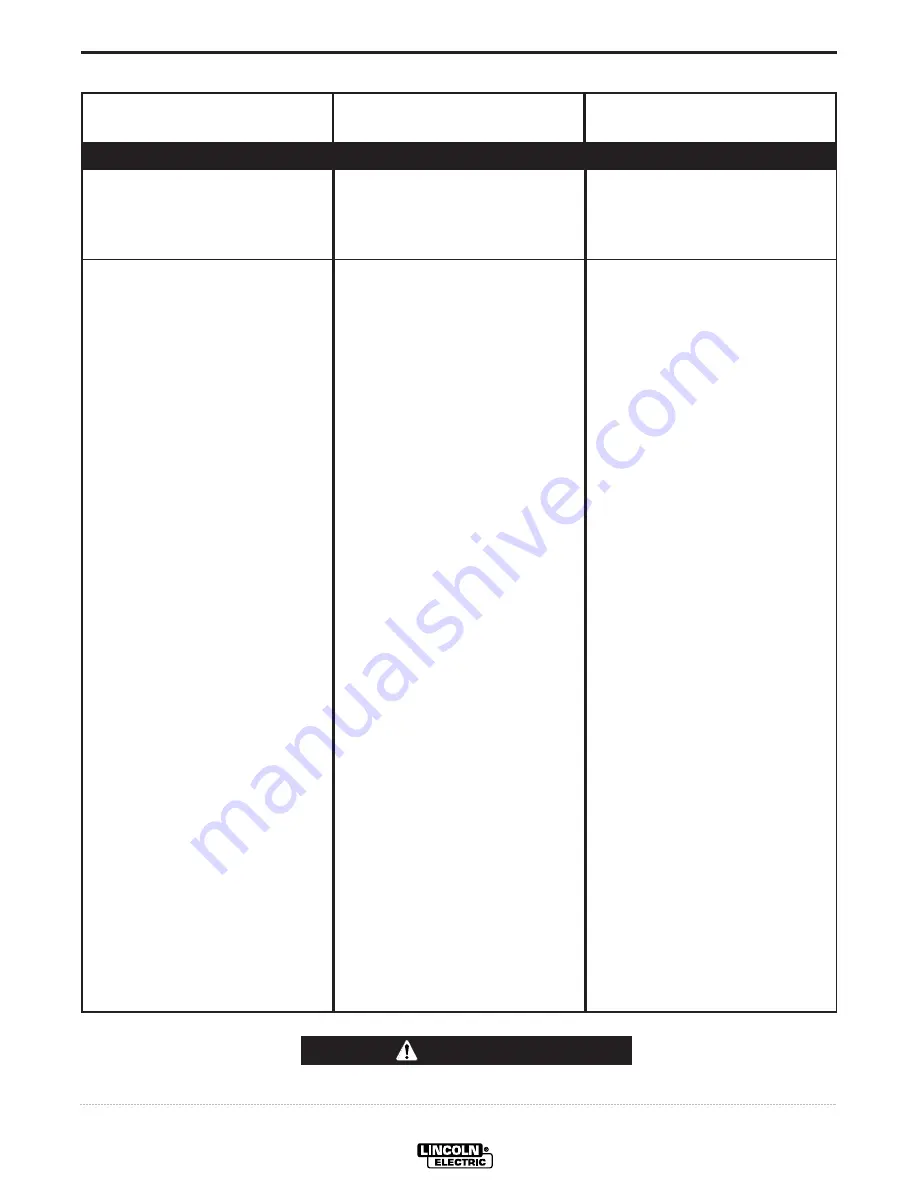
E-2
TROUBLESHOOTING
E-2
IDEALARC R3R 375-I, 500-I AND 600-I
Observe all Safety Guidelines detailed througout this manual
If for any reason you do not understand the test procedures or are unable to perform the tests/repairs safely, contact your
Local
Lincoln Authorized Field Service Facility
for technical troubleshooting assistance before you proceed.
CAUTION
FUNCTION PROBLEMS
PROBLEMS
(SYMPTOMS)
POSSIBLE CAUSE
RECOMMENDED
COURSE OF ACTION
A. Input contactor chatters.
B. Machine input contactor does not
operate.
1.Faulty input contactor.
2.Low line voltage.
1.Supply line fuse blown.
2.Power circuit dead.
3.Broken or loose power lead.
4.Wrong voltage.
5.Thermostats tripped. (High
Temperature Warning Light
should be lit.) (Welder
overheated.)
6.Input contactor coil open.
7.Open winding on 115V pilot
transformer.
8.Power ON-OFF switch not
closing.
9.Lead broken or loose connec-
tion in 115V starter circuit.
10.Thermostats defective. (High
Temperature Warning Light
should be lit.)
1.Repair or replace.
2.Check with Power Company.
1.Replace (look for reason for
blown fuse first).
2.Check voltage.
3.Repair.
4.Check voltage against
instructions.
5.a. Make sure the fan is operating
and that there are no obstruc-
tions to free flow of air.
b. Operate at normal current
and duty cycle.
c. Replace High Temperature
Warning Light if defective.
6.Replace.
7.Replace.
8.Replace.
9.Replace.
10.Turn input power off (115V cir-
cuit is hot when input power is
connected). Check thermostats
with continuity meter – should
read short-circuit when machine
is cool. Replace if defective.
There are two thermostats; one
on the secondary lead and one
on the choke. Replace High
Temperature Warning Light if
defective.