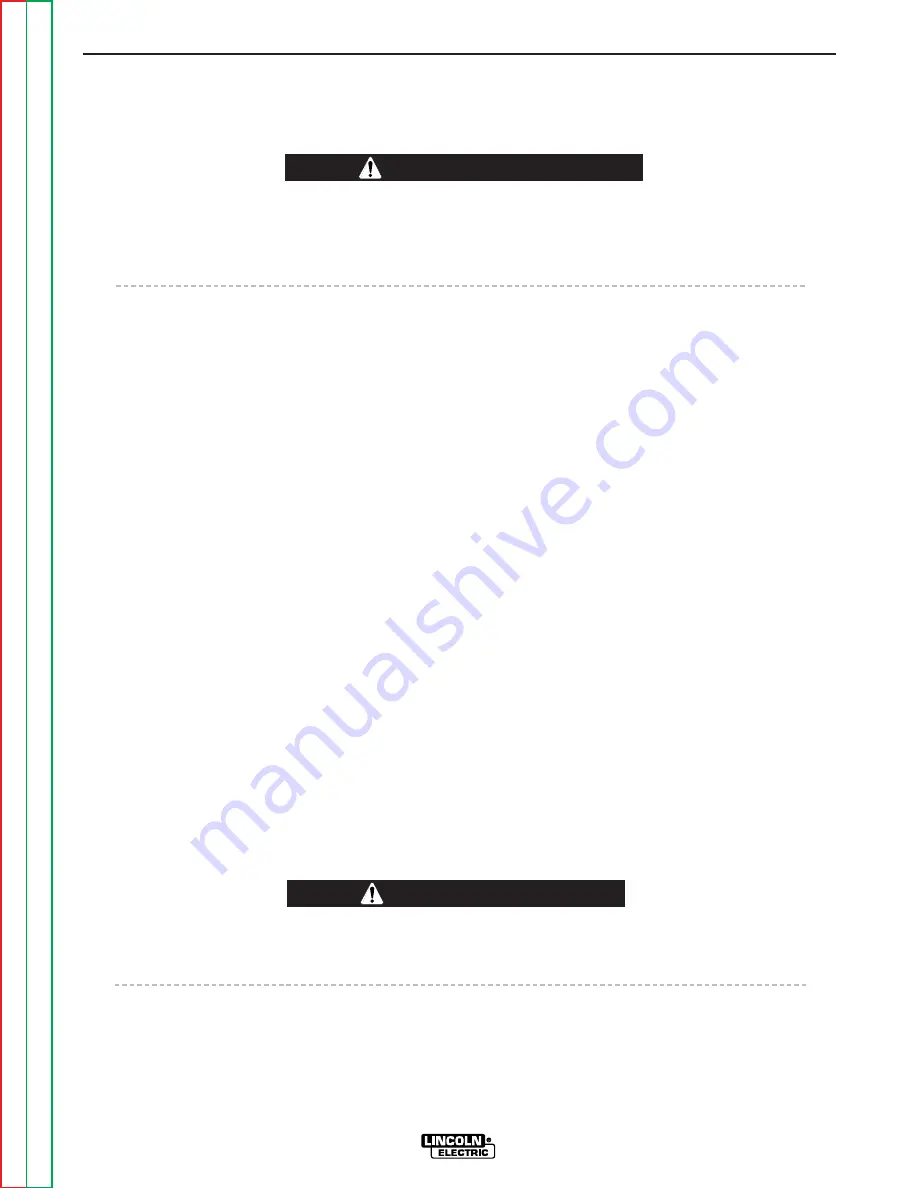
Retur
n to Section TOC
Retur
n to Section TOC
Retur
n to Section TOC
Retur
n to Section TOC
Retur
n to Master TOC
Retur
n to Master TOC
Retur
n to Master TOC
Retur
n to Master TOC
HOW TO USE TROUBLESHOOTING GUIDE
Service and repair should be performed by only Lincoln Electric Factory Trained Personnel.
Unauthorized repairs performed on this equipment may result in danger to the technician and machine
operator and will invalidate your factory warranty. For your safety and to avoid Electrical Shock, please
observe all safety notes and precautions detailed throughout this manual.
TROUBLESHOOTING & REPAIR
F-2
F-2
POWER MIG 300
This Troubleshooting Guide is provided to help
you locate and repair possible machine malfunc-
tions. Simply follow the three-step procedure list-
ed below.
Step 1. LOCATE PROBLEM (SYMPTOM).
Look
under the column labeled “PROBLEM” (SYMP-
TOMS). This column describes possible symp-
toms that the machine may exhibit. Find the list-
ing that best describes the symptom that the
machine is exhibiting. Symptoms are grouped
into four main categories: Output Problems,
Function Problems, Wire Feeding, and Welding
Problems.
Step 2. PERFORM EXTERNAL TESTS.
The
second column, labeled “POSSIBLE AREAS OF
MISADJUSTMENT(S)”, lists the obvious external
possibilities that may contribute to the machine
symptom. Perform these tests/checks in the
order listed. In general, these tests can be con-
ducted without removing the case cover.
Step 3. PERFORM COMPONENT TESTS.
The
last column, labeled “Recommended Course of
Action” lists the most likely components that may
have failed in your machine. It also specifies the
appropriate test procedure to verify that the sub-
ject component is either good or bad. If there are
a number of possible components, check the
components in the order listed to eliminate one
possibility at a time until you locate the cause of
your problem.
All of the referenced test procedures referred to in
the Troubleshooting Guide are described in detail
at the end of this section. Refer to the
Troubleshooting and Repair Table of Contents
to locate each specific Test Procedure. All of the
referred to test points, components, terminal
strips, etc., can be found on the referenced elec-
trical wiring diagrams and schematics. Refer to
the
Machine Schematic
and
Electrical
Diagrams
Section Table of Contents to locate the
appropriate diagram.
WARNING
If for any reason you do not understand the test procedures or are unable to perform the test/repairs
safely, contact the Lincoln Electric Service Department for electrical troubleshooting assistance before
you proceed. Call 1-800-833-9353.
CAUTION
Summary of Contents for Power MIG 300
Page 126: ...POWER MIG 300 SVM160 B...