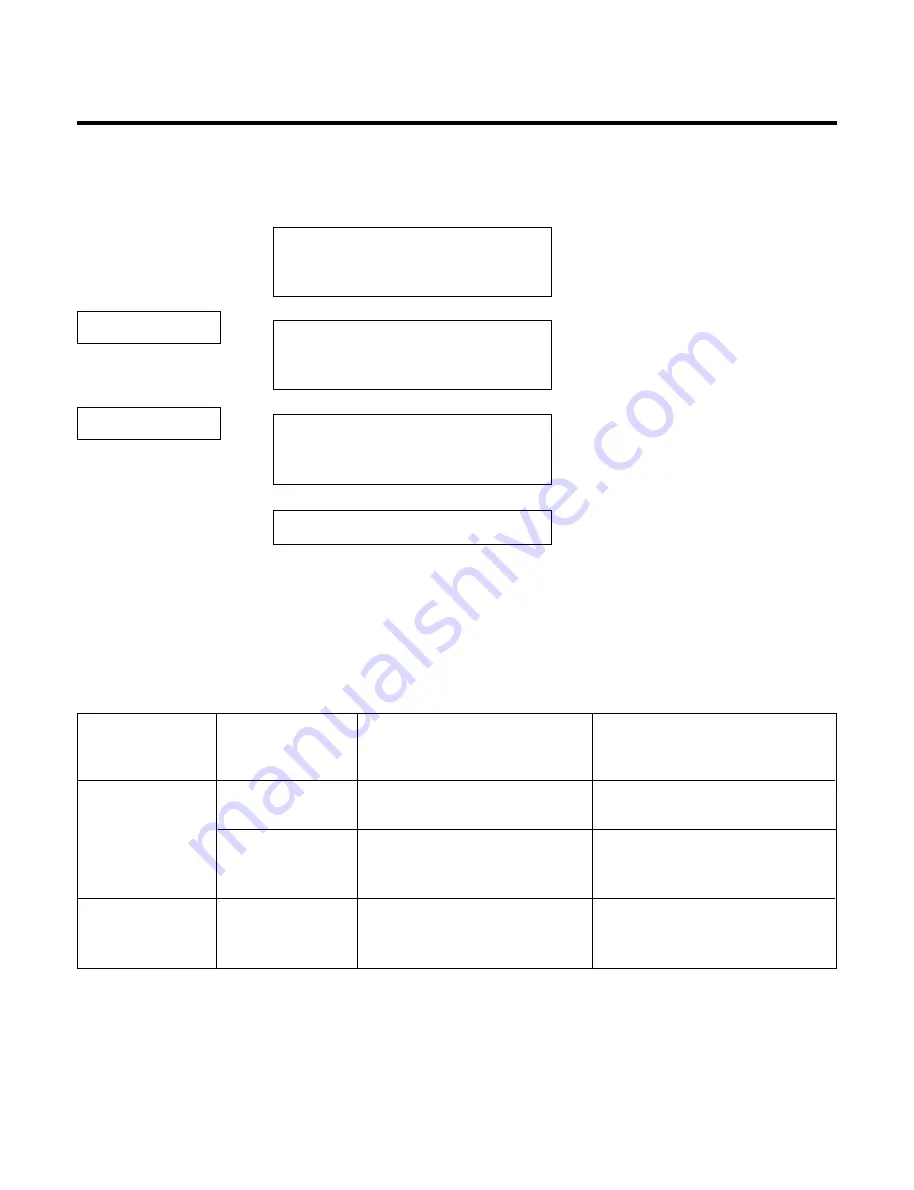
Cycle Troubleshooting Guide
Trouble analysis
1. Check temperature difference between intake and discharge air and operating current.
Temp. Difference
Temp. difference : approx. 0°C
Current : less than 80% of
rated current
Temp. difference : approx. 8°C
Current : less than 80% of
rated current
Temp. difference : less than 8°C
Current : over the rated
current
Temp. difference : over 8°C
Operating Current
All amount of refrigerant leaked out
Check refrigeration cycle
Refrigerant leakege
Clog of refrigeration cycle
Defective compressor
Excessive amount of refrigerant
Normal
Notice :
Temperature difference between intake and discharge air depends on room air humidity. When the room air
humidity is relativery higher, temperature difference is smaller. When the room air humidity is relatively lower
temperature difference is larger.
2. Check temperature and pressure of refrigeration cycle.
Notice :
1. The suction pressure is usually 4.5~6.0 kg/cm
2
G at normal condition.
2. The temperature can be measured by attaching the thermometer to the low pressure tubing and wrap it with
putty.
Suction pressure
Temperature
(Compared with
(Compared with
Cause of Trouble
Description
the normal value)
the normal value)
Defective compressor
Current is low
Defective 4-way reverse valve
Excessive amount of
High pressure does not quickly
Normal
refrigerant
rise at the beginning of
operation
Insufficient amount of
Current is low
Lower Higher
refrigerant
(Leakage)
Clogging
Current is low
High
Higher
–39–