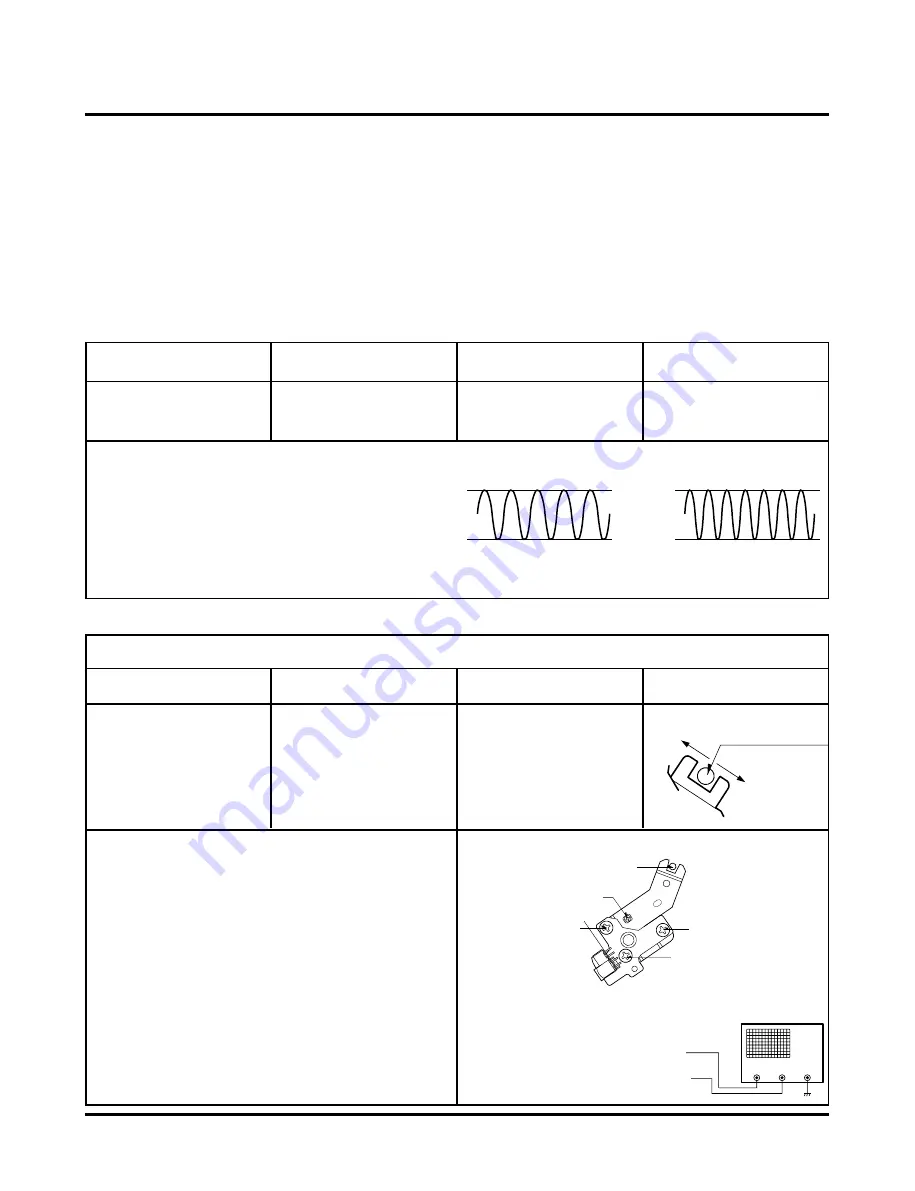
DECK MECHANISM ADJUSTMENT
4-17
Purpose: To obtain compatibility with other VCR (VCP) Models.
5-2. Confirm that the Tape passes smoothly
between the Take-up Guide and Pinch Roller
(using a Mirror or the naked eye).
1)
After completing Step 5-1. (Preliminary Adjustment),
check that the Tape passes around the Take-up Guide
and Pinch Roller without Folding or Curling at the Top or
Bottom.
