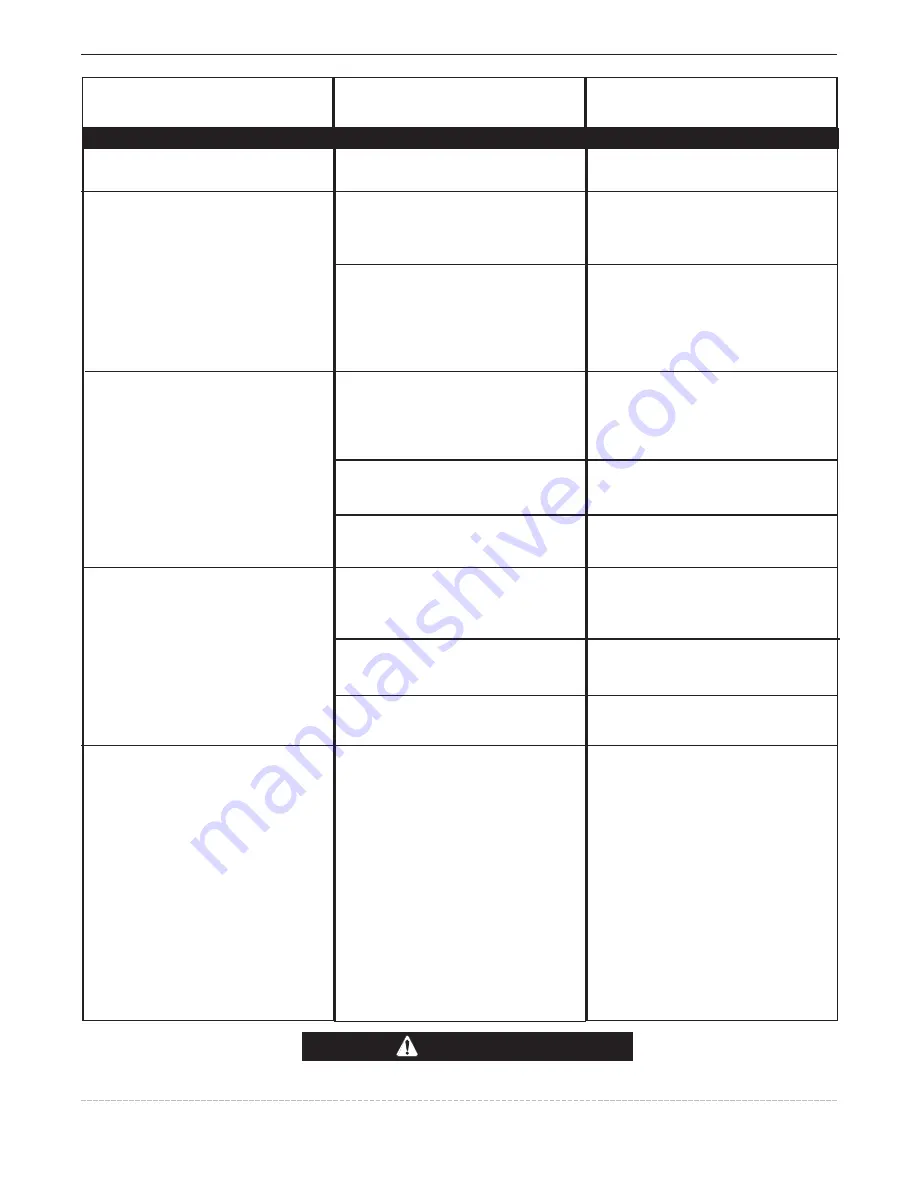
Observe all Safety Guidelines detailed throughout this manual
If for any reason you do not understand the test procedures or are unable to perform the tests/repairs safely, contact your
Local Lincoln
Authorized Field Service Facility
for technical troubleshooting assistance before you proceed.
CAUTION
PROBLEMS
(SYMPTOMS)
POSSIBLE
CAUSE
RECOMMENDED
COURSE OF ACTION
Wire burns back to tip at the end of the
weld.
Machine output shuts down during a weld.
Machine won’t produce full output.
Excessively long and erratic arc.
1. Burnback Time
1. Secondary current limit has been exceed-
ed, and the machine shuts down to pro-
tect itself.
2. System Fault
1. Input voltage may be too low, limiting
output capability of the power source.
2. The input may be single phase.
3. Machine calibration.
1. Wire feed problem.
2. Loss of, or improper Shielding Gas
3. Machine calibration.
1. Reduce burnback time and/or work point.
1. Adjust procedure or reduce load to lower
current draw from the machine.
2. A non-recoverable fault will interrupt
welding. This condition will also result in
a status light blinking. See the Status
Light section for more information.
1. Make certain that the input voltage is
proper, according to the Rating Plate
located on the rear of the machine.
2. Verify all 3 phases are present.
3. Calibrate secondary current and voltage.
1. Check for feeding problems. Make sure
proper gear ratio has been selected.
2. Verify gas flow and type are correct
3. Calibrate secondary current and voltage.
Weld and Arc Quality Problems (Continued)
E-7
TROUBLESHOOTING
POWER WAVE
®
R500
Summary of Contents for POWER WAVE R500
Page 36: ...F 2 DIAGRAMS POWER WAVE R500 L16215 A 01 13 94 22 45 27 43 6 00 18 35 24 76...
Page 37: ...F 3 NOTES...
Page 38: ...F 4 NOTES...
Page 39: ...F 5 NOTES...