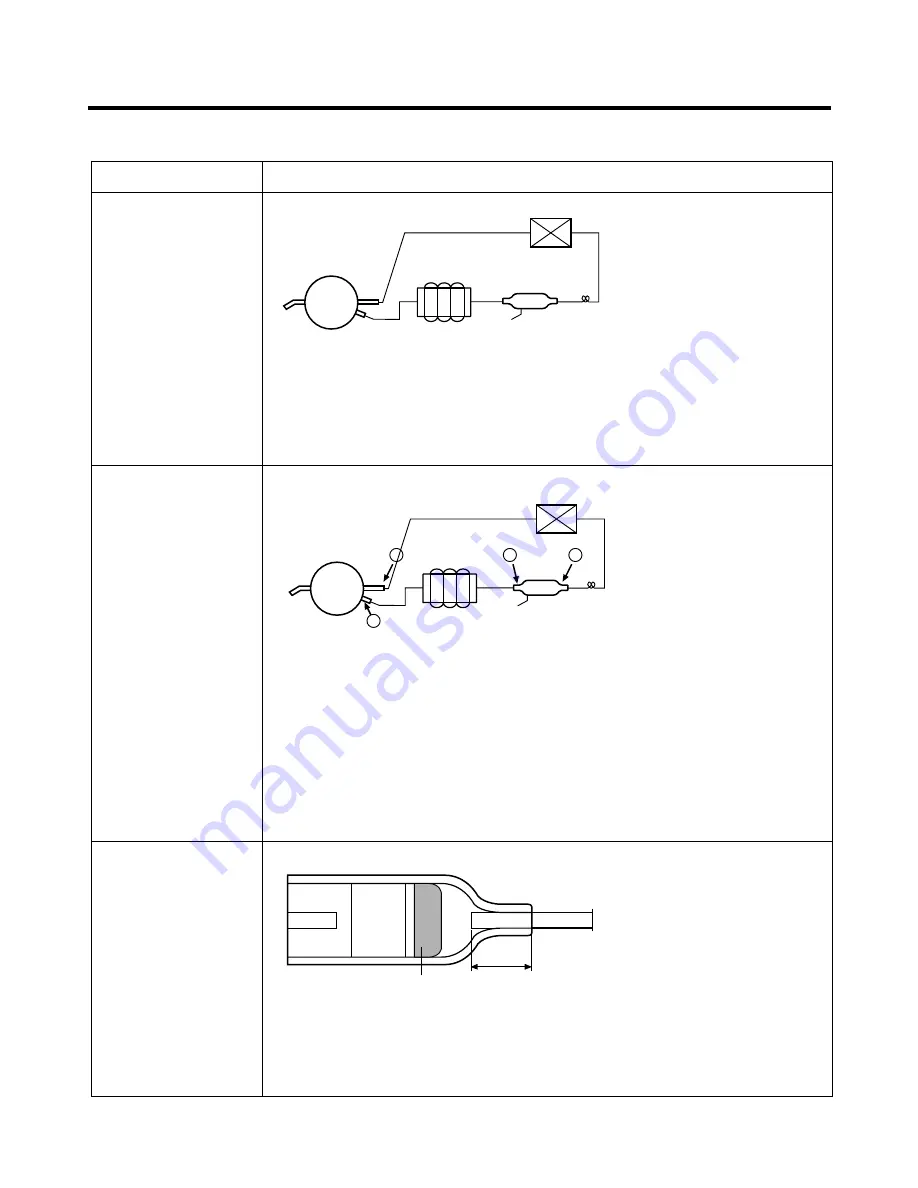
3-4. Practical Work For Heavy Repair
TROUBLE DIAGNOSIS
- 105 -
Items
Precautions
1. Removal of residual
refrigerant.
1) Remove residual refrigerant more than 5 minutes later after turning off the refrigerator.
( If not, compressor oil may leak inside.)
2) Remove retained refrigerant slowly by cutting first high pressure side (drier part) with a
nipper and then cut low pressure side.
2. Nitrogen blowing
welding.
When replacing a drier:
Weld
and
parts by blowing nitrogen(0.1~0.2kg/cm
2
) to high pressure side after
assembling a drier.
When replacing a compressor:
Weld
and
parts by blowing nitrogen to the low pressure side.
Note) For other parts, nitrogen blowing is not necessary because it does not produce oxidized
scales inside pipe because of its short welding time.
3. Replacement of drier.
Inserting a capillary tube
Measure distance with a ruler and put a mark(12
+3/-0
)on the capillary tube. Insert tube to the
mark, and weld it
KEYPOINTING
Observe the sequence for
removal of refrigerant.
(If not, compressor oil may
leak.)
KEYPOINTING
Welding without nitrogen
blowing produces oxidized
scales inside a pipe, which
affect on performance and
reliability of a product.
KEYPOINTING
Be sure to check the
inserted length of capillary
tube when it is inserted. (If
too much inserted, a
capillary tube is clogged by
a filter.)
Compressor
Low pressure side
Condenser
High pressure side
Drier
Evaporator
Release
Refrigent
Intake
Suction
1
2
1
2
Evaporator
Drier
High pressure side
Condenser
Refrigent
Intake
12
+
3
-
0
Filter
* Unit : mm
Summary of Contents for SXS Refrigerator
Page 27: ...EXPLATION FOR MICOM CIRCUIT 27 GW P L227 88 LED GW P L227 Bar LED ...
Page 30: ...EXPLATION FOR MICOM CIRCUIT 30 GW P L227 Bar LED ...
Page 39: ...EXPLATION FOR MICOM CIRCUIT 39 GW B C227 88 LED E A B C D ...
Page 45: ...EXPLATION FOR MICOM CIRCUIT 45 GW P L227 Bar LED b a e d ...
Page 46: ...EXPLATION FOR MICOM CIRCUIT 46 GW B C227 88 LED GW B C227 Bar LED b a e d b a e d ...
Page 50: ...1 11 Display Circuit EXPLATION FOR MICOM CIRCUIT 50 GW P L227 ...
Page 51: ...EXPLATION FOR MICOM CIRCUIT 51 GW B C227 ...
Page 53: ...EXPLATION FOR MICOM CIRCUIT 53 GW B C227 88 LED GW B C227 Bar LED ...
Page 56: ...EXPLATION FOR MICOM CIRCUIT 56 GW P L227 Bar LED ...
Page 57: ...EXPLATION FOR MICOM CIRCUIT 57 GW B C227 88 LED ...
Page 58: ...EXPLATION FOR MICOM CIRCUIT 58 GW B C227 Bar LED ...
Page 59: ...3 2 Parts List EXPLATION FOR MICOM CIRCUIT 59 GW P L227 88 LED ...
Page 60: ...EXPLATION FOR MICOM CIRCUIT 60 GW P L227 88 LED ...
Page 61: ...EXPLATION FOR MICOM CIRCUIT 61 GW P L227 Bar LED ...
Page 62: ...EXPLATION FOR MICOM CIRCUIT 62 GW P L227 Bar LED ...
Page 63: ...EXPLATION FOR MICOM CIRCUIT 63 GW B C227 88 LED ...
Page 64: ...EXPLATION FOR MICOM CIRCUIT 64 GW B C227 88 LED ...
Page 65: ...EXPLATION FOR MICOM CIRCUIT 65 GW B C227 Bar LED ...
Page 66: ...EXPLATION FOR MICOM CIRCUIT 66 GW B C227 Bar LED ...
Page 73: ...CIRCUIT 73 GW P L B C227 88 LED ...
Page 74: ...CIRCUIT 74 GW P L B C227 Bar LED ...
Page 128: ...P No MFL38540601 MAR 2007 Printed in Poland ...