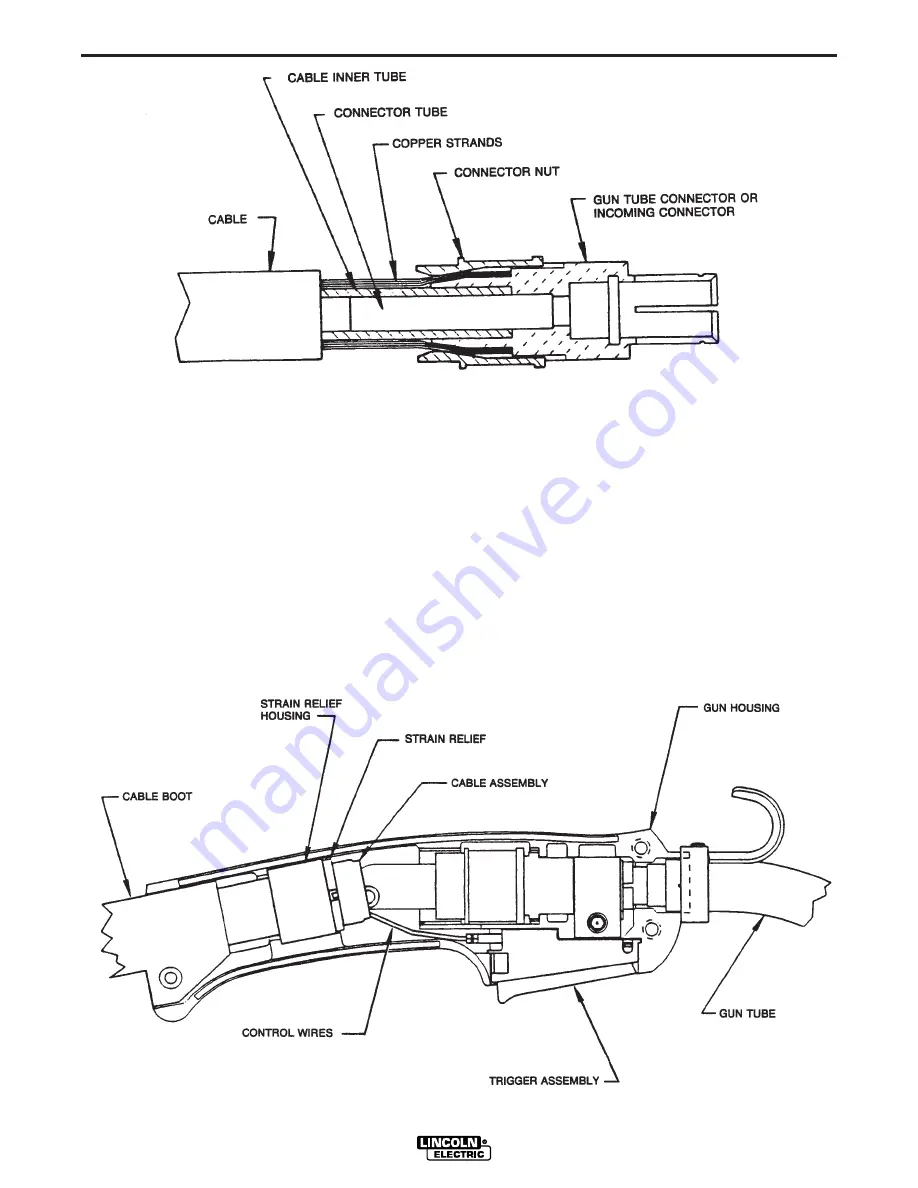
D-3
MAINTENANCE
D-3
strain relief are on the cable. Slip the connector nut
over the copper strands with the thread end out.
Orient gun tube connector so machined flat is on
the same side of the cable as the red and white
control leads. Assemble gun tube connector to
cable by forcing the steel tube of the connector into
the inside diameter of the cable inner tube until the
copper strands are butted against the gun tube
connector shoulder. Keeping the copper strands
against the shoulder, pull the connector nut over
the copper strands, engage the gun tube connector
threads, and tighten in place. Refer to Figure 3.
NOTE:
For best results, insert a .175”/.197” (4.5-
5.0 mm) diameter rod through the connec-
tor and into core of cable approximately
5.00” (127 mm) when pushing the connec-
tor tube into the cable core tube. To tighten,
hold the connector in place while turning
the nut. Then remove the rod from the core.
This procedure ensures the inner core does
not kink while assembling or tightening.
h. Pull the cut-off lead terminals off the trigger assem-
bly and connect the replacement control lead termi-
nals.
i. Position the cable boot and strain relief on the
MAGNUM 200FM
FIGURE 3
FIGURE 4
Summary of Contents for K498
Page 5: ...iv SAFETY iv Mar 93...
Page 19: ...NOTES MAGNUM 200FM...