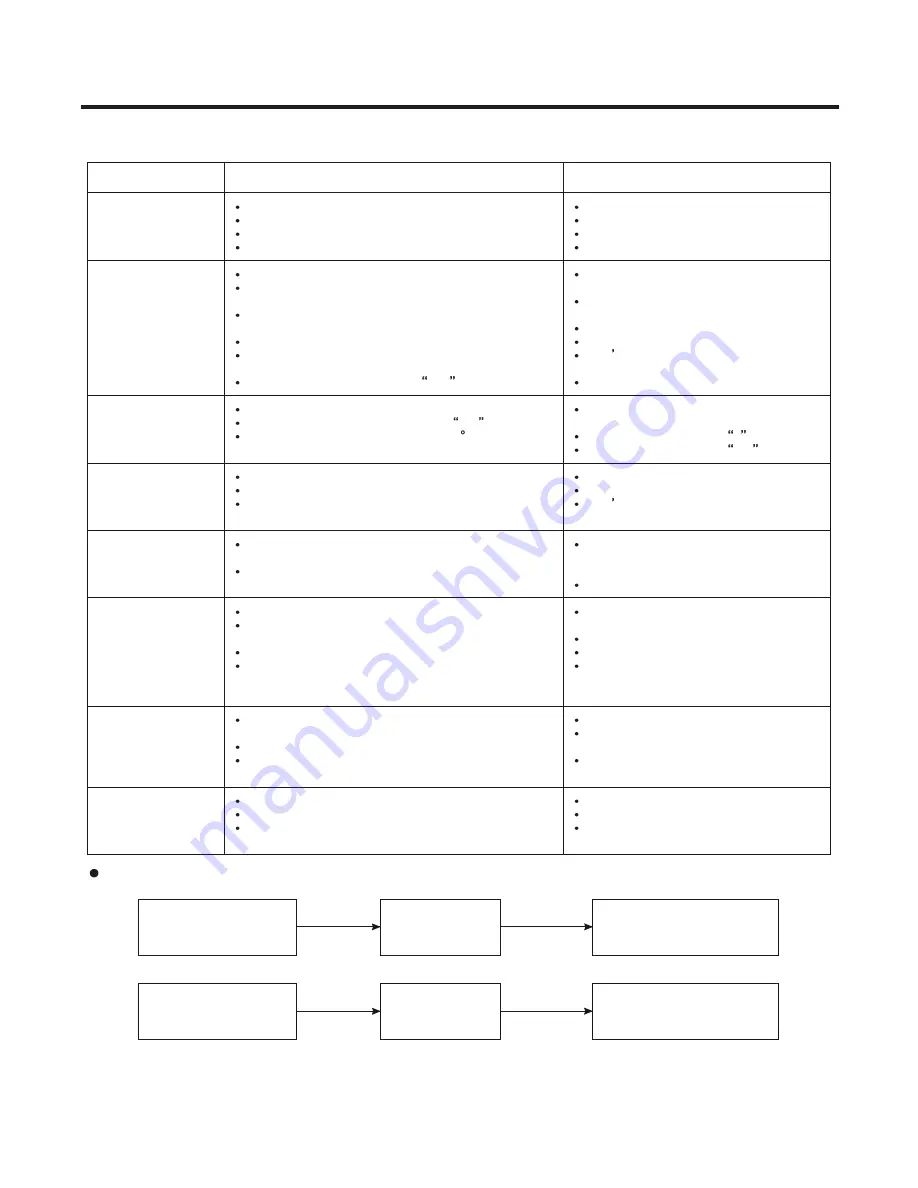
Defrosting is
poor.
4-2 SERVICE DIAGNOSIS CHART
Cooling is
impossible.
Is the power cord unplugged from the outlet?
Checked if the power S/W is set to OFF.
Check if the fuse of power S/W is shorted.
Measure the voltage of power outlet.
Check if the set is placed close to wall.
Check if the set is placed close to stove, gas,
cooker and direct rays.
Is the ambient temperature high or the room door
closed?
Check if putting in hot foods foods.
Did you open the door of the set too often or check
if the door is closed up?
Check if the Control is set to Min .
Are foods placed in cooling air outlet?
Check if the Display LED is set to 0-1 .
Is the ambient temperature below 5 C.
Is watery foods kept?
Check if putting in hot foods.
Did you open the door of the set too often or check
if the door is closed up.
Check if ambient temperature and humidity of
surrounding air are high.
Is the gap in the door packed?
Is the set positioned in a firm and even place?
Does any unnecessary objects exists in the back
side of the set?
Check if the Drip tray is not firmly fixed?
Check if the cover of mechanical room in below
and back side is taken out.
Check if the door packing becomes dirty by filth
such as juice.
Is the set positioned in a firm and even place?
Is too much food putted in the set?
Check if the inside of the set becomes dirty.
Did you keep smelly foods without wrapping?
It smells plastic.
Plug to the outlet.
Set the switch to ON.
Replace a regular fuse.
If voltage is low, wire newly.
Place the set with the space of about
10cm
Place the set apart from these heat
appliances.
Make the ambient temperature below.
Put in foods after they get cold cold.
Don t open the door too often and
close it firmly.
Set the control to mid-position.
Place foods in high temperature
section. (Front part)
Set the Display LED to 3 .
Set the Display LED to 5-6 .
Seal up watery foods with wrap.
Put in foods after they get cold.
Don t open the door too often and
close it firmly.
Wipe dew with a dry cloth. This
happening is solved in low temperature
and humidity naturally.
Fill up the gap.
Adjust the leveling screw, and position
in the firm place.
Remove the objects.
Fix it firmly on an original position.
Place the cover at an original position.
Clean the door packing.
Position in the firm place and adjust the
adjust screw.
Keep foods not to reach the door.
Clean the inside of the set.
Wrap smelly foods.
The new products smell plastic, but it is
removed after 1-2 weeks.
Cooling ability is
poor.
Foods in the
refrigerator
are frozen.
Dew or ice forms in
the chamber of the
set set.
Dew forms in the
Out Case.
Abnormal noise
generates.
To close the door
is not handy.
Ice and foods
smell unpleasant.
In addition to the items describes left, refer to the following to solve the complaint.
Check if dew forms
in the freezer.
Replace the
components of
defrosting circuit.
Check refrigerator
Cycle.
The cycle is
faulty.
Repair the cycle.
COMPLAINT
N
O
I
T
C
A
E
C
I
V
R
E
S
D
E
K
C
E
H
C
E
B
O
T
S
T
N
I
O
P
Copyright © 20
LG Electronics Inc. All rights reserved.
Only training and service purposes.
18
Summary of Contents for LTCS20020W
Page 51: ...Mar 2020 MFL71772901 ...