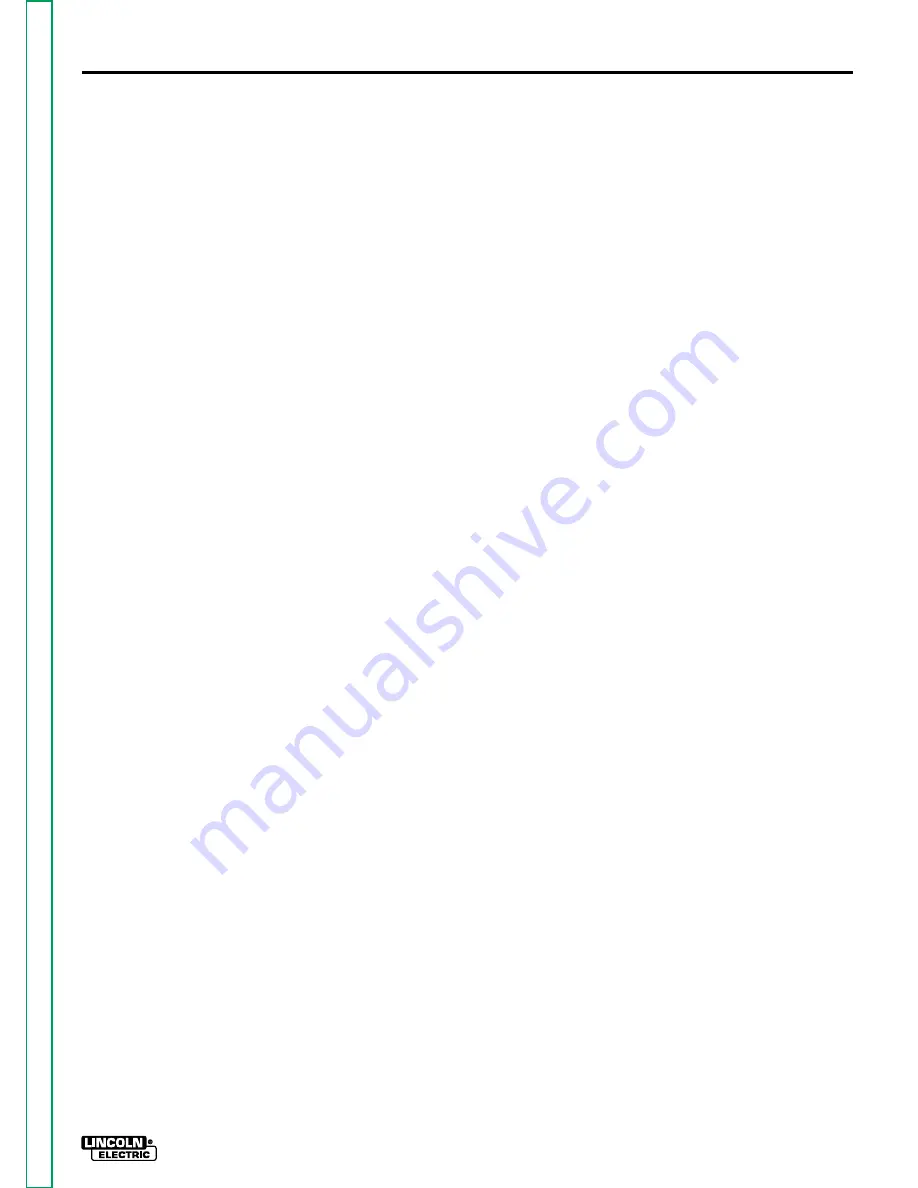
Return to Master TOC
Return to Master TOC
Return to Master TOC
Return to Master TOC
SP-100
TABLE OF CONTENTS
– OPERATION SECTION –
Operation ...........................................................................................................Section B
Safety Precautions ......................................................................................................B-1
General Description ....................................................................................................B-2
Recommended Processes.....................................................................................B-2
Operational Features and Controls........................................................................B-2
Design Features and Advantages .........................................................................B-2
Welding Capability ................................................................................................B-2
Limitations .............................................................................................................B-2
Controls and Settings...................................................................................................B-2
Welding Operations......................................................................................................B-3
Process Guidelines................................................................................................B-3
Sequence of Operations ........................................................................................B-3
Wire Loading..........................................................................................................B-3
Friction Brake Adjustments....................................................................................B-4
Wire Threading ......................................................................................................B-4
Shielding Gas .......................................................................................................B-5
Making a Weld ......................................................................................................B-5
Cleaning Tip and Nozzle........................................................................................B-6
Changing Machine Over To Feed Other Wire Sizes .............................................B-6
Welding With Innershield .......................................................................................B-6
Overload Protection .....................................................................................................B-6
Output Overload ....................................................................................................B-6
Thermal Protection ................................................................................................B-6
Wire Feed Overload Protection ............................................................................B-6
Section B