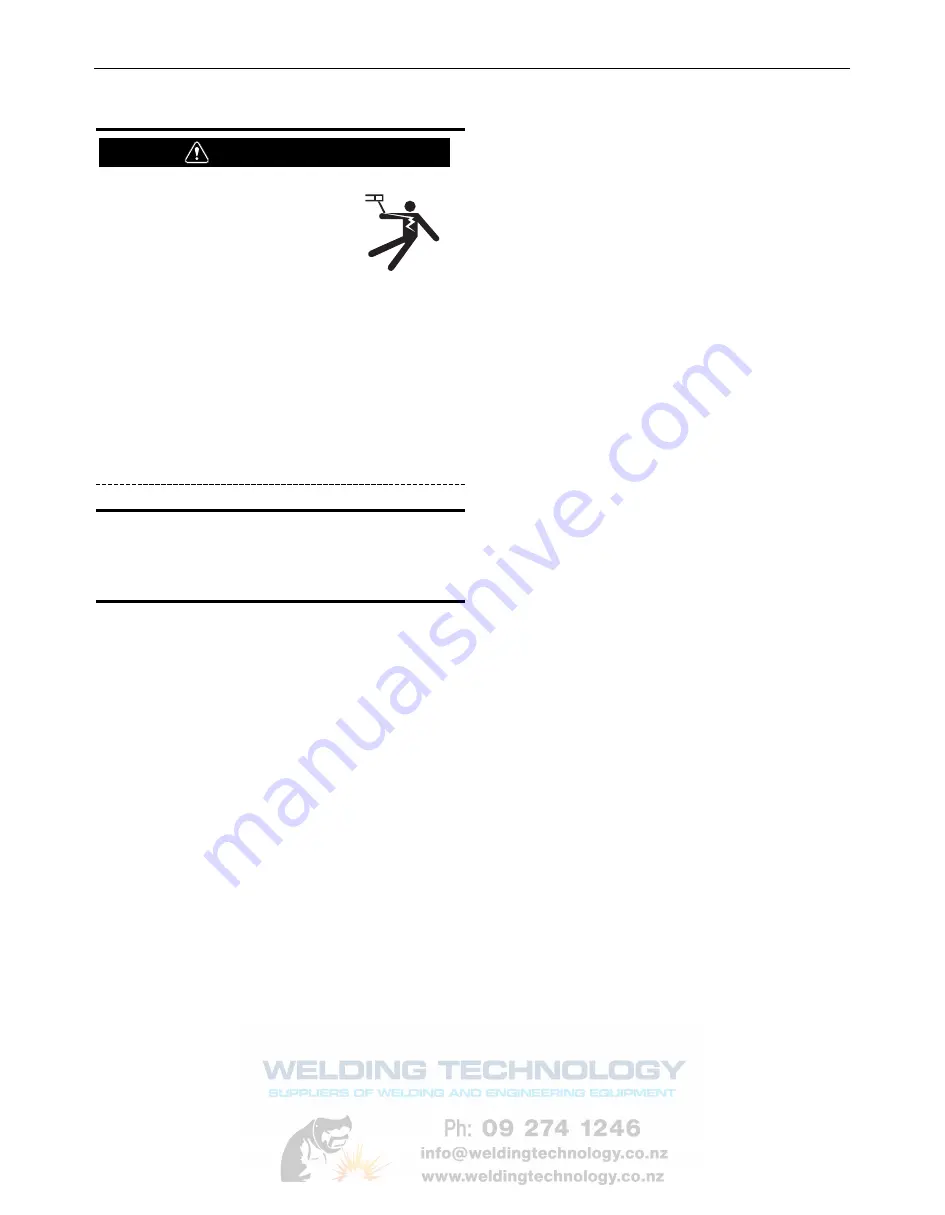
D-1
MAINTENANCE
ELECTRIC SHOCK CAN KILL.
•
Turn the input power OFF at the
welding power source before
installation or changing drive rolls
and/or guides.
•
Do not touch electrically live parts.
•
When inching with the gun trigger, electrode and drive
mechanism are "hot" to work and ground and could
remain energized several seconds after the gun trigger
is released.
•
Do not operate with covers, panels or guards removed
or open.
•
Only qualified personnel should perform
maintenance work.
roUtine Maintenance
•
Check weld cables and gas hoses for cuts.
•
Clean and tighten all weld terminals.
perioDic Maintenance
•
Clean the drive rolls and inner wire guide and replace if worn.
•
Blow out or vacuum the inside of the feeder.
Flow Meter Validation
Tools required:
• Flow meter reference standard.
• Constant voltage DC welding power source (DC- 400, V-350,
CV-400 or equivalent).
To verify the flow meter accuracy:
1. Turn power OFF.
2. Connect the LN-25X™to the constant voltage DC welding power
source. The work lead of the LN-25X™must be connected to the
work terminal of the power source.
3. Connect a supply of CO2 to the wire feeder. Do not exceed the
maximum inlet pressure of the wire feeder.
4. Disconnect the shielding gas hose that connects to the gun
bushing.
5. Connect the shielding gas hose to flow meter reference standard.
6. Orient the LN-25X™in a vertical position.
7. Turn power ON.
8. Adjust the flow meter on the LN-25X™to 40 scfh while pressing
the GAS PURGE button.
9. Measure the gas flow with the calibrated flow meter while
pressing the GAS PURGE button.
10. The measured flow rate should be between 35 and 45 scfh. The
LN-25X™flow meter cannot be calibrated. If the flow meter
reads incorrectly, check for leaks or kinks in the gas hose.
Replace the flow meter if necessary.
WARNING
LN-25X™
MAINTENANCE