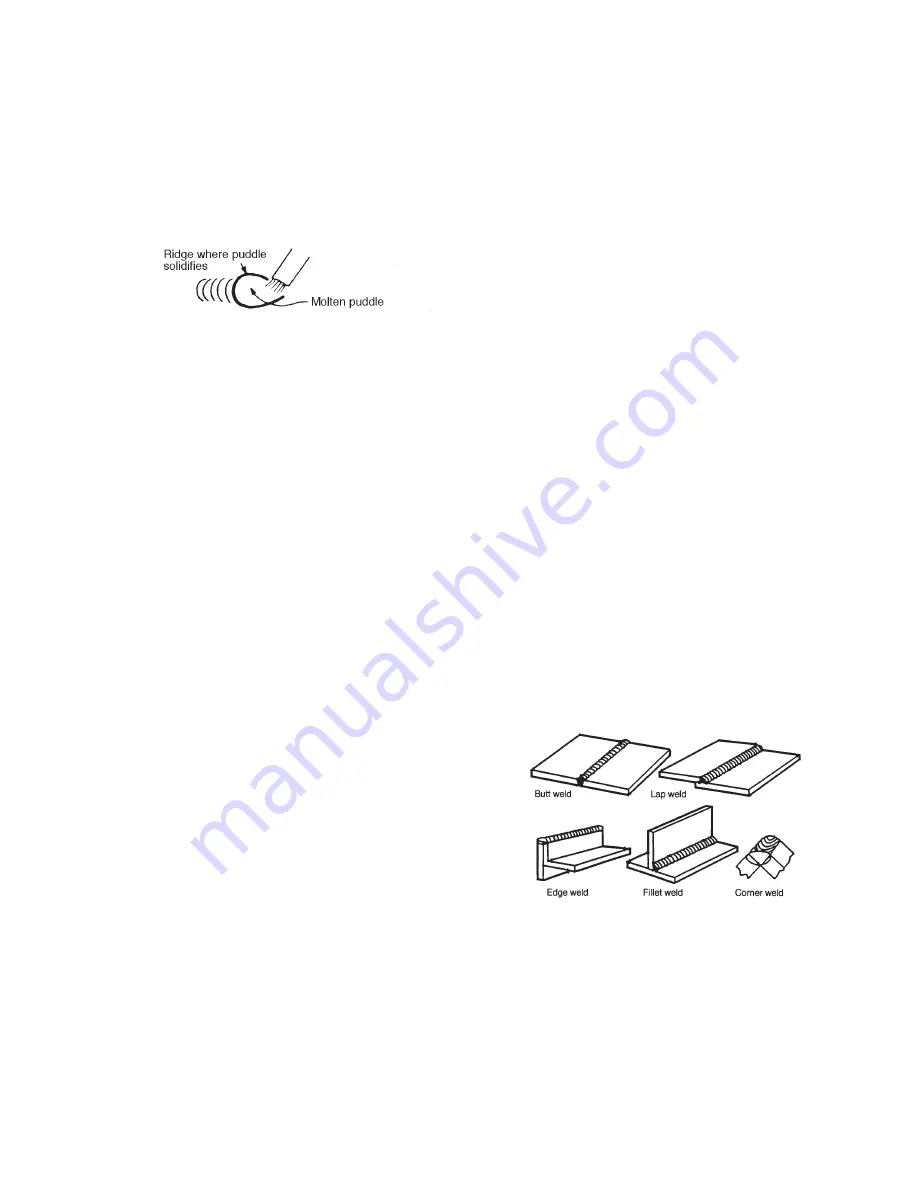
– 13 –
4. The Correct Welding Speed
The important thing to watch while welding is the puddle
of molten metal right behind the arc.
Do NOT watch the
arc itself.
It is the appearance of the puddle and the ridge
where the molten puddle solidifies that indicate correct
welding speed. The ridge should be approximately 3/8"
(9.5mm) behind the electrode.
Most beginners tend to weld too fast, resulting in a thin,
uneven, “wormy” looking bead. They are not watching the
molten metal.
IMPORTANT:
For general welding it is not necessary to
weave the arc; neither forwards and backwards nor side-
ways. Weld along at a steady pace. You will find it easier.
NOTE:
When welding on thin plate, you will find that you
will have to increase the welding speed, whereas when
welding on heavy plate, it is necessary to go more slowly
in order to get good penetration.
Practice
The best way of getting practice in the four skills that
enable you to maintain:
1 Correct Welding Position
2. Correct Way To Strike An Arc
3. Correct Arc Length
4. Correct Welding Speed
is to spend a little more time on the following exercise.
Use the following:
Mild Steel Plate ......................3/16" (4.8mm) or heavier
Electrode ............................1/8" (3.2mm) Fleetweld 180
Current Setting..........................................105 Amps AC
Do the following:
1. Learn to strike the arc by scratching the electrode over
the plate. Be sure the angle of the electrode is correct. If
you have a headshield use both hands.
2. When you can strike an arc without sticking, practice the
correct arc length. Learn to distinguish it by its sound.
3. When you are sure that you can hold a short, crackling
arc, start moving. Look at the molten puddle constantly,
and look for the ridge where the metal solidifies.
4. Run beads on a flat plate. Run them parallel to the top
edge (the edge farthest away from you). This gives you
practice in running straight welds, and also, it gives you
an easy way to check your progress. The 10th weld will
look considerably better than the first weld. By con-
stantly checking on your mistakes and your progress,
welding will soon be a matter of routine.
Common Metals
Most metals found around the farm or small shop are low
carbon steel, sometimes referred to as mild steel. Typical
items made with this type of steel include most sheet metal,
plate, pipe and rolled shapes such as channels, angle irons
and “I’’ beams. This type of steel can usually be easily
welded without special precautions. Some steel, however,
contains higher carbon. Typical applications include wear
plates, axles, connecting rods, shafts, plowshares and
scraper blades. These higher carbon steels can be welded
successfully in most cases; however, care must be taken to
follow proper procedures, including preheating the metal to
be welded and, in some cases, carefully controlling the
temperature during and after the welding process. For fur-
ther information on identifying various types of steels and
other metals, and for proper procedures for welding them,
we again suggest you purchase a copy of “New Lessons in
Arc Welding” (see page 25).
Regardless of the type of metal being welded, it is impor-
tant in order to get a quality weld that it be free of oil, paint,
rust or other contaminants.
Types of Welds
Five types of welding joints are: Butt Welds, Fillet Welds,
Lap Welds, Edge Welds and Corner Welds.
Of these, the Butt Weld and Fillet Weld are the two most
common welds.
Butt Weld
Butt Welds are the most widely used welds. Place two
plates side by side, leaving 1/16” (1.6mm) (for thin metal)
to 1/8” (3.2mm) (for heavy metal) space between them in
order to get deep penetration .