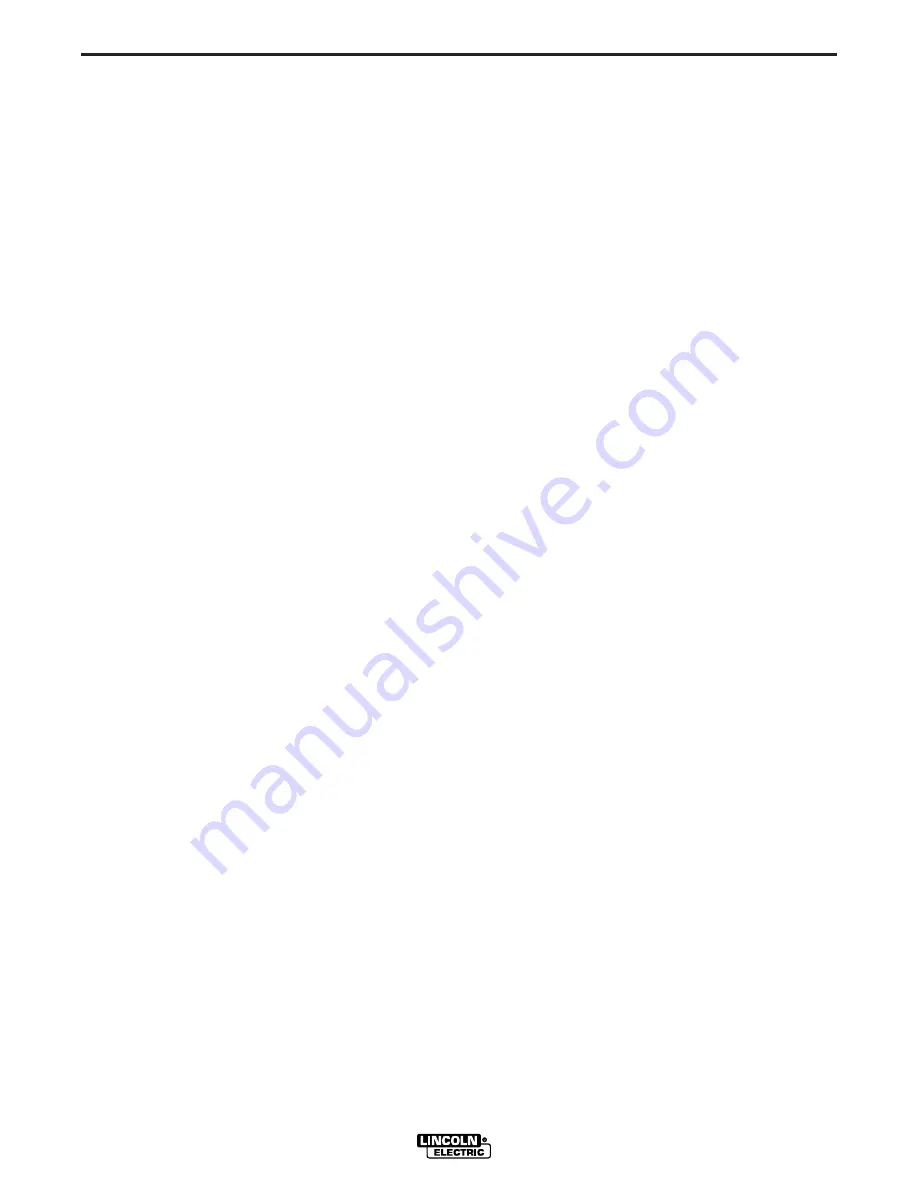
B-3
OPERATION
B-3
COMMON WELDING PROCEDURES
Set the oscillation speed and the rear and front dwell
times as called for in the welding procedure. The front
dwell time controls the dwell when the nozzle is at the
proximity sensor farthest from the Spreadarc mount-
ing bracket (right-side when facing the Spreadarc
User Interface). The rear dwell time controls the dwell
when the nozzle is at the proximity sensor closest to
the Spreadarc mounting bracket (left-side when facing
the Spreadarc User Interface). The oscillation dis-
tance, or sweep length, is controlled by rotating either
or both of the proximity sensor stops as required giv-
ing proper front and rear electrode position. After the
desired oscillation track is obtained, lock the stops in
place by tightening the hex nuts against the stops.
In order to protect the Spreadarc from high tempera-
tures, best welding practices would be to set the travel
direction such that the unit moves away from the heat
of the arc, instead of over it.
SPREADARC