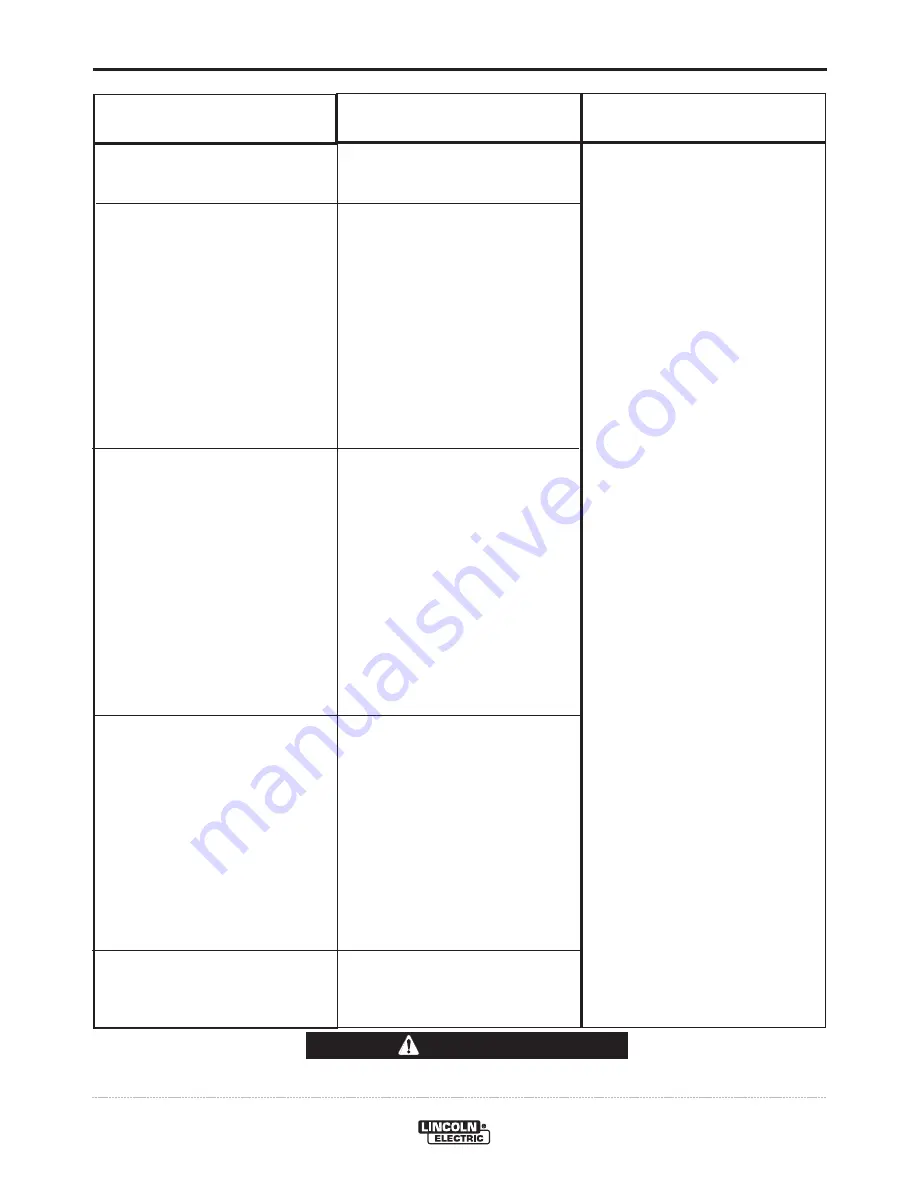
E-2
TROUBLESHOOTING
E-2
V350-PIPE
If for any reason you do not understand the test procedures or are unable to perform the tests/repairs safely, contact your
Local Lincoln Authorized Field Service Facility
for technical troubleshooting assistance before you proceed.
CAUTION
Observe all Safety Guidelines detailed throughout this manual
PROBLEMS
(SYMPTOMS)
POSSIBLE
CAUSE
RECOMMENDED
COURSE OF ACTION
Major physical or electrical damage
is evident when the sheet metal
covers are removed.
Input fuses keep blowing, or input
breaker keeps tripping
Machine will not power up (No
lights)
Machine won’t weld, can’t get any
output.
1. Contact your local authorized
Lincoln Electric Field Service facil-
ity for technical assistance.
1. Make certain that the fuses or
breakers are properly sized. See
installation section of the manual
for recommended fuse and break-
er sizes.
2. Welding procedure is drawing too
much output current, or duty cycle
is too high. Reduce output current,
duty cycle or both.
3. There is internal damage to the
power source. Contact an autho-
rized Lincoln Electric Service facil-
ity.
1. Make certain that the power
switch is in the "ON" position.
2. The circuit breaker in the recon-
nect area may have opened.
Reset. Check input voltage sec-
tion below.
3. Input voltage selection made
improperly. Power down, check
input voltage reconnect according
to diagram on reconnect cover.
4. The 6 amp breaker may have
opened. Check for overload on
42VAC or 24VAC supply from the
14 pin MS-style connector.
1. If the displays show an Err ###
see the fault section for corrective
action.
2. If the displays are not lit refer to
machine will not power up section.
3. If the thermal symbol is lit refer to
the thermal section.
4. If the output terminals are in
remote control switch to "ON" and
check for output voltage. If output
voltage is now present check for
correct remote control connection
and operation.
1.If all recommended possible areas
of misadjustment have been
checked and the problem persists,
Contact your local Lincoln
Authorized Field Service
Facility.