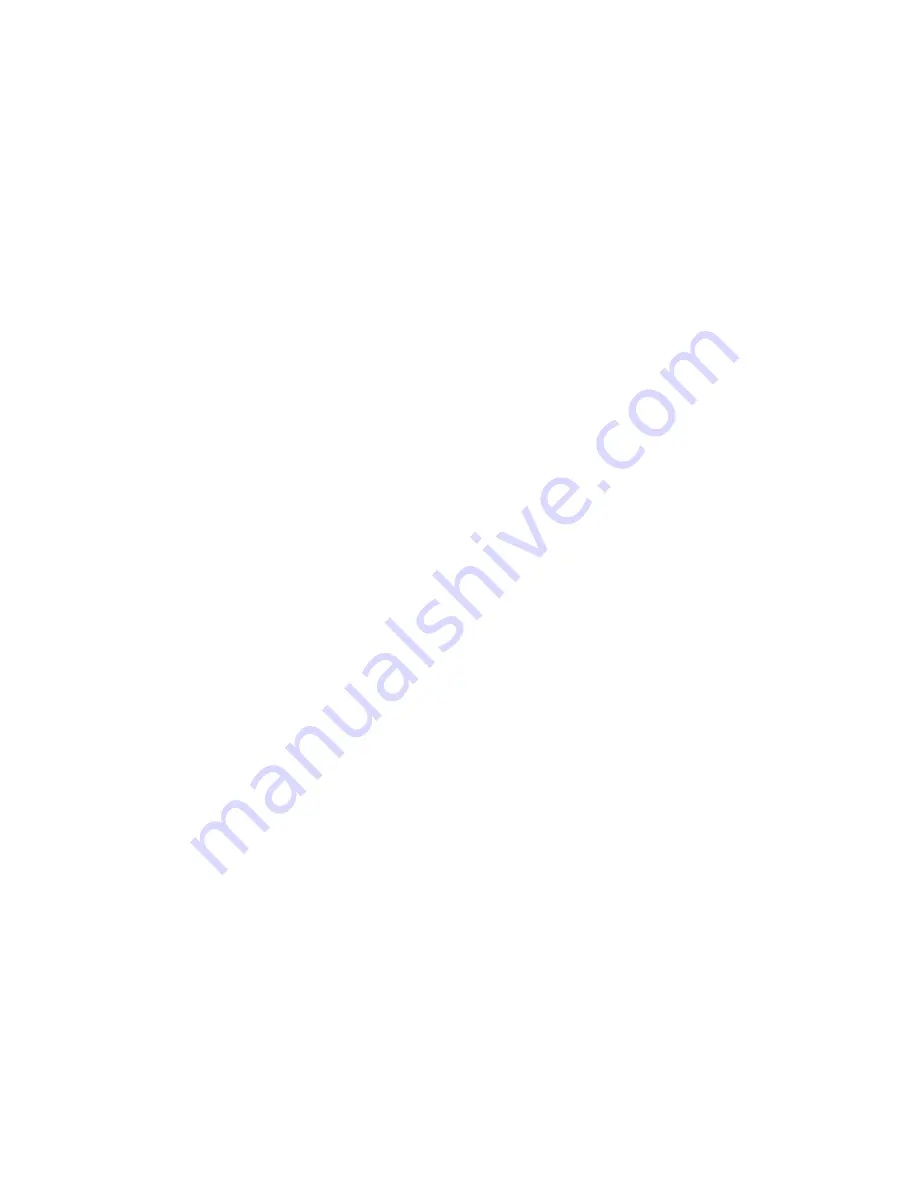
Expanded Metal:
Output set near mid-range.
• Cut it as you would light gauge sheet metal.
• Expanded metal is pilot arc intensive. After
about 30 seconds of cutting, the pilot arc will
change from a bright continuous arc to a discon-
tinuous one which will sputter slightly. It will stay
in this mode as long as metal has been cut in
the previous 5 seconds. If metal is not cut in the
previous 5 seconds, the arc will shut off and the
machine will go into postflow.
•If the trigger is continuously pressed and
released to obtain the bright pilot arc for long
periods of time, the machine will go into pilot arc
duty cycle limit. This is a 20 seconds out of 80
seconds pilot duty cycle. The pilot arc is dis-
abled in the limit period. Pilot arc duty cycle
limit is indicated by alternately flashing “OUT-
PUT ON” and “MALFUNCTION” LED’s.
• Placing a thin piece of scrap sheet metal above
the area to be cut and cutting through both can
make the job easier.
• Do not allow cable or body to contact hot sur-
face.
Material Thickness above .75” (19mm):
Output set above mid-range.
• The best quality and consumable life will be
obtained by holding the torch nozzle off the sur-
face about 1/4” (6.4mm). Do not touch the noz-
zle to the work or carry a long arc.
• Use either S19972 standoff guide or S19973
and S19974 contact attachments to protect the
torch. The only reason not to use these are in
special tight corners. Always hold at least a 1/4”
(6.4mm) standoff in those situations.
• Set the current to the minimum necessary to
make the cut.
• Pierce the plate by slowly lowering the torch
onto it at an angle of about 30° to blow the
dross away from the torch tip and slowly rotate
the torch to a vertical position as the arc
becomes deeper.
• Where possible, start the cut from the edge of
the workpiece.
• Keep moving!
A steady speed is necessary.
Do not pause.
• Do not allow the torch cable or body to contact
hot surfaces.
• For thickness between .75” (19mm) and 1.00”
(25.4mm), use an S19961-4 nozzle (1.9mm dia.
orifice). The S19972 standoff guide should be in
the lowest position for maximum standoff.
• For thickness above 1.00” (25.4mm), use an
S19961-4 nozzle (1.9mm dia. orifice). The
S19972 standoff guide should be in the lowest
position for maximum standoff.
Gouging:
Output set to maximum.
• Use a gouging nozzle S19961-5. The pilot arc
may sputter while gouging, but this is normal.
• Use the S19975 gouging attachment in the low-
est position for maximum standoff.
• Bring the torch slowly towards the work at about
a 30° angle as if piercing the plate. Blow the
molten metal away from the torch.
• Do not touch the nozzle to the work.
• To obtain deeper penetration when gouging,
lower the flowing air pressure to 50 psi. To
obtain shallower penetration, raise the flowing
air pressure to 70 psi.
• This process will blow a lot of molten metal and
dross.
BE CAREFUL!
Blow the dross away
from the torch, away from the operator and
away from flammable objects.
• Do not allow the torch cable or body to contact
hot surfaces.
• Performance is similar to air carbon arc gouging
with a 1/8” (3.2mm) carbon electrode.
– 13 –