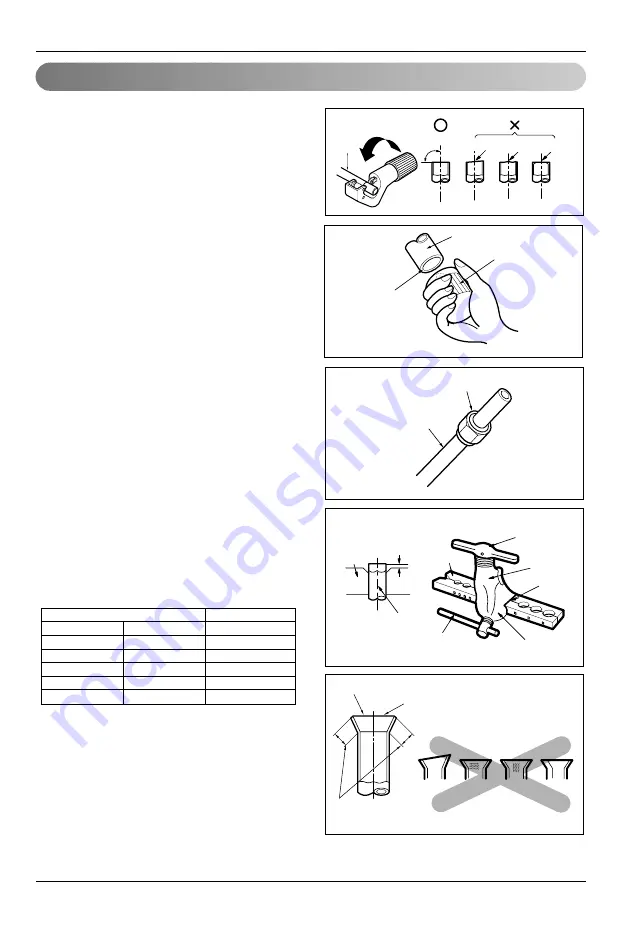
Installation Manual
11
Installation of Unit
Preparation of Piping
Main cause of gas leakage is defect in flaring
work. Carry out correct flaring work in the
following procedure.
1. Cut the pipes and the cable.
• Use the accessory piping kit or the pipes
purchased locally.
• Measure the distance between the indoor
and the outdoor unit.
• Cut the pipes a little longer than measured
distance.
• Cut the cable 1.5m longer than the pipe
length.
2. Burrs removal
• Completely remove all burrs from the cut
cross section of pipe/tube.
• Put the end of the copper tube/pipe to
downward direction as you remove burrs in
order to avoid to let burrs drop in the tubing.
3. Putting nut on
• Remove flare nuts attached to indoor and
outdoor units, than put them on pipe/tube
having completed burr removal.
(Not possible to put them on after flaring work)
4. Flaring work
• Carry out flaring work using dedicated
flaring tool for R-22 as shown below.
Firmly hold copper tube in a bar(or die) as
indicated dimension in the table above.
5. Check
• Compare the flared work with figure below.
• If flare is noted to be defective, cut off the
flared section and do flaring work again.
Copper
tube
90
°
Slanted Uneven Rough
Pipe
Reamer
Point down
Flare nut
Copper tube
Bar
Copper pipe
Clamp handle
Red arrow mark
Cone
Yoke
Handle
Bar
"A"
Inclined
Inside is shining without scratches
Smooth all round
Even length
all round
Surface
damaged
Cracked Uneven
thickness
= Improper flaring =
Outside diameter
A
mm
inch
mm
Ø6.35
1/4
0~0.5
Ø9.52
3/8
0~0.5
Ø12.7
1/2
0~0.5
Ø15.88
5/8
0~1.0
Ø19.05
3/4
0~1.0