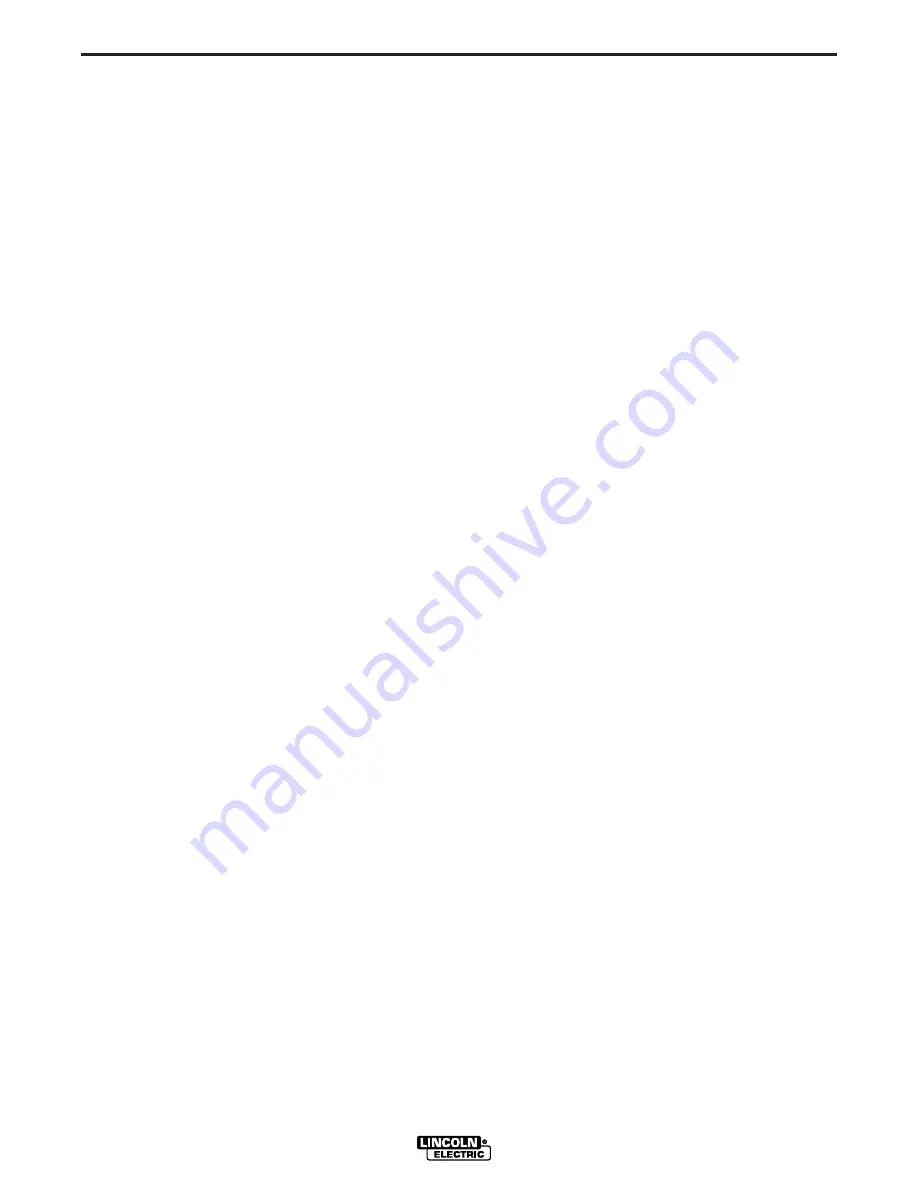
C-3
ACCESSORIES
C-3
K320 FLUX TANK
Either turn off the incoming air line or remove the quick
disconnect if one has been installed. Slightly loosen
the tank cap and let the air in the tank escape in the
holes in the side of the cap. After pressure has been
released, remove the cap from the tank. Using the
funnel provided, put 100 pounds of flux in the tank. It is
very important that only new or properly reclaimed flux
be put in the tank. Coarse particles and/or magnetic
particles will stop the flux feeding process. New Lincoln
flux is properly screened at the factory. All reclaimed
flux must be separately screened through a vibrating
screen with 0.065 in. to 0.075 in. openings and be put
through a magnetic separator. The K310 vibrated
screen and K58 magnetic separator are available for
this purpose. The screen in the funnel supplied with the
tank has much larger openings and its only purpose is
to keep paper and slag out of the tank.
There will always be a small amount of air and possible
drops of water coming out of the end of the tube coiled
under the tank. This is an automatic disposal system in
case the plant air has water and dirt in it.
POWER INPUT CABLES
A variety of power input cable assemblies are avail-
able for various current ratings and power source con-
nection types. All provide a polarized control cable
plug and a lugged electrode cable for connection to
the wire feeder.
K1819-[ ] CONTROL CABLES
These control cables connect the wire feeder to the
power source.The wire feeder end is an 8 pin anphe-
nol and the power source end is a 14 pin amphenol.
The control cable supplies 42VAC from the welding
power source to the feeder. It also carries a lead for
the work voltage and sends signals for the gun trigger
and remote voltage potentiometer. See connection
diagram of wire feeder to power source in the
“
Installation Section
”
.
K1817-[ ] CONTROL CABLE EXTENSIONS
The control cable extensions are used to lengthen the
control cable. The extensions have a 14 pin amphenol
on one end that connects to the K1819-[ ] cable and
the other end has a 14 pin amphenol that connects to
the welding power source. Do not exceed more than
100 Ft. (31m) of total control length. See connec-
tion diagram of wire feeder to power source in the
“
Installation Section
”
.
WELDING GUNS
Welding guns can be broken down into groups,
according to the type of welding that is to be
accomplished. Select the appropriate welding gun from
the following weld-type groups.
INNERSHIELD GUNS
K122. This submerged arc gun and its cable assem-
blies are rated 500 amps, 60% duty cycle.
K115. This Innershield gun and its cable assemblies
are rated at 450 amps, 60% duty cycle. Maximum wire
size for LN-742 models is 5/64 in. (2.0 mm).
K126. This Innershield gun and its cable assemblies
are rated at 350 amps, 60% duty cycle. Maximum wire
size for LN-742 models is 5/64 in. (2.0 mm).
NOTE: The K115 and K126 are not recommended for
LN-742H models.
NOTE: Linconditioner
TM
guns are recommended for
locations where smoke accumulation is a problem and
conventional exhaust systems are ineffective. The
available smoke removal type Innershield guns and
vacuum units can be used in these locations.
Instructions are shipped with the equipment.
LN-742 & LN-742H
Summary of Contents for LN-742
Page 42: ...NOTES LN 742 LN 742H ...
Page 43: ...NOTES LN 742 LN 742H ...
Page 44: ...F 4 NOTES LN 742 LN 742H F 4 ...
Page 45: ...F 5 NOTES LN 742 LN 742H F 5 ...