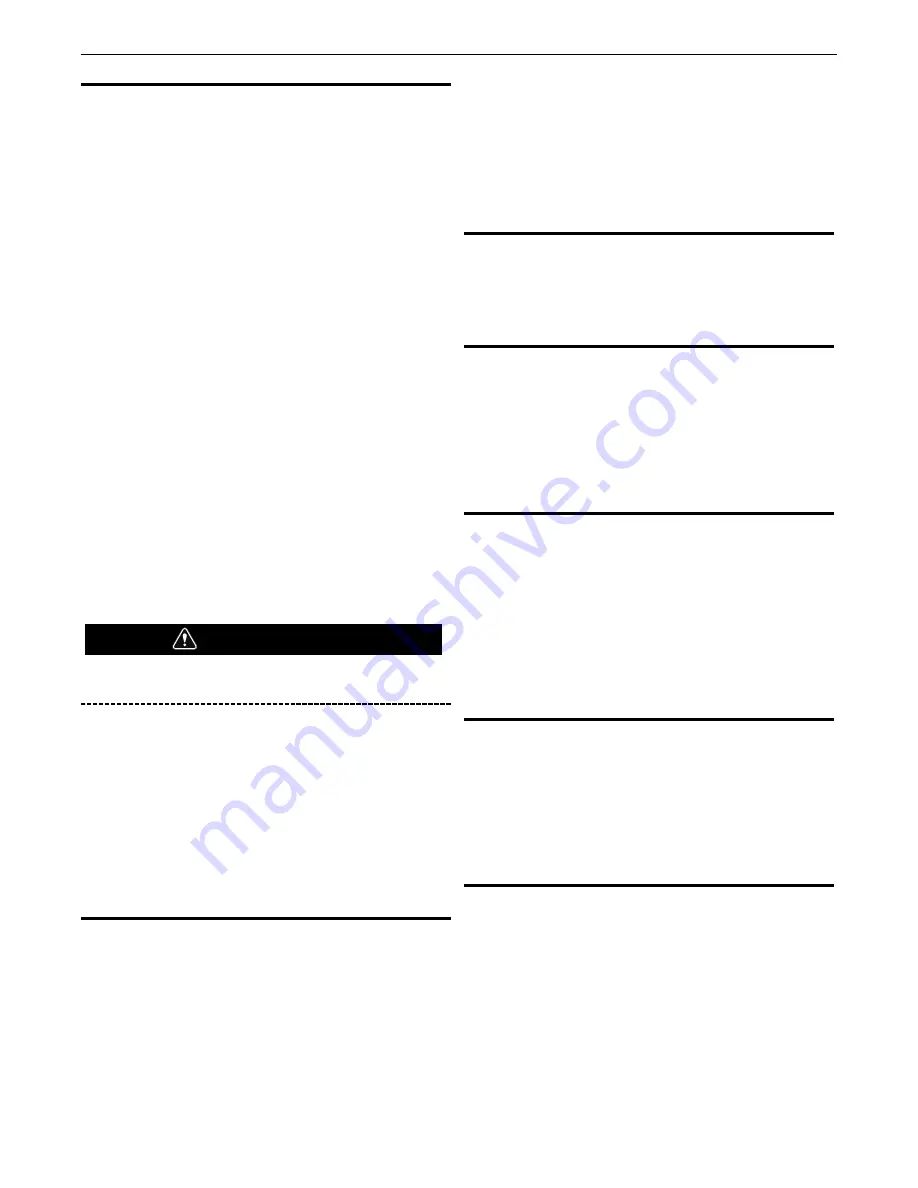
B-9
OPERATION
POWER MIG
®
260
MAKING A WELD
1. Check that the electrode polarity is correct for the process
being used, then turn the power switch ON.
2. Set desired arc voltage and wire speed for the particular
electrode wire, material type and thickness, and gas (for
GMAW) being used.
3. Select the desired procedure as described in "Description of
Controls” Section.
4. Press the trigger to feed the wire electrode through the gun
and cable and then cut the electrode within approximately
3/8" (10 mm) of the end of the contact tip [3/4" (20 mm)
Outershield
®
].
