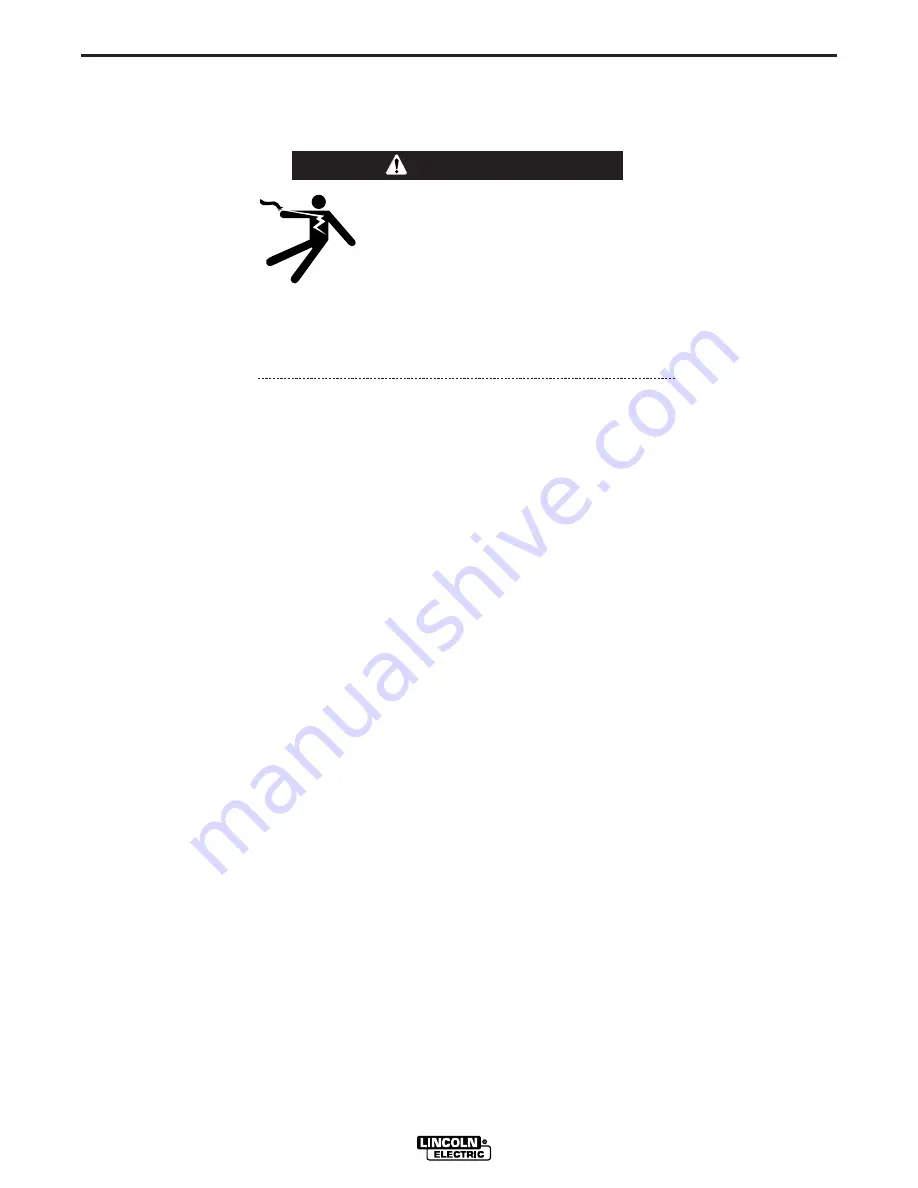
MAINTENANCE
SAFETY PRECAUTIONS
ELECTRIC SHOCK can kill.
• Disconnect input power by removing
plug from receptacle before working
inside machine. Use only grounded
receptacle. Do not touch electrically
“hot” parts inside machine
• Have qualified personnel do the mainte-
nance and trouble shooting work.
ITEMS REQUIRING
NO MAINTENANCE
• Drive Motor and Gearbox – Lifetime lubrication
• Wire Reel Spindle – Do NOT lubricate shaft
ROUTINE AND PERIODIC
MAINTENANCE
BEFORE EACH USE
• Check over machine and accessories for any obvious condi-
tion that may prevent safe performance or operation. Repair
or replace items as necessary to correct any abnormal con-
dition.
AFTER 5 MINUTES OF WELDING
or when spatter accumulates in the gas nozzle:
• Clean the contact tip and gas nozzle to avoid bridging
between the nozzle and contact tip. Bridging results in a
shorted nozzle, poor welds and overheated gun. Hint: Anti-
stick spray or gel available from a welding supplier may
reduce buildup and aid in spatter removal.
D-1
MAINTENANCE
D-1
MIG PAK HD
WARNING