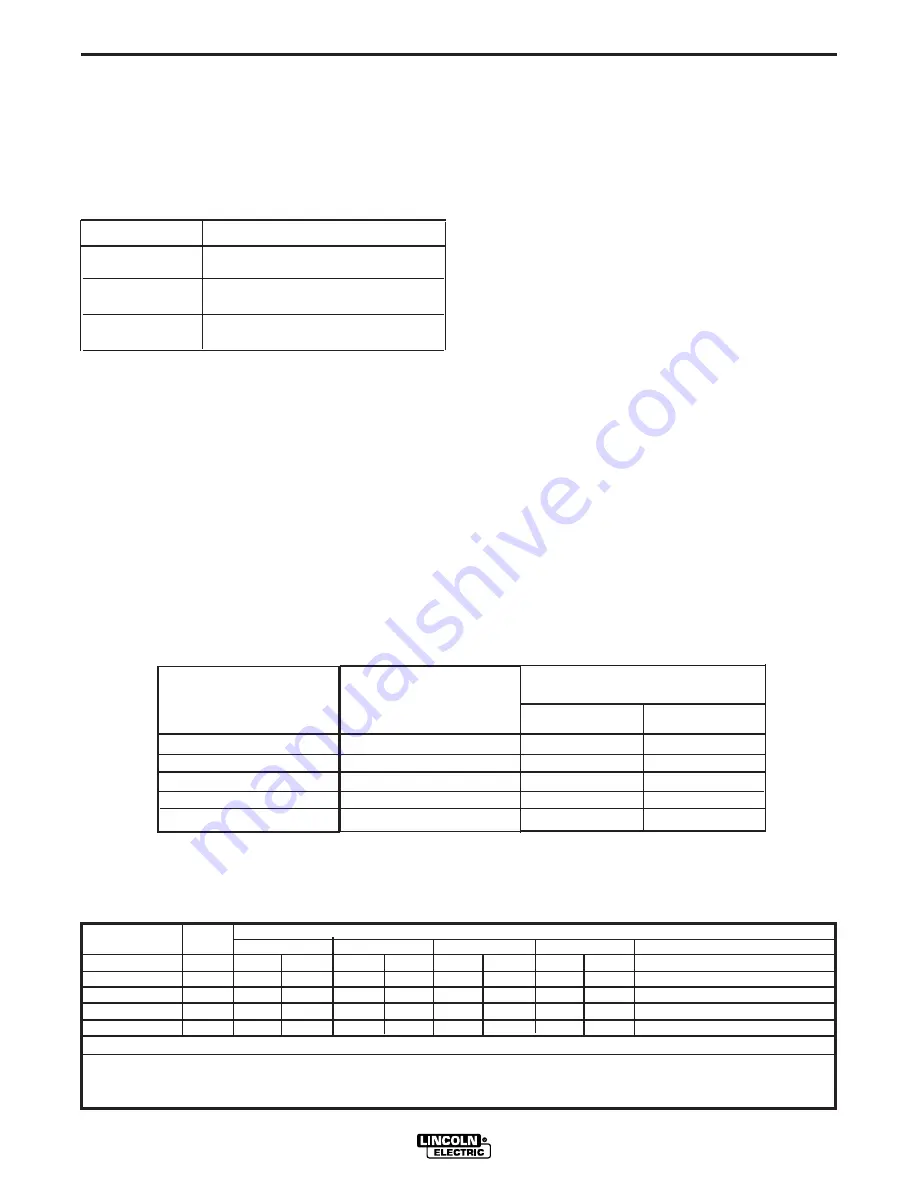
B-6
OPERATION
B-6
ARC GOUGING
The RANGER 250 LPG can be used for limited arc
gouging. For optimal performance, set the MODE
switch to CC-STICK and the ARC CONTROL to +10.
Set the CONTROL knob to adjust output current to the
desired level for the gouging electrode being used
according to the ratings in the following table:
Electrode Diameter Current Range (DC, electrode positive)
1/8" (3.2mm) 30-60 Amps
5/32" (4.0mm) 90-150 Amps
3/16" (4.0mm) 200-250 Amps
AUXILIARY POWER:
Start the engine and set the IDLER control switch to
the desired operating mode. Full power is available
regardless of the welding control settings providing no
welding current is being drawn.
The auxiliary power of the RANGER 250 LPG con-
sists of two 20 Amp-120 VAC (5-20R) GFCI duplex
receptacles and one 50 Amp 120/240 VAC (14-50R)
receptacle. The 240 VAC receptacle can be split for
single phase 120 VAC operation. If a GFCI receptacle
is tripped, See the MAINTENANCE section for
detailed information on testing and resetting the GFCI
receptacle.
The auxiliary power capacity is 9,000 Watts Peak,
8000 Watts Continuous of 60 Hz, single phase power.
The auxiliary power capacity rating in watts is equiva-
lent to volt-amperes at unity power factor. The max
permissible current of the 240 VAC output is 33 Amps.
The 240 VAC output can be split to provide two sepa-
rate 120 VAC outputs with a max permissible current
of 33 Amps per output to two separate 120 VAC
branch circuits (these circuits cannot be paralleled).
Output voltage is within ± 10% at all loads up to rated
capacity. All auxiliary power is protected by circuit
breakers.
The 120 V auxiliary power receptacles should only be
used with three wire grounded type plugs or approved
double insulated tools with two wire plugs. The current
rating of any plug used with the system must be at
least equal to the current capacity of the associated
receptacle.
NOTE: The 240 V receptacle has two circuits, each of
which measure 120 V to neutral but are of opposite
polarities and cannot be paralleled.
Simultaneous Welding and Auxiliary Power Loads
The above auxiliary power ratings are with no welding
load. Simultaneous welding and power loads are
specified in the following table. The permissible cur-
rents shown assume that current is being drawn from
either the 120 VAC or 240 VAC supply (not both at the
same time).
RANGER 250 LPG
Welding
Output-Amps
0
100
150
200
250
Permissible Power-Watts
(Unity Power Factor)
8000
5300
4000
2700
750
Permissible
Current in
@120 VAC *
66**
48**
38**
24
8
Auxiliary
-Amps
@ 240 VAC
33
24
19
12
4
* Each duplex receptacle is limited to 20 amps.
** Not to exceed 35 A per 120 VAC branch circuit when splitting the 240 VAC output.
RANGER 250 LPG Simultaneous Welding and Power Loads
RANGER 250 LPG Extension Cord Length Recommendations
(Use the shortest length extension cord possible sized per the following table.)
Current
(Amps)
15
20
15
20
33
Voltage
Volts
120
120
240
240
240
Load
(Watts)
1800
2400
3600
4800
8000
30
60
(9)
(18)
40
30
75
60
(12)
(9)
(23)
(18)
75
50
150
100
60
(23)
(15)
(46)
(30)
(18)
125
88
225
175
100
(38)
(27)
(69)
(53)
(30)
175
138
350
275
175
(53)
(42)
(107)
(84)
(53)
300
225
600
450
250
(91)
(69)
(183)
(137)
(76)
Maximum Allowable Cord Length in ft. (m) for Conductor Size
Conductor size is based on maximum 2.0% voltage drop.
14 AWG
12 AWG
10 AWG
8 AWG
6 AWG
4 AWG
Summary of Contents for RANGER 250 LPG
Page 36: ...F 1 DIAGRAMS F 1 RANGER 250 LPG ...
Page 37: ...F 2 DIAGRAMS F 2 RANGER 250 LPG ...
Page 38: ...F 3 DIAGRAMS F 3 RANGER 250 LPG ...
Page 39: ...F 4 DIAGRAMS F 4 RANGER 250 LPG ...
Page 40: ...F 5 DIAGRAMS F 5 RANGER 250 LPG ...
Page 42: ...F 7 DIAGRAMS F 7 RANGER 250 LPG ...
Page 43: ...F 8 DIAGRAMS F 8 RANGER 250 LPG ...
Page 44: ...F 9 DIAGRAMS F 9 RANGER 250 LPG ...
Page 45: ...F 10 DIAGRAMS F 10 RANGER 250 LPG ...
Page 48: ...NOTES RANGER 250 LPG ...
Page 49: ...NOTES RANGER 250 LPG ...