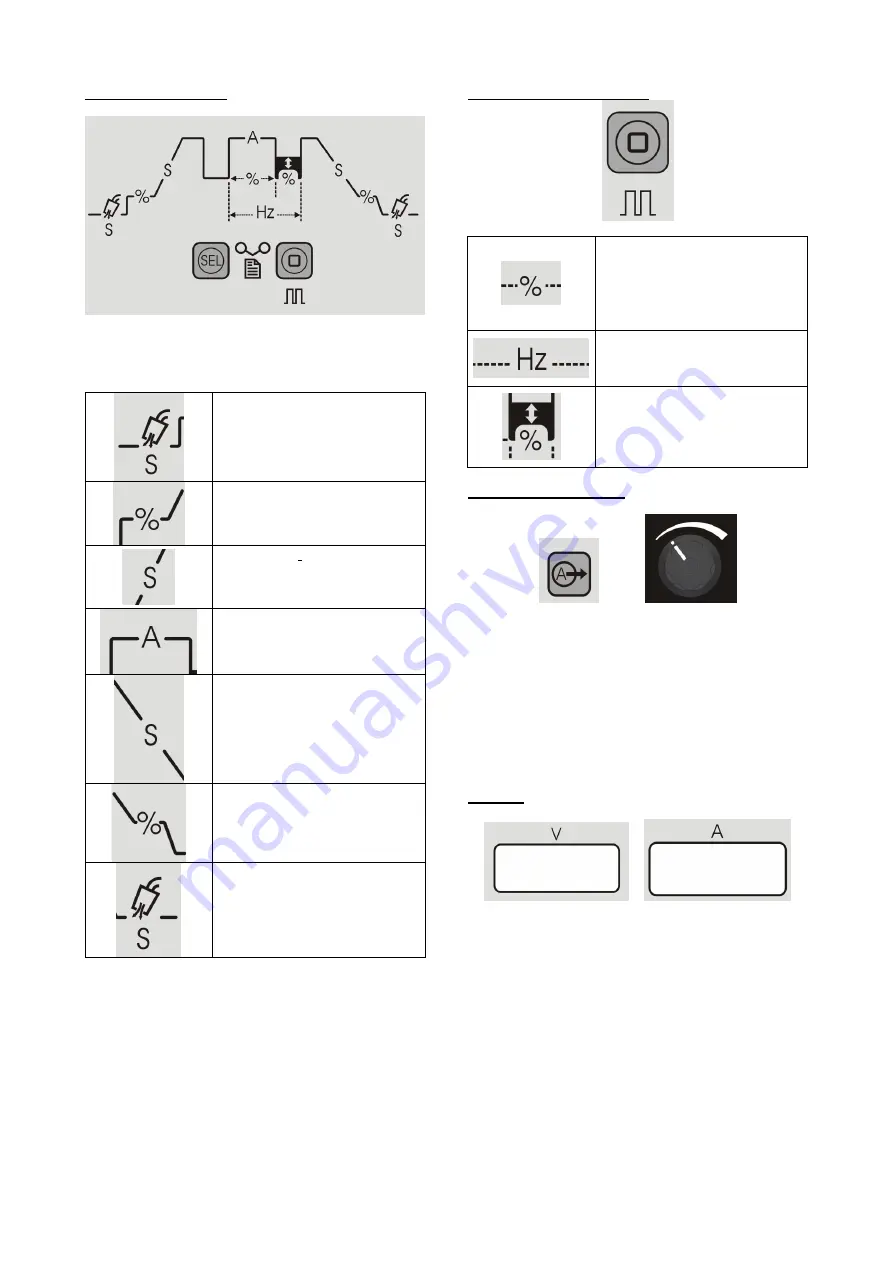
English 11
English
Sequencer Functions:
The sequencer allows for the customization of the TIG
welding operation both in AC & DC- polarities. Pressing
the “Sel” button will cycle through the process graph.
Pre-Flow
: Sets the time in
seconds gas will flow prior to arc-
start initiation
Starting Current
: Sets the
starting amperage for the
process.
Initial Slope
: Sets the time in
seconds it takes the starting
current to reach normal operating
amperage.
Operating Amperage
: Sets the
amperage for all welding process
permitted.
Final Slope:
Sets the time in
seconds it takes the operating
amperage to ramp down to the
Finishing current.
Finishing Current:
Sets the
finishing amperage for the
process.
Post Flow:
Sets the time in
seconds gas will flow after the arc
is terminated
Pulse Sequencer Functions:
Percent Peak Current:
This
functions sets the amount of time
the pulse waveform spends at the
peak current setting. This
function is set as a percentage of
the total time for the pulse cycle.
Pulses-Per-Second:
Sets the
total number of pulse cycles per
second of time.
Percent Background Current:
Sets the background amperage of
the pulse waveform. Background
amperage is set as a percentage
of the peak current.
Main Amperage Control:
The main amperage control button is intended to be a quick
selection method to adjust the main amperage setting. This
function will allow users to quickly exit the sequencer
portion of the U/I, eliminating the need to cycle through all
possible sequencer functions to adjust the main amperage
or exit the sequencer menu.
This knob is also a multi-purpose command: see the
“Operating Instruction” section for a description of how to
use this command for parameter selection.
Displays:
The right meter displays the preset welding current (A) before
welding and the actual welding current during welding, and
the left meter shown the voltage (V) at the output leads.
A flashing on both displays indicate that the value read is
the average value of the previous welding operation. This
feature shown the average value for 5seconds after every
welding time.
If a remote control is connected (the Remote LED is ON),
the left meter (A) indicates the preset and the actual
welding current following the instruction explained in the
“Remote LED” description above.
The dispays are used to indicate during setting of
parameters, the name and the value of them. Also are used
for menu indication and error codes displaing.