(1) If Folding or Curling is observed at the Bottom of
the Take-up Guide then slowly turn the Tilt
Adjustment Screw (C) in the Clockwise direction.
(2) If Folding or Curling is observed at the Top of it then
slowly turn the Tilt Adjustment Screw (C) in the
Counterclockwise direction.
Check the RF Envelope after adjusting the A/C Head, if
the RF Waveform differs from Fig. C-5-4, performs
Precise Adjustment to flat the RF Waveform.
Test Equipment/ Fixture
• Oscilloscope
• Alignment Tape (SP)
• Screw Driver (+) Type 5mm
Connection Point
• Audio output jack
Test Conditions
(Mechanism Condition)
• Play an Alignment Tape
1KHz, 7KHz Sections
Adjustment Point
• Azimuth Adjustment Screw (A)
• Height Adjustment Screw (B)
1) Connect the Probe of the Oscilloscope to the Audio
Output Jack.
2) Alternately adjust the Azimuth Adjustment Screw (A)
and the Tilt Adjustment Screw (C) for Maximum Output
of the 1Khz and 7Khz segments, while maintaining the
flattest Envelope differential between the two
Frequencies.
Adjustment Procedure
5-3. Precise Adjustment (Azimuth adjustment)
6. X-Value Adjustment
Fig. C-5-4
1KHZ
• Oscilloscope
• Alignment tape (SP only)
• Screw Driver (+) Type 5mm
• CH-1: PB RF Envelope
• CH-2: NTSC: SW 30Hz
PAL: SW 25Hz
• Head Switching Output
Test Point
• RF Envelope Output Test
Point
Test Conditions
(Mechanism Condition)
• Play an Alignment Tape
Adjustment Point
Connection Point
Test Equipment/ Fixture
Adjustment Procedure
1) Release the Automatic Tracking to run long enough for
Tracking to complete it’s Cycle.
2) Loosen the Fixed Mounting Screw and move the A/C
Head Base Assembly in the direction as shown in the
Diagram to find the center of the peak that allows for the
maximum Waveform Envelope.
This method should allow the 31um Head to be centrally
located over the 58um Tape Track.
3) Tighten the A/C Head Base Assembly mounting Screw.
7KHZ
A:Maximum
B:Maximum
Left
Right
Groove at the
Base A/C
Height Adjustment Screw (B)
Tilt Adjustment Screw (C)
Azimuth Adjustment
Screw (A)
X-Value Adjustment Hole
Fixed Screw
RF ENVELOPE OUTPUT TEST POINT
OSCILLOSCOPE
HEAD SWITCHING OUTPUT TEST POINT
Connection Diagram
Adjustment Diagram
NOTE:
CH-1 CH-2
Summary of Contents for LGXBR342
Page 10: ...OVERALL WIRING DIAGRAM 3 2 ...
Page 36: ...3 36 3 37 EE MODE VIDEO TU MODE AUDIO 2 TU IF CIRCUIT DIAGRAM ...
Page 38: ...3 40 3 41 4 JACK CIRCUIT DIAGRAM ...
Page 44: ...3 52 3 53 PRINTED CIRCUIT DIAGRAMS 1 VCR P C BOARD ...
Page 45: ...3 54 3 55 3 TIMER P C BOARD 2 POWER P C BOARD ...
Page 46: ...3 56 3 57 4 KEY P C BOARD 5 JACK P C BOARD ...
Page 47: ......
Page 60: ...3 70 3 71 CIRCUIT DIAGRAMS 1 E5_BGA POWER UART2 CIRCUIT DIAGRAM ...
Page 61: ...3 72 3 73 2 DDR_SDRAM FLASH CIRCUIT DIAGRAM ...
Page 62: ...3 74 3 75 3 RST CONTROL STATUS_REG ATAPI HOST_CPLD LATCH CIRCUIT DIAGRAM ...
Page 63: ...3 76 3 77 4 1394 ETHERNET_CONNECTOR CIRCUIT DIAGRAM ...
Page 64: ...3 78 3 79 5 VIDEO_