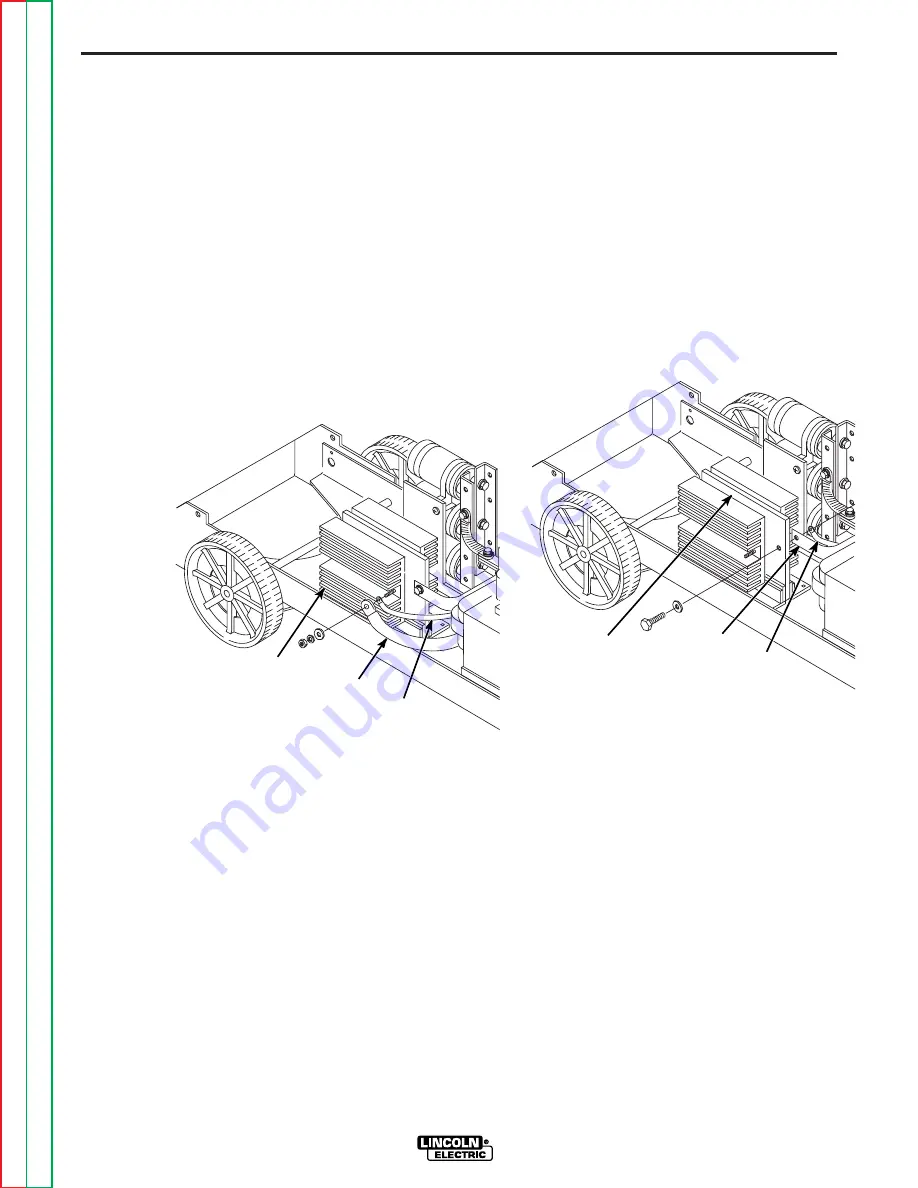
F-46
TROUBLESHOOTING AND REPAIR
F-46
POWER MIG 255C
3. Disconnect lead #204 and heavy alu-
minum choke lead from the middle heat
sink with a 1/2 in. socket wrench and
1/2 in. open end wrench. See Figure
F.14.
4. Remove the diode lead from the nega-
tive capacitor band buss bar on the
right side of the machine using a 1/2 in.
socket and 3/8 in. open end wrench.
FIGURE F.14 — MIDDLE HEAT SINK
LEAD DISCONNECTION.
PROCEDURE
1. Remove the case side panels using a
3/8 in. nutdriver.
2. Disconnect lead #208S and trans-
former lead X1 from the heat sink on
the left side of the machine using a 1/2
in. socket wrench. See Figure F.13.
a. Thin lead is always on the outboard
side of the connection.
FIGURE F.13 — LEFT HEAT SINK
LEAD DISCONNECTION.
SCR OUTPUT RECTIFIER REMOVAL AND REPLACEMENT (continued)
LEAD X1
LEAD
#208S
LEFT
HEAT SINK
HEAVY
LEAD
LEAD
#204S
MIDDLE
HEAT SINK
Retur
n to Section TOC
Retur
n to Section TOC
Retur
n to Section TOC
Retur
n to Section TOC
Retur
n to Master TOC
Retur
n to Master TOC
Retur
n to Master TOC
Retur
n to Master TOC