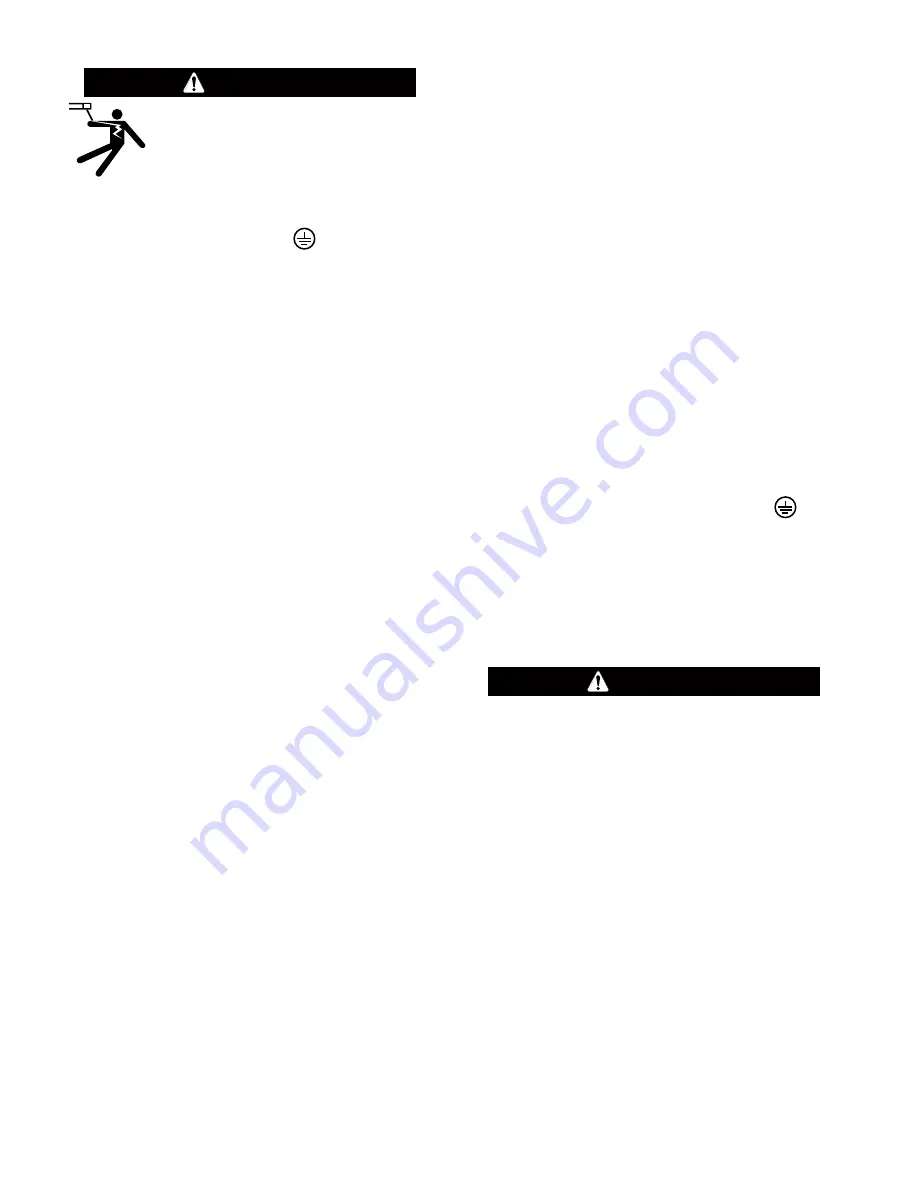
INSTALLATION
Please read all of this section before starting
installation. Refer to Figure 1 during installation.
Location
Place the welder where clean cooling air can freely
circulate in through the front louvers, and out through
the rear louvers. The presence of dirt, dust or any
foreign material that can be drawn in through the
louvers should be kept to a minimum. Failure to
observe these precautions can result in excessive
operating temperatures, and welder shutdowns due to
thermal overload.
DC-650 PRO power sources can be stacked three
high, provided that the bottom machine is on a stable,
hard, level surface. Be sure that the two pins in the
roof of the lower machine fit into the holes in the base
of the DC-650 PRO above it.
Minimizing Problems Due to High
Frequency
This welder, like all electrical equipment, can be
subject to interference from strong sources of high
frequency energy. Sources of high frequency energy
include, but are not limited to, TIG welders, plasma
cutters, and two-way radios. To minimize the
potential for such interference, follow all of the
installation instructions for equipment that will be
installed in the same general area as the DC-650
PRO. Pay particular attention to instructions on
grounding. The best preventative measure is to
locate high frequency generating devices away from
all other electrical equipment. Also, the input power
lines going to those devices should be enclosed in
solid metallic tubing or conduit.
Input Connections
Be sure the voltage, phase and frequency of the input
power is as specified on the rating plate. The rating
plate is located on the front control panel of the DC-
650 PRO.
An entry for the input power lines (#1, Fig. 1) is
provided on the case back. The knockout is 2.00
”
(51
mm) in diameter. Access to the input panel
connection area is gained by removing the two bolts
which secure the Reconnect Door (#2, Fig. 1) and
lifting the door upward.
Select the input lead wire sized according to local and
national electrical codes. A chart conforming to the
U.S. National Electrical Code is provided as a
reference. (Table 1). Have a qualified electrician
connect the input leads to terminals L1, L2 and L3 on
the reconnect panel (#3, Fig. 1), in accordance with all
local and national electrical codes, and with the
diagram (#4, Fig. 1) located on the inside of the cover.
Use a three phase line.
The frame of the welder must be grounded. A ground
terminal (#5, Fig. 1) marked with the symbol
is located on the bottom of the input box for this
purpose. Check local and national electrical codes for
details on proper grounding methods.
On welders with multiple input voltages, be sure that
the reconnect panel is connected per the instructions
that follow.
FAILURE TO FOLLOW THESE INSTRUCTIONS
CAN CAUSE IMMEDIATE FAILURE OF
COMPONENTS INSIDE THE WELDER.
Welders are shipped connected for the highest rated
input voltage. To change this to a lower voltage, first
reconnect the pilot transformer leads H2, H3 or H4 per
the diagram attached to the inside of the reconnect
door. Next, remove and reinstall the reconnect links
according to the same diagram.
Fuse the input leads with the recommended size
super lag fuses or delay type circuit breakers. See
Table 1 for the recommended fuse and/or circuit
breaker sizes. Using fuses or breakers smaller than
those recommended may result in nuisance
“
tripping
”
,
and possible damage to circuit breakers from welder
inrush currents at turn on, even if the machine is not
used to weld at high currents.
–
8
–
–
8
–
ELECTRIC SHOCK can kill.
•
Turn the input power off at the
disconnect switch before installing
or servicing this machine.
•
Do not touch electrically
“
hot
”
parts such as
output terminals or internal wiring.
•
Connect grounding screw to a good
earth ground.
•
Do not operate with covers removed.
•
Turn power switch
“
OFF
”
before connecting
or disconnecting cables or other equipment.
•
Only qualified personnel should install or
service this equipment.
-------------------------------------------------------------
WARNING
CAUTION
Dec 95
Dec 95
Summary of Contents for DC-650 PRO
Page 9: ...9 Figure 1...
Page 30: ...NOTES...