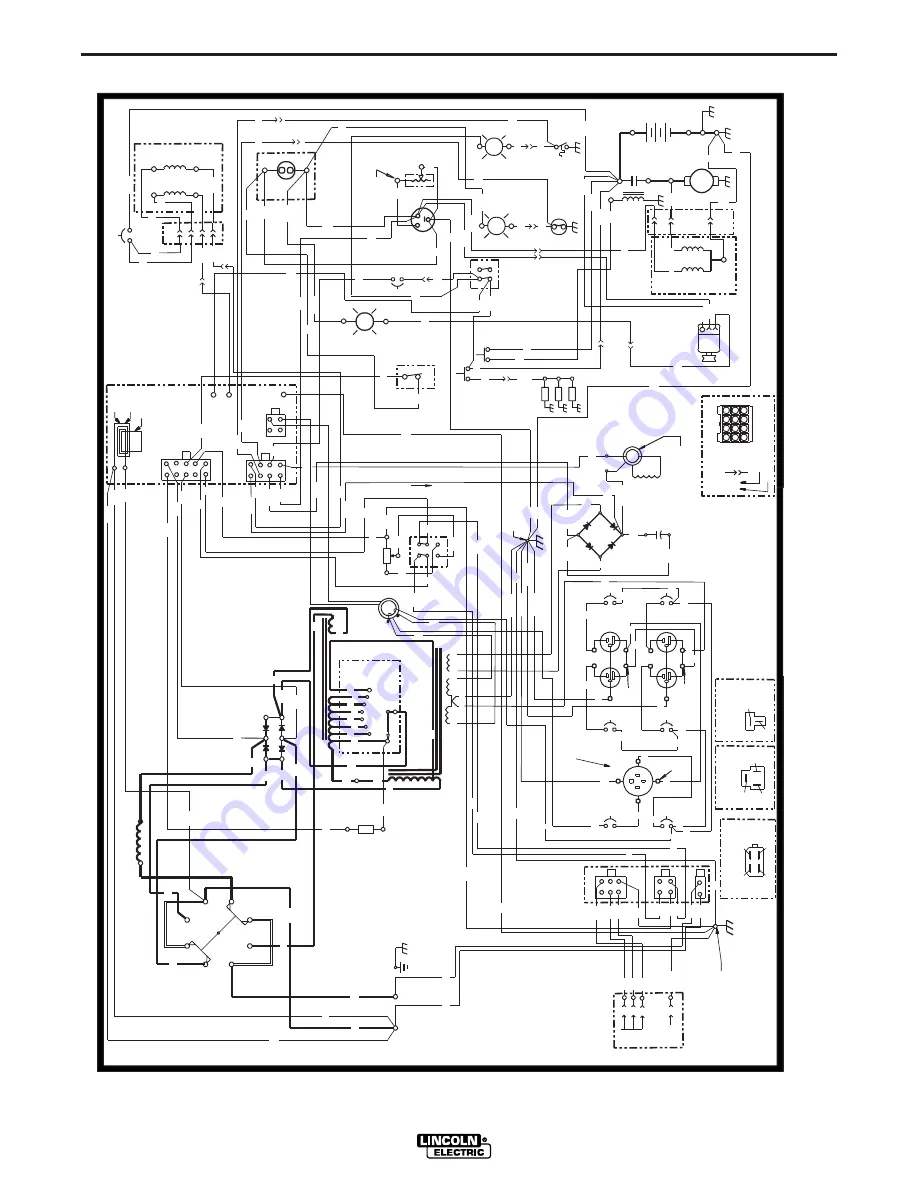
F-8
WIRING DIAGRAM
F-8
RANGER 300 D AND 300 DLX
67
75A
3C
PCB2
BYPASS PC
4
1
76B
2
J10
227
76A
5E
4
BLACK
BLACK
11
RECEPTACLE
3B
125/250V. SINGLE
BLACK
BLACK
BLACK
BLACK
3F
3A
3B
201
B
1J10
2J10
222B
225
223
3J10
HIGH
GLOW PLUG
GLOW PLUGS
FLASHING CURRENT
5
AC
9
15A
50A
77B
201
CB2
75B
3
CB7
15A
J10
5
W4
254
TERMINALS
5L
GREEN
GND-C
5H
ENGINE GROUND
5H
PULL
HOLD
L3
FUEL
IG
L
ALTERNATOR
INDICATES JACK NUMBER
1J10
INDICATES CAVITY NUMBER
GREEN
75A
R3
MAX
10K POT
75
CW
76D
77
RHEOSTAT
RED
J3
214
200B
219
224
A1
R1
W12
R
ENGINE HARNESS CONNECTOR TO PANEL HARNESS
GND
5E
15A
5K
222G
214
240
221
BOARD
PCB1
254B
254A
254
224D
222
213B
5F
214B
15A
77
BATTERY
214A
213A
227A
SWITCH
SHOWN IN
"HIGH"
POSITION
AUTO
235
224F
5F
250
222D
3G
GND-G
J8
120/240V
CB5
15A
3C
BLACK
12
76A
3A
77A
76B
75B
GND-B
5F
J11
J7
5D
75A
BLACK
FUEL SHUTDOWN SOLENOID (HARNESS LEAD END)
GROUND SCREW
IDLER SOLENOID (HARNESS LEAD END)
ABOVE AMPHENOL HOLE
3H
GND-G
5A
WHITE
WHITE
WHITE
COLORED
TERM.
