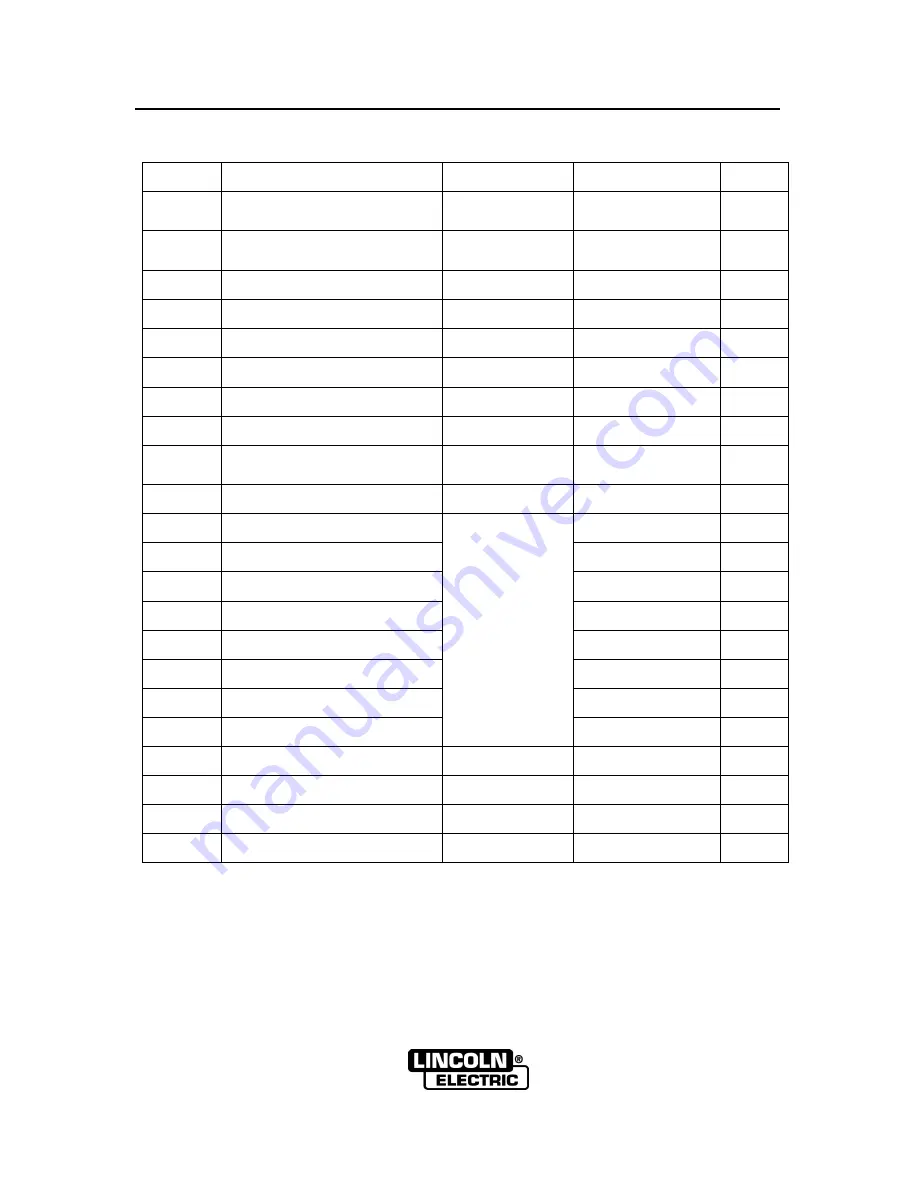
E-7
PARTS LIST
E-7
PWF
TM
-4 REPLACEMENT PARTS
Number
Description
Specification
Part number
QTY
1
Gun
Connector(PWF-4/-4PLUS)
KP61232
1
2
Outlet Guide
See consumable
parts
1
3
Bracket
KP61234
1
4
Insulated Sheath
KP61235
2
5
Straight Pin
Φ3X16
KP61236
6
6
Insulator
KP61237
3
9
Inlet Guide
0.8-2.0mm
KP61238
1
14
Straight Key
5X5X10
KP61239
1
19
Drive Roll
See consumable
parts
2
21
M10 Nut and washer
KP61241
各
2
22
Pressure Roll
KP61107-4
KP61242
2
24
Pin
KP61243
2
25
Pressure Arm
(
right
)
KP61244
2
27
Handle Pin
KP61246
1
28
Pressure Arm Screw
KP61247
1
29
Plain Washer
KP61248
2
30
Pressure Washer
KP61249
1
32
Adjustive Handle
KP61251
1
26
Pressure Arm
(
left
)
KP61245
2
36
Intermediate Guide
0.8-2.0mm
KP61252
1
37
Bracket Insulation Plate
KP61253
2
38
Feeder Motor
120SN10-CQ
KP61254
1