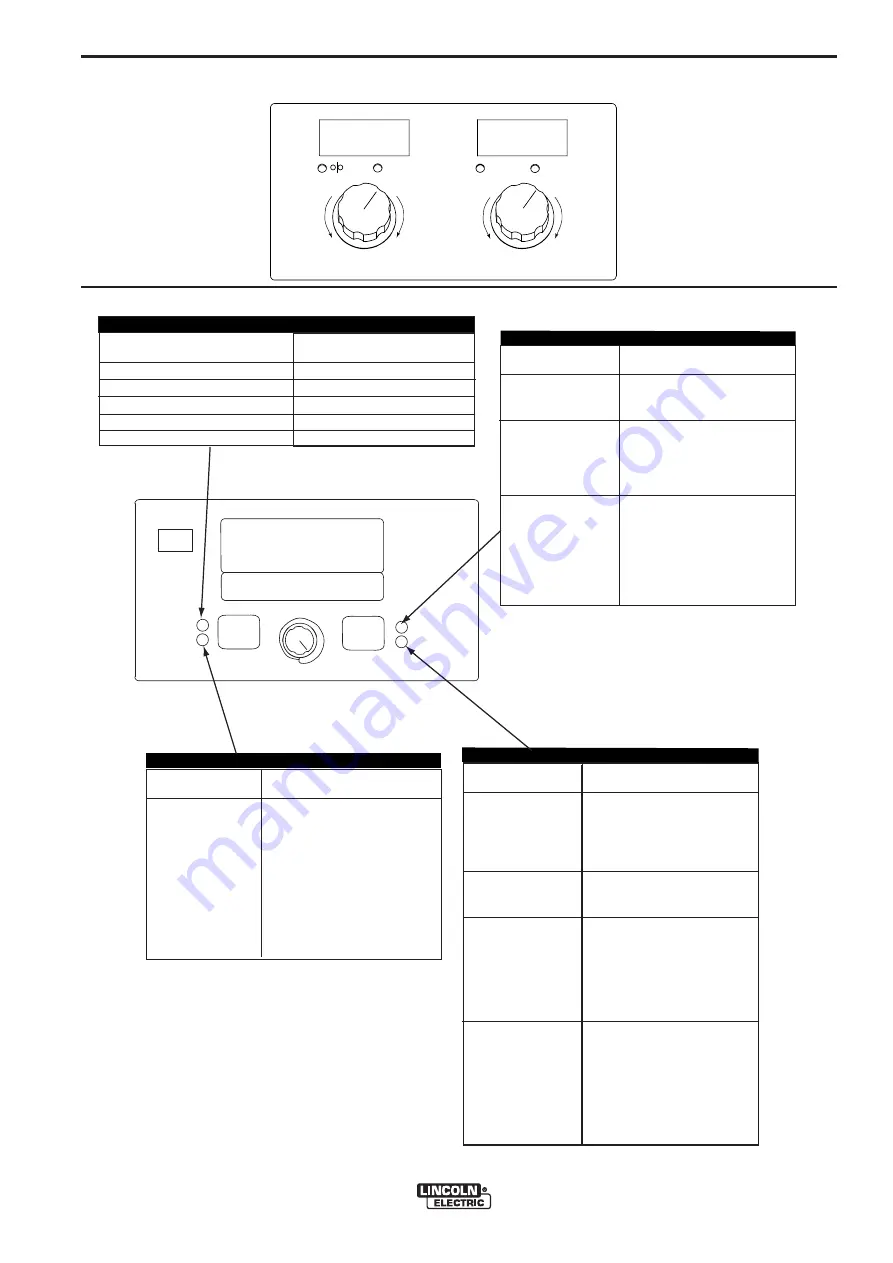
B-15
OPERATION
B-15
POWER FEED™ 25M
220
1.06
WFS AMPS
VOLTS TRIM
Less
Deposition
Shorter
Arc
Longer
Arc
More
Deposition
ARC
FOCUS
-10.0 (SOFT to
10.0 (STIFF)
DESCRIPTION
Arc Focus adjusts the arc from
a wide, soft arc good for out of
position work to a narrow, stiff
arc preferred for faster travel
speeds. The pulse frequency is
lower with a soft arc and higher
with a stiff arc.
PREFLOW TIME
0 - 25.0 seconds
RUN-IN WFS:
Off, 30 to150 in/min.
Start Procedure
DESCRIPTION
Adjusts the time that shielding
gas flows after the trigger is
pulled and prior to feeding wire.
Run-in sets the wire feed
speed from the time the trigger
is pulled until an arc is estab-
lished.
The Start Procedure controls
the WFS, Trim at a specified
time at the beginning of the
weld. During the start time, the
machine will ramp up or down
from the Start Procedure to the
preset Welding Procedure.
EFFECT / RANGE
Postflow Time:
0 to 25.0 seconds
Burnback: 0 to .25
Seconds
Crater Procedure
FUNCTION
Adjusts the time that shielding
gas flows after the welding out-
put turns off.
The burnback time is the
amount of time that the weld
output continues after the wire
stops feeding. It prevents the
wire from sticking in the puddle
and prepares the end of the
wire for the next arc start.
Crater Procedure controls the
WFS and Trim for a specified
time at the end of the weld
after the trigger is released.
During the Crater time, the
machine will ramp up or down
from the Weld Procedure to
the Crater Procedure.
ELECTRODE AND
Steel(Crisp)
Steel(Soft)
Stainless
Stainless
Stainless
GAS
2
CO
2
CO
2
Ar(Mix)
Ar(Mix)
Ar/He/CO
Ar/
Ar/
WIRE SIZE
0.030 0.035 0.045 0.052
---
14 19 28
95 12 22 201
66 36 46 ---
62 32 42 ---
--- 34 44 ---
START OPTIONS
END OPTIONS
WELD MODE
ARC CONTROL
STEEL
.035"
SET
SETUP
IR PORT
Pulse Crisp ArMix
WAVEFORM CONTROL TECHNOLOGY
WELD MODE
ARC CONTROL
12
START OPTIONS
END OPTIONS
Spot Timer
0 to 120.0 Seconds
Adjust the time welding will
continue even if the trigger
is still pulled. This option
has no effect in 4-Step
Trigger Mode.
MSP4 OPERATION
STEEL AND STAINLESS SYNERGIC GMAW-P (PULSED MIG) WELDING
All manuals and user guides at all-guides.com
all-guides.com