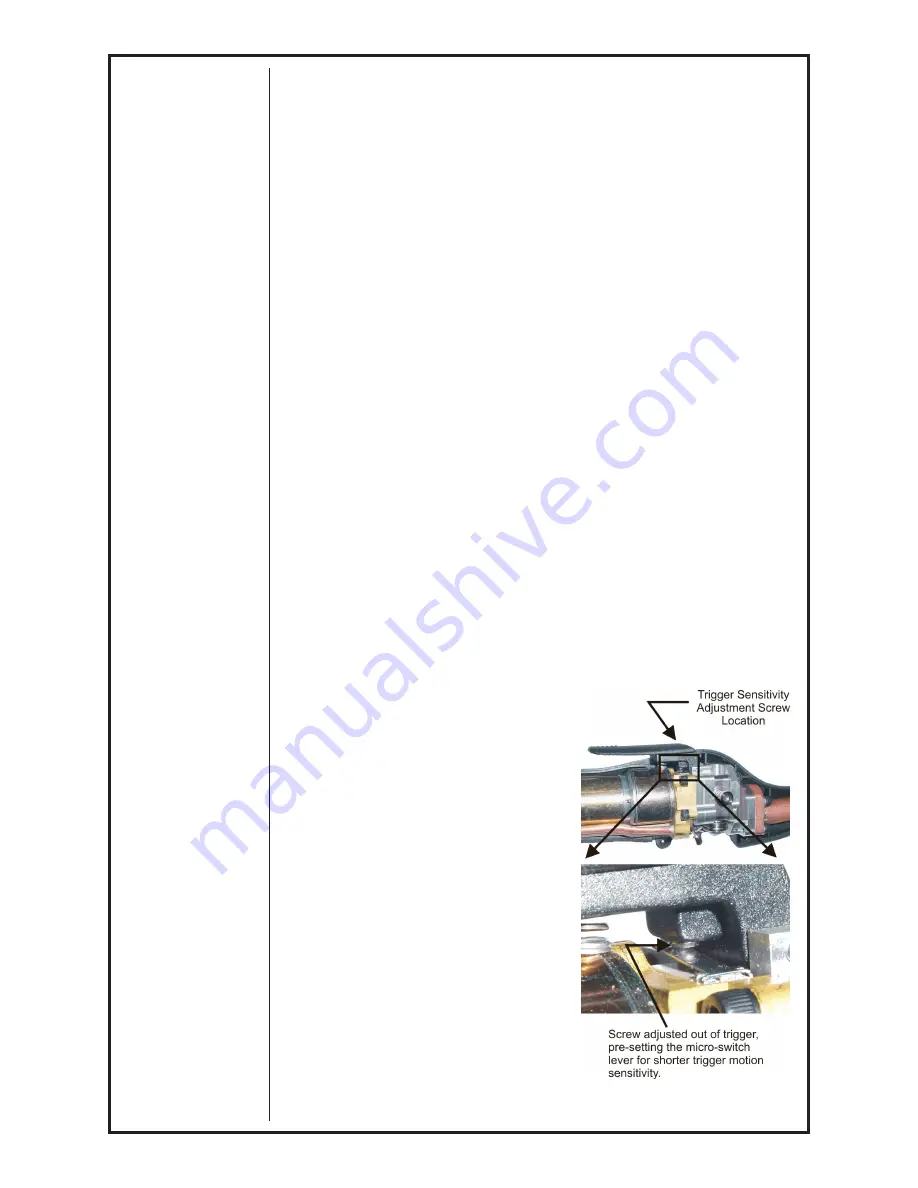
CobraMAX™ Owner's Manual -
Page 2
Gas Hose
The gas hose is secured over the barbed gas fitting with a tie wrap. The
cabinet end of the gas hose uses our standard gas fitting (1/8” - 27 nps).
Water Hose
If so equipped, one end of the water hose is secured over the barbed water
fitting with a tie wrap and the other end is connected to the center fitting on
the power block.
Electric Cable
A seven conductor control cable is used on the CobraMAX
™
gun. The gun
end of the control cable is secured to the gun with a boot clamp and soldered
to the pot assembly, tirgger and water leads. Slack is left in the electric cable
as it exits the back of the gun to prevent cable breakage. The cabinet end
has a seven pin “W” clocked amphenol connector.
Section B
Operation
General
The CobraMAX
™
gun maintains a constant, steady, uniform wire feed speed,
regardless of curved or looped wire conduit. The constant push exerted
by the slave motor in the cabinet, combined with the pull of the gun motor,
causes the wire to literally float friction-free through the wire conduit. The
24VDC gun motor is controlled by a three and three-quarter (3 3/4) turn
potentiometer in the gun handle.
Controls and Settings
Potentiometer
The laterally-positioned potentiometer is located in the lower end of the
handle, providing up to 800 ipm with 3 3/4 turns.
Micro Switch
The micro switch assembly consists of the micro switch and leads.
Trigger Sensitivity
The amount of trigger level travel can
be shortened for a "quicker" or "more
responsive" action.
A more sensitive trigger lever is
produced by reducing the gap between
the trigger lever and the micro switch
lever. By turning-in the trigger sensitivity
adjustment screw, it closed the gap
between the trigger lever and the micro
switch lever.
This will enable the operator to increase
the sensitivity of the trigger lever.
Sensitivity Adjustment
With the wire feeder turned on (with
or without welding wire loaded), turn
the screw in until the micro-switch is
activated. Once activated, the tortch and
wire feeder motors will begin feeding
wire. Retract the screw accordingly until
the system is deactivated and adjusted to
the operators' liking.
Summary of Contents for COBRAMAX IM774
Page 2: ......
Page 5: ...CobraMAX Owner s Manual Page...
Page 8: ...CobraMAX Owner s Manual Page iv...
Page 9: ...CobraMAX Owner s Manual Page...
Page 26: ...CobraMAX Owner s Manual Page 16...