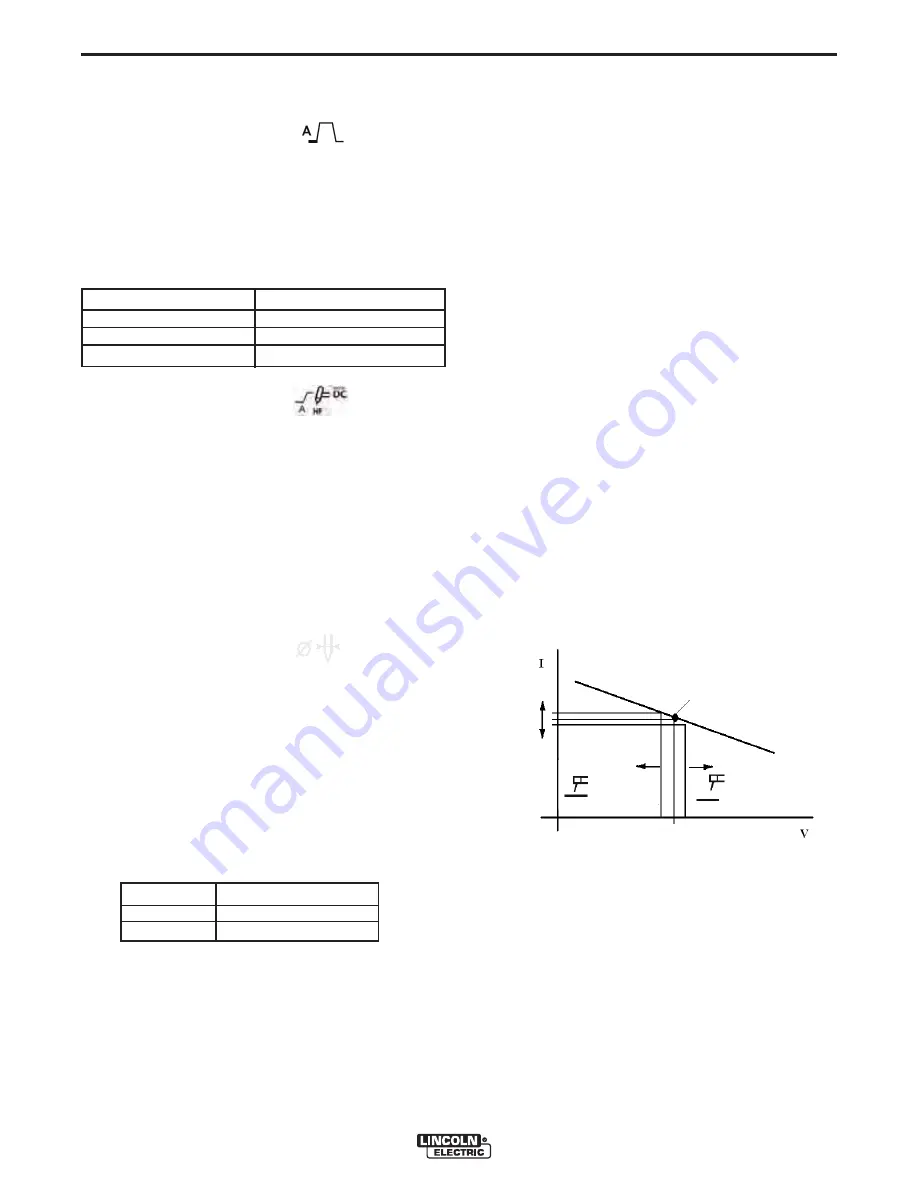
B-11
OPERATION
B-11
TIPS FOR IMPROVED TIG STARTING
1. Start Current:
For the best AC or DC TIG starting characteristics it
may be necessary to adjust the start current on the
front panel depending on the tungsten size. In gener-
al, larger tungsten requires more energy to establish
an arc than smaller tungsten. As an initial guideline,
set the start current according to the following recom-
mendations:
Tungsten Size (in.)
Start Current (Amps)
0.020, 0.040 1/16th
6-10 Amps
3/32 th
10-12 Amps
1/8th 12-15
Amps
2. DC Strike Current:
Aside from start current, DC strike current can also be
adjusted from the set-up menu to get a hotter or softer
start when DC TIG welding. Strike current is an initial
spike of current that lasts a few milliseconds before
the machine goes to start current. In general, the fac-
tory default of 15 amps works for most applications. If
welding on very thin materials with small diameter
tungsten, strike current can be turned down to mini-
mize burning through the weld material. Like-wise for
larger diameter tungsten strike current can be turned
up to put more energy in the tungsten.
3. AC TIG Start Power:
For AC TIG welding AC start power can be adjusted
from the set-up menu to aid starting if required. The
Invertec® V311-T AC/DC when set to AC TIG will try
to initiate the arc with positive polarity until the arc is
established. Positive polarity puts more energy into
heating the tungsten but the drawback is that is can
cause the tungsten to ball excessively or to super
heat. Note super heating of the tungsten can be
noticed if the tungsten is glowing red or orange during
starting. Start Power can be adjusted within two
ranges:
Range
Mode
0.5 to 1
Manual Setting
1.2 to 5.0
Incremental setting
If start power is set within the incremental range
mode, the machine tries to start electrode positive at a
relative setting of 1. If the arc fails to establish it will
repeat the start sequence each time by incrementing
the amount of electrode positive energy by 10% (0.1)
up to the start power limit setting or until the arc estab-
lishes. For comparison a start power limit of 2 if
reached will have twice the energy of the starting point
of 1. If the tungsten has too much of a ball on it or
appears to be super heating during starts the start
power limit can be turned down. In the manual setting
range, the start power will not keep incrementing up to
a limit. Instead the start power stays at whatever level
is set. For example a setting of 0.5 will start the
machine with half the normal starting energy of 1.
STICK CRISP MODE DYNAMIC CURRENT
REGULATION
When running E6010 electrodes DC Crisp mode is
recommended. The Invertec® V311-T AC/DC has a
special dynamic current regulation that is ideal for the
whipping technique common to E6010 electrodes.The
machine regulates the welding current based on
changes in arc length. As the arc length is increased
and the arc voltage increases, the machine will reduce
its welding current below the set point. As the arc
length is decreased and the arc voltage decreases the
machine will increase its current.
FIGURE B.8
Arc Force Control –
Arc Force is a setting that helps
reduce sticking the electrode into the weld puddle.
Increasing the arc force percentage will provide a
higher boost of current when the electrode is about to
short into the weld puddle. In Stick Crisp mode since
the current is dynamically regulated based on the arc
voltage, shorting the electrode to the work will be rare
- therefore, adjustments to the arc force percentage
will not be as noticeable in Stick Crisp mode com-
pared to Stick Soft mode.
INVERTEC® V311-T AC/DC TIG
Weld
Current
Set Point
Increase
Arc Length
Average Arc Length
Decrease
Arc Length