SILVER
WHITE
BLACK
BLACK
ALTERNAT0R CONNECTION BLOCK (HARNESS LEAD END)
224A
222F
213
(+)
239
W15
W1
200A
OUTPUT
D2
ROTOR FIELD
(+)
(-)
BLACK
BLACK
CB6
5D
5L
J9
ELECTRODE
3E
J13
J12
227
224B
237
WORK
DC+
S1
SWITCH
75
76
5W
GAUGE
226
SENDER
"SIG" TERMINAL
224E
+
240
222
224
CHARGER
SENSOR
254C
IDLER WELD
CURRENT
COIL
COIL
PULL
RED
L2
WHITE
-
BLACK
J11
R
TEMP.
WATER
220B
221C
12 VOLT
BATTERY
+
222E
220C
TEMP.
WATER
OIL
224E
224
S
CRANK
MOTOR
WHITE
COIL
COIL
SOLENOID
5E
67
21A
NOTES:
ELECTRICAL SYMBOLS PER E1537
ALL CASE FRONT COMPONENTS VIEWED FROM REAR.
GROUND
J12
FRAME
(-)
BLACK
J13
SHUTDOWN
220A
235B
CONTACTOR
237
5K
5K
REMOTE SWITCH
L1
(CHOKE)
W6
224G
R
224H
5G
221A
225
R
6J10
STARTER
SOLENOID
COIL
S5
SWITCH
IDLER
224B
222
RED
S4
S3
START
222G222G
SWITCH
223A
ON/OFF
S6
5B
PRESSURE
235A
222C
FUEL
8J10
FUEL
9J10
235C
235B
BLUE
221B
CB9
(+)
222D
11J10
220
222B
BLUE
STARTER
ELECTRODE POLARITY
77B
REMOTE CONTROL
AC
DC-
AC
DC-
DC+
OUTPUT
D1
W11
RECTIFIER
R2
W16
50 W
25 OHM
77A
1
R3
3
SWITCH
C1
5
77D
S8
76
3D
3D
PC
CB8
15A
BLACK
BLACK
222E
222F
222J
222K
222H
HIGH
HOLD
SPEED
SOLENOID
5G
224F
ENGINE
HOUR METER
5H
SENSOR
CURRENT
IDLER AC
(-)
5
200B
7
201A
W7
5M
5M
W10
213
RED
BLACK
GND-D
200
RED
6
POSITIVE SLIP
RING NEAREST
LAMINATION
3
GND-E
BLACK
J5
201A
120 V
11
BLACK
R2
12J10
10
5
8
4
5A
2
J1
214
1
A2
REACTOR
C1
221
241
A1
W12
236
(-)
7J10
SWITCH
OIL PRESSURE
SWITCH
"ON" POSITION
10J10
SHOWN IN
SWITCH
222A
236
239
5J10
4J10
67
3
224A
12
11
10
9
8
5
1
24
219
(-)
RINGS
(+)
5A
BLOWER BAFFLE
C1
CB4
800 MFD
(SHOWN IN
REMOTE POSITION)
7
A
GND-E
STATOR
SILVER
COLORED
C
GROUND
AMPHENOL
R6
R4
R7
R5
RANGE
S2
76A
W1
76D
77A
9
6
GROUND SCREW
3
WIRING DIAGRAM - RANGER 300 D
GND-C
CB3
50A
254A
W10
L10556
9-12-97A
77
6
3
TERMINALS
B
77A
76A
3
J6
F
W2
21A
GREEN
120 V
SILVER
COLORED
5B
(+)
SLIP
(+)
RED
AC
GND-D
6
3 TURNS
W7
W11
J2
250
1
6
220
200B
W4
4
201A
235
254B
A2
1
W9
3
NOTE: This diagram is for reference only. It may not be accurate for all machines covered by this manual. The specific diag
ram for a particular code is pasted inside
the machine on one of the enclosure panels. If the diagram is illegible, write to the Service Department for a replacement. G
ive the equipment code number..
Summary of Contents for RANGER 300 D
Page 5: ...iv SAFETY iv ...
Page 51: ...NOTES RANGER 300 D AND 300 DLX ...