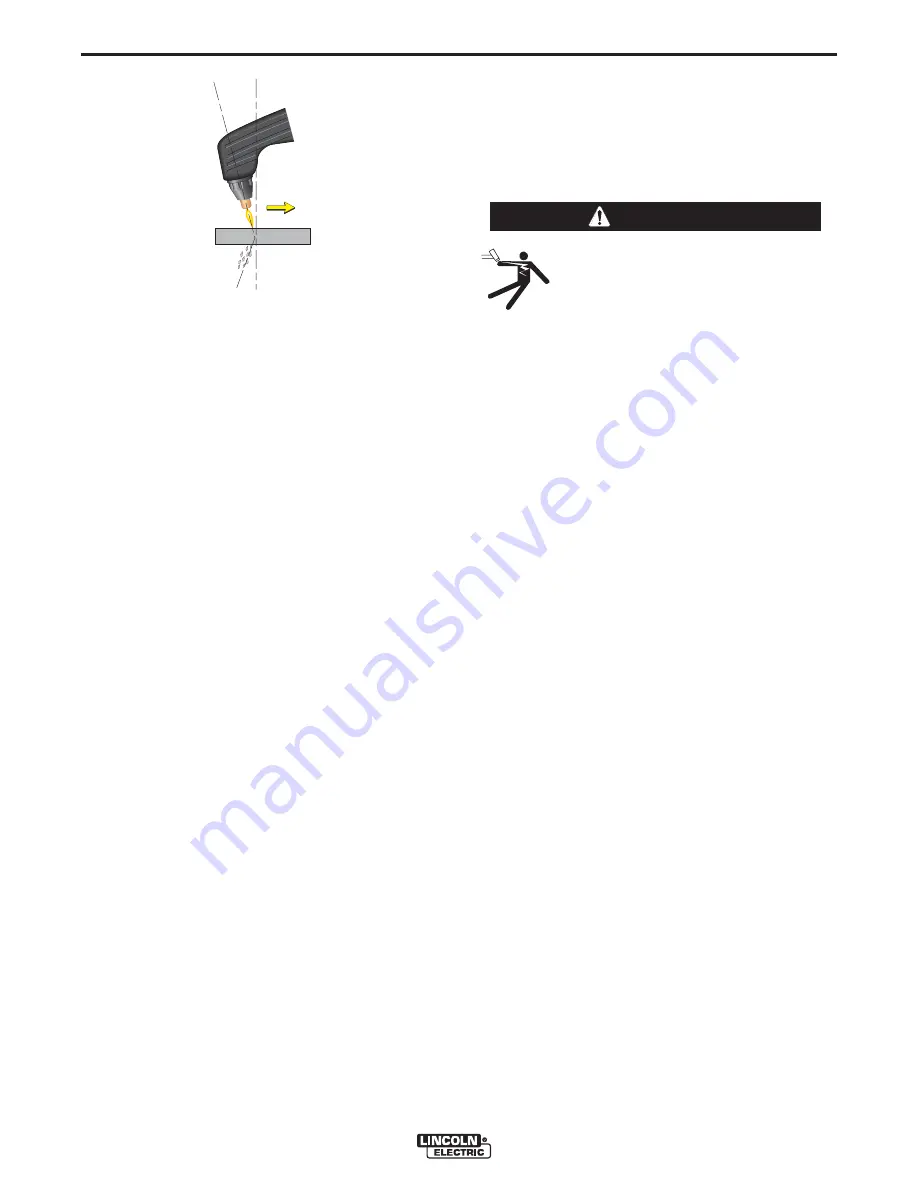
Direction of Travel
5
°
- 15
°
10
°
- 20
°
Arc Lag
Leading Angle
B-5
OPERATION
B-5
• Use a 5° - 15° leading angle in the direction of the cut.
• Finish the cut to be made and release the trigger.
• When the trigger is released, the arc will stop.
- The gas will continue to flow for 10 seconds of
postflow. If the trigger is activated within this time
period, the pilot arc will immediately restart.
• If the dross is difficult to remove, reduce the cutting
speed. High speed dross is more difficult to remove
than low speed dross.
• The right side of the cut is more square than the left
as viewed along the direction of travel.
• Clean spatter and scale from the nozzle frequently.
• If the "SAFETY" LED lights at any time; check the
following:
• Check the assembly of the torch consumables. If
they are not properly in place, the machine will
not start.
Make sure that the shield cup is hand
tight. Do not use pliers or over tighten.
• Check the conditions of the inside of the nozzle. If
debris has collected, rub the electrode on the
inside bottom of the nozzle to remove any oxide
layer that may have built up. Refer to
"Suggestions for Extra Utility from the PRO-CUT
system".
• Check the condition of the electrode. If the end
has a crater-like appearance, replace it along with
the nozzle. The maximum wear depth of the elec-
trode is approximately .062”. A green and erratic
arc will indicate definite electrode failure and the
electrode should be replaced immediately.
• Replace the nozzle when the orifice exit is eroded
away or oval shaped.
• After the problem is found, or if there is nothing
apparently wrong, reset the machine by turning the
power switch OFF and then ON again. (It is possi-
ble for electrical noise to trip the safety circuit on
rare occasions. This should not be a regular occur-
rence.)
• If the machine does not reset or continues to trip,
consult the Troubleshooting Section.
• Use the proper cutting procedures referred to in
Procedure Recommendations.
PILOT ARC DISCUSSION
The PRO-CUT has a smooth, continuous pilot arc.
The pilot arc is only a means of transferring the arc to
the workpiece for cutting. Repeated pilot arc starts, in
rapid succession, is not recommended as these starts
will generally reduce consumable life. Occasionally,
the pilot arc may sputter or start intermittently. This is
aggravated when the consumables are worn or the air
pressure is too high. Always keep in mind that the
pilot arc is designed to transfer the arc to the work-
piece and not for numerous starts without cutting.
When the pilot arc is started, a slight impulse will be
felt in the torch handle. This occurrence is normal and
is the mechanism which starts the plasma arc. This
impulse can also be used to help troubleshoot a "no
start" condition.
PRO-CUT 20
ELECTRIC SHOCK CAN KILL.
• Turn off machine at the disconnect
switch on the front of the machine
before tightening, cleaning or replacing
consumables.
----------------------------------------------------------------------------
WARNING