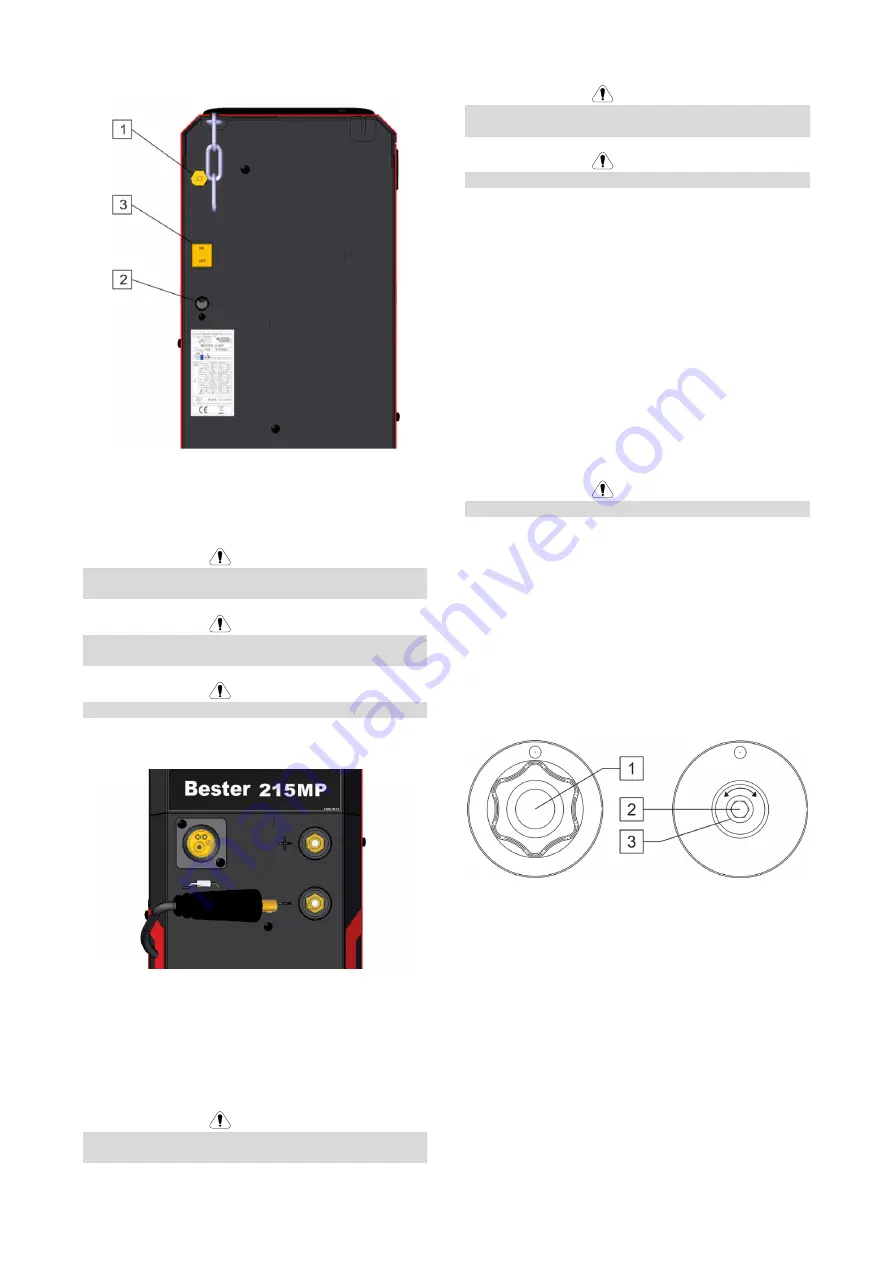
English
10
English
Rear Panel
Figure 3
1. Gas connector
2. Input power cord
3. Power switch
WARNING
When the machine is switched again on, last welding
process will be recalled.
WARNING
If the push-button is pushed in MIG process in, the output
terminals will lived.
WARNING
During MMA process, the output terminals are still lived.
The installation and connection
Figure 4
If the welding polarity has to be changed, user should:
•
Switch off the machine.
•
Determine the polarity for the electrode to be used
(or wire). Consult the data for this information.
•
Select and set the correct polarity: positive (terminal
8) or negative (terminal 9)
WARNING
Before welding check the polarity for using electrodes and
wires.
WARNING
The machine must be used with the door completely
closed during welding.
WARNING
Not use handle to move the machine during work.
Loading the Electrode Wire
•
Turn the machine off.
•
Open the side cover of the machine.
•
Unscrew the locking nut of the sleeve.
•
Load the spool with the wire on the sleeve such that
the spool turns anticlockwise when the wire is fed
into the wire feeder.
•
Make sure that the spool locating pin goes into the
fitting hole on the spool.
•
Screw in the fastening cap of the sleeve.
•
Put on the wire roll using the correct groove
corresponding to the wire diameter.
•
Free the end of the wire and cut off the bent end
making sure it has no burr.
•
The device is adapted to the spool max. 15 kg
300 mm
WARNING
Sharp end of the wire can hurt.
•
Rotate the wire spool anticlockwise and thread the
end of the wire into the wire feeder as far as the Euro
socket.
•
Adjust force of pressure roll of the wire feeder
properly.
Adjustments of Brake Torque of Sleeve
To avoid spontaneous unrolling of the welding wire the
sleeve is fitted with a brake.
Adjustment is carried by rotation of its Allen screw M8,
which is placed inside of the sleeve frame after
unscrewing the fastening cap of the sleeve.
Figure 5
1. Fastening cap.
2. Adjusting Allen screw M8.
3. Pressing spring.
Turning the Allen screw M8 anticlockwise increases the
spring tension and you can increase the brake torque
Turning the Allen screw M8 clockwise decreases the
spring tension and you can decrease the brake torque.
After finishing of adjustment, you should screw in the
fastening cap again.