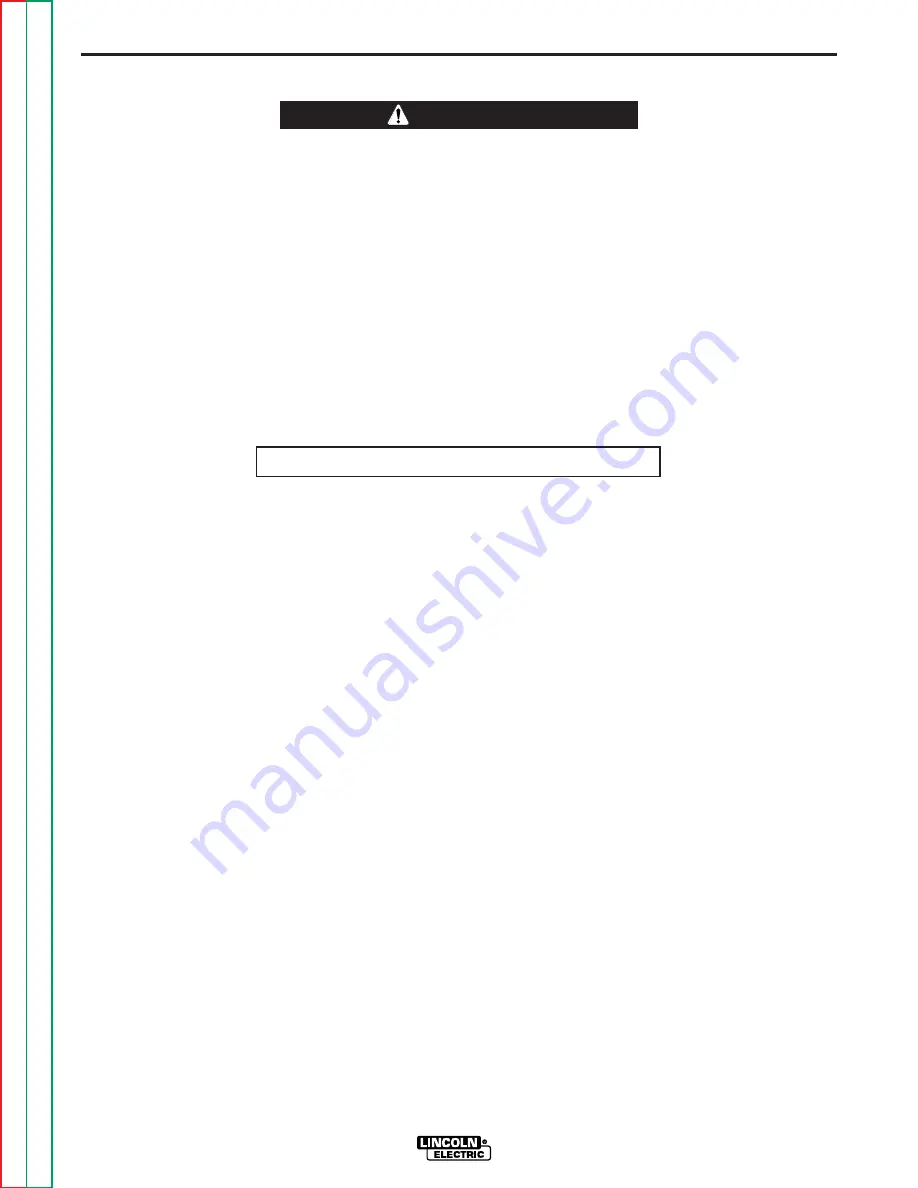
F-43
TROUBLESHOOTING AND REPAIR
F-43
POWER BOARD TEST
Service and repair should only be performed by Lincoln Electric factory trained
personnel. Unauthorized repairs performed on this equipment may result in dan-
ger to the technician or machine operator and will invalidate your factory warran-
ty. For your safety and to avoid electrical shock, please observe all safety notes
and precautions detailed throughout this manual.
If for any reason you do not understand the test procedures or are unable to per-
form the test/repairs safely, contact the Lincoln Electric service department for
technical troubleshooting assistance before you proceed. Call 216-383-2531 or
1-800-833-9353(WELD).
------------------------------------------------------------------------------------------------
TEST DESCRIPTION
This test will help determine if the power board is receiving the correct voltages and
also if the power board is regulating and producing the correct DC voltages.
This procedure takes approximately 20 minutes to perform.
MATERIALS NEEDED
3/8 in. nutdriver
Volt-Ohmmeter
Wiring diagram
POWER WAVE 455/POWER FEED 10
WARNING
Return to Section TOC
Return to Section TOC
Return to Section TOC
Return to Section TOC
Return to Master TOC
Return to Master TOC
Return to Master TOC
Return to Master TOC