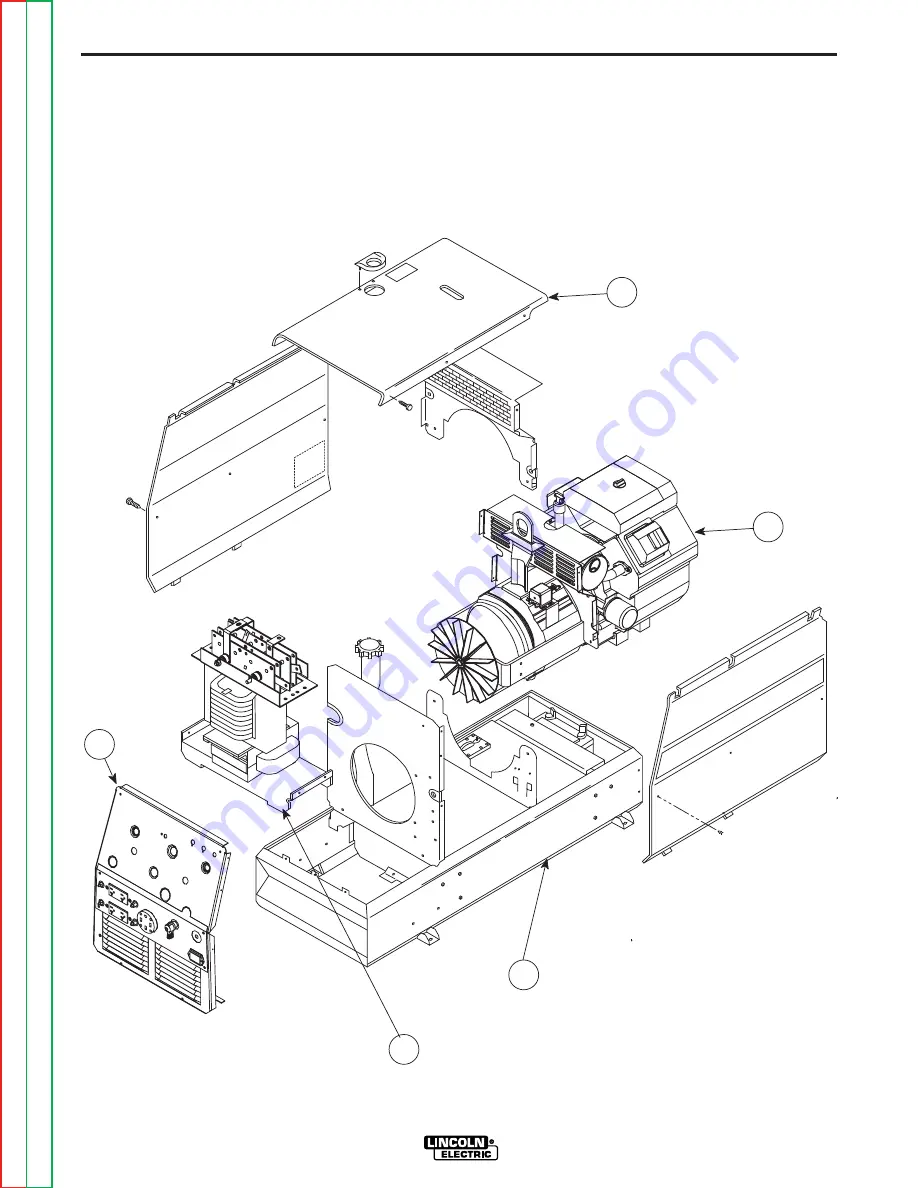
RANGER® 10,000 & RANGER® 10,000 PLUS
MAINTENANCE
D-6
D-6
FIGURE D.1 - MAJOR COMPONENT LOCATION
44
11
33
55
22
1. CASEFRONT
2. OUTPUT RECTIFIER ASSEMBLY
3. BASE/UNDERCARRIAGE ASSEMBLY
4. ENGINE/ROTOR/STATOR ASSEMBLY
5. CASE TOP & SIDES
Retur
n
to
Section
TOC
Retur
n
to
Section
TOC
Retur
n
to
Section
TOC
Retur
n
to
Section
TOC
Retur
n
to
Master
TOC
Retur
n
to
Master
TOC
Retur
n
to
Master
TOC
Retur
n
to
Master
TOC