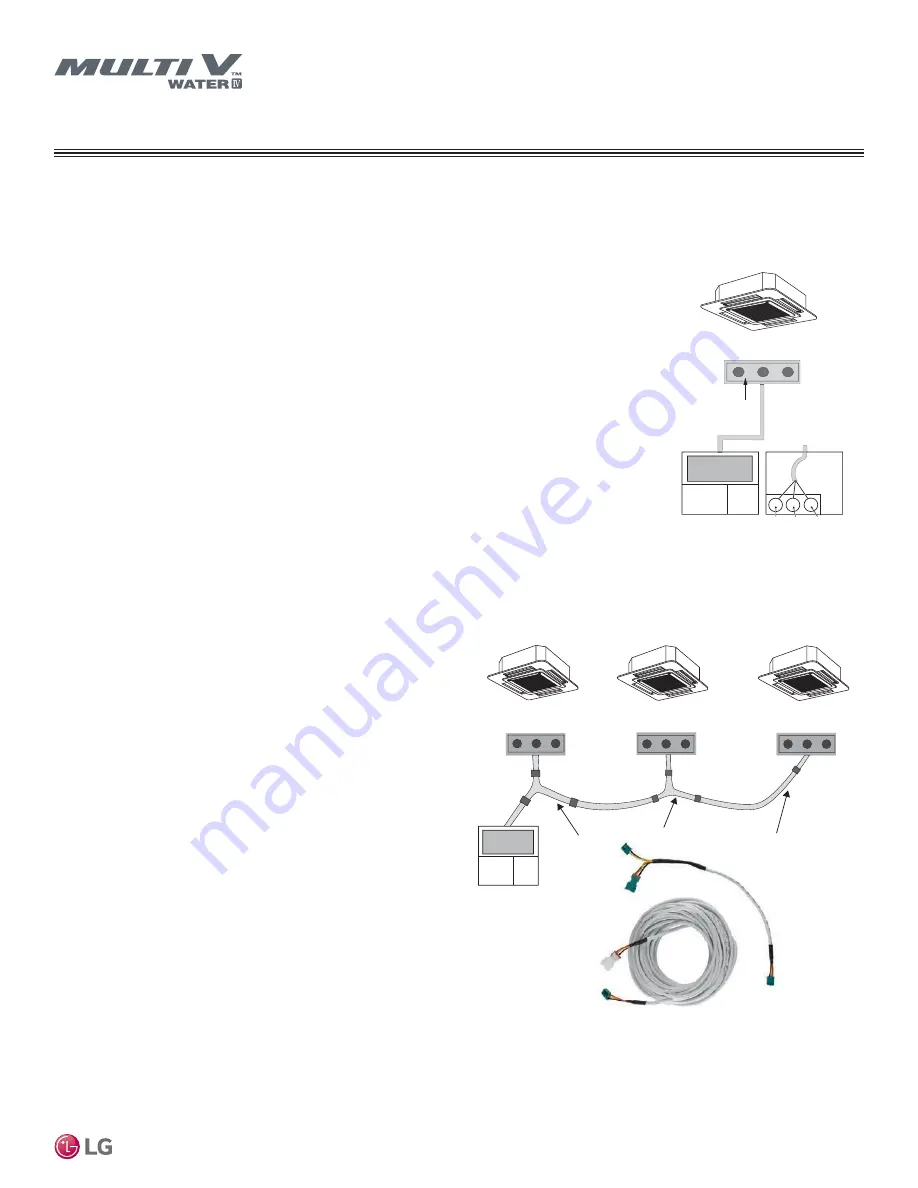
91
Electrical System Installation
Due to our policy of continuous product innovation, some specifications may change without notification.
©LG Electronics U.S.A., Inc., Englewood Cliffs, NJ. All rights reserved. “LG” is a registered trademark of LG Corp.
Communication Cable Between the Indoor Units and the
Wall-Mounted Zone Controller
Communication Cable Between Multiple Indoor Units
Operating as a Group (Group Control)
• Use only LG-provided three-conductor communications cable between the indoor unit and the
wall-mounted zone controller.
• NEVER splice, cut, or extend cable length with field provided cable. If the length must be extended,
use the LG Extension Kit (sold separately). A maximum of four (4) kits (up to 165 feet) can be
connected together.
• Set the indoor unit operating parameters with DIP switches on the indoor unit control PCB or by
setting the zone controller. Refer to the indoor unit installation manuals for details.
• If any indoor units operate as a group, use one (or multiple)
three-core Group Control Kit (sold separately) containing
extension and Y-splitter cables. One (1) group control cable kit
is required for each indoor unit in the group except for the last
indoor unit.
• Always use an LG provided group control communications
cable (Group Control Kit; sold separately) between the indoor
unit and the wall-mounted zone controller.
• NEVER splice or cut the communications cable. Do not short-
en the cable or extend cable length with field provided cable.
• Before running cable, decide which indoor unit will be the mas-
ter indoor unit. The zone controller connects to the master.
• Adjust the appropriate DIP switch at each indoor unit in the
group to identify it as the master or a slave. On wall mounted
indoor unit models, set the assignment using the handheld
remote controller.
• Use a daisy chain configuration and connect all of the group’s
indoor units together starting at the Master unit.
Communication Cable
ELECTRICAL SYSTEM INSTALLATION
CN-REMO
On All Indoor Unit Styles
CN-REMO
On All Indoor Unit Styles
CN-REMO
On All Indoor Unit Styles
LG
Supplied
LG Supplied Group Control Kit (PZCWRCG3)
CN-REMO
On All Indoor Unit Styles
LG Supplied
Cable Assembly
To CN_REMO
Connector on
IDU Control PCB
Yellow
Black
Red
Front
Back
Figure 76:Indoor Unit to Zone
Controller Connection.
Note:
Cable connected to Zone Controller is the factory default connection.
Note:
Cable connected to Zone Controller is the factory default connection.
Figure 77:Indoor Unit Group to Zone Controller Connections.