NOTE: If set for slow run-in when the trigger is pulled, the wire
feeder feeds wire at low speed regardless of the set wire feed
speed until the welding arc starts or 1 second has elapsed.
This feature enhances starting and makes it easier to set the
stickout. The 1 second limit permits high speed loading of the
gun and cable. To change run-in mode, see "Run-In Mode" in
Description of Controls Section.
5. If welding gas is to be used, turn on the gas supply and set
the required flow rate (typically 25-35 CFH; 12-16 liters/min).
6. When using Innershield electrode, the gas nozzle may be
removed from the insulation on the end of the gun and
replaced with the gasless nozzle. This will give improved
visibility and eliminate the possibility of the gas nozzle
overheating.
7. Connect work cable to metal to be welded. Work clamp must
make good electrical contact to the work. The work must also
be grounded as stated in "Arc Welding Safety Precautions".
When using an open arc process, it is necessary to use
correct eye, head, and body protection.
8. Position electrode over joint. End of electrode may be lightly
touching the work.
9. Lower welding helmet, close gun trigger, and begin welding.
Hold the gun so the contact tip to work distance is about 3/8"
(10 mm) [3/4" (20 mm) for Outershield].
10. To stop welding, release the gun trigger and then pull the gun
away from the work after the arc goes out.
11. When no more welding is to be done, close valve on gas
cylinder (if used), momentarily operate gun trigger to release
gas pressure, and turn off POWER MIG
®
260.
AVOIDING WIRE FEEDING PROBLEMS
Wire feeding problems can be avoided by observing the following
gun handling procedures:
• Do not kink or pull cable around sharp corners.
• Keep the gun cable as straight as possible when welding or
loading electrode through cable.
• Do not allow dolly wheels or trucks to run over cables.
• Keep cable clean by following maintenance instructions.
• Use only clean, rust-free electrode. The Lincoln electrodes
have proper surface lubrication.
• Replace contact tip when the arc starts to become unstable or
the contact tip end is fused or deformed.
• Keep wire reel spindle brake tension to minimum required to
prevent excess reel over-travel which may cause wire "loop-
offs" from coil.
• Use proper drive rolls and wire drive idle roll pressure for wire
size and type being used.
FAN CONTROL
The fan is designed to come on automatically when a weld arc is
established. The fan will also stay on when the machine’s welding
and feeding are disabled during thermostatic over temperature
protection. (See Welding Thermal Overload Protection)
INPUT LINE VOLTAGE PROTECTION
High Line Voltage — If the line voltage exceeds 110% of rated
input voltage, the output will be reduced to the lower level to
protect voltage rating of the capacitor bank.
Low Line Voltage — You may not be able to get maximum output
from the machine if the line voltage is less than rated input. The
unit will continue to weld, but the output may be less than what is
set.
WIRE FEED OVERLOAD PROTECTION
The POWER MIG
®
260 has solid state overload protection of the
wire drive motor. If the motor becomes overloaded, the protection
circuitry turns off the wire feed speed weld output and gas
solenoid. Check for proper size tip, liner, and drive rolls, for any
obstructions or bends in the gun cable, and any other factors that
would impede the wire feeding.
To resume welding, simply pull the trigger. There is no circuit
breaker to reset, as the protection is done with reliable solid state
electronics.
WELDING THERMAL OVERLOAD PROTECTION
The POWER MIG
®
260 has built-in protective thermostats that
respond to excessive temperature. They open the wire feed and
welder output circuits if the machine exceeds the maximum safe
operating temperature because of a frequent overload, or high
ambient temperature plus overload. The thermostats automatically
reset when the temperature reaches a safe operating level and
welding and feeding are allowed again, when gun is retriggered.
OVERCURRENT PROTECTION
The machine will automatically reduce the output if the load on
the machine exceeds 300 to 320 amperes. This protects the
welding machine from excessive short circuit currents and from
exceeding their temperature rating before the thermostats can
react.
WARNING