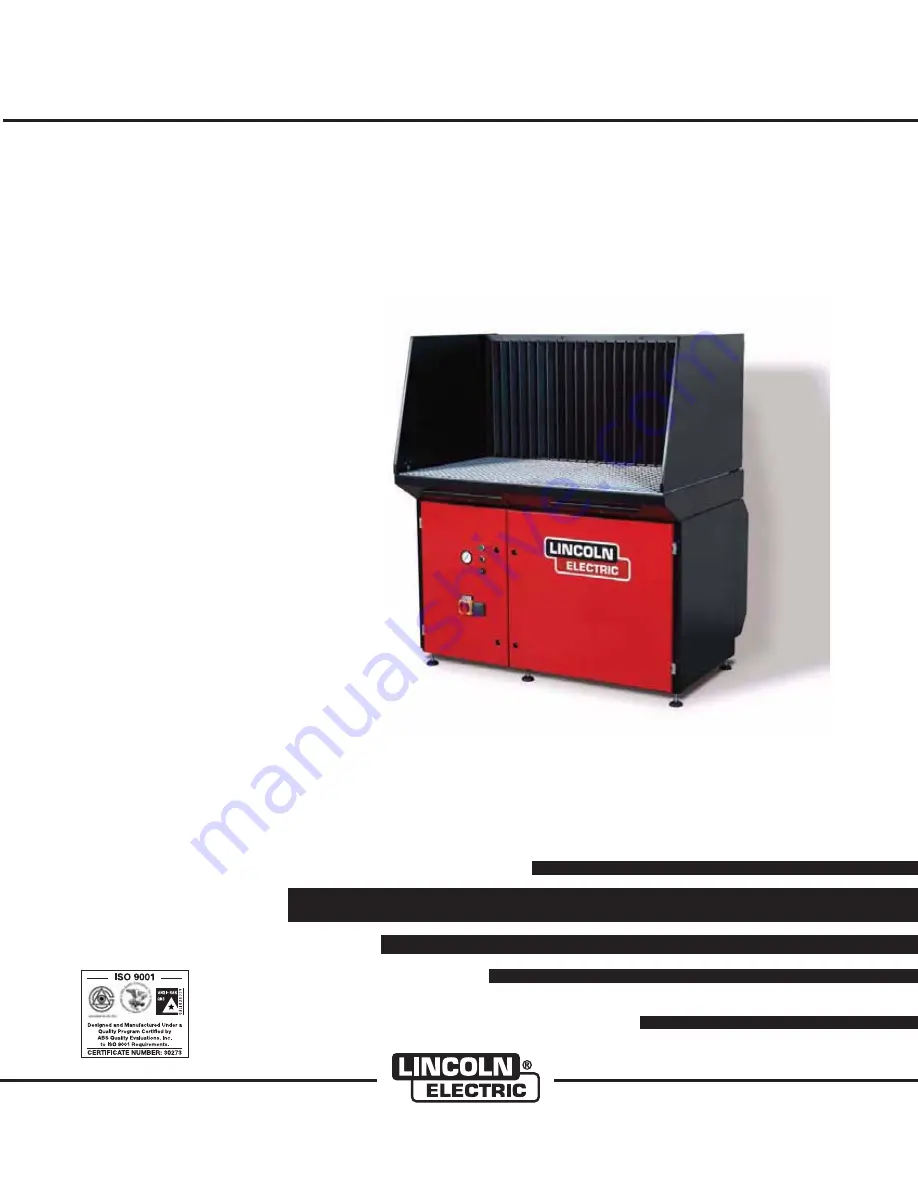
• Sales and Service through Subsidiaries and Distributors Worldwide •
Cleveland, Ohio 44117-1199 U.S.A. TEL: 888.935.3878 FAX: 216.383.8823 WEB SITE: www.lincolnelectric.com
• World's Leader in Welding and Cutting Products •
DOWNFLEX 200/400
INSTRUCTION MANUAL
IM10013
1RYHPEHU
, 2011
Safety Depends on You
Lincoln arc welding and cutting
equipment is designed and built
with safety in mind. However,
your overall safety can be
increased by proper installation
... and thoughtful operation on
your part.
DO NOT INSTALL,
OPERATE OR REPAIR THIS
EQUIPMENT WITHOUT READ-
ING THIS MANUAL AND THE
SAFETY PRECAUTIONS CON-
TAINED THROUGHOUT.
And,
most importantly, think before
you act and be careful.
For use with machines having Code Numbers:
K2751-2, K2751-3, K2751-4,
CK 2751-2, CK 2751-3, CK 2751-4,
CK 2751-25, CK 2751-35
Copyright © Lincoln Global Inc.
Summary of Contents for DOWNFLEX 200
Page 44: ...NOTES DOWNFLEX 200 400...
Page 45: ...NOTES DOWNFLEX 200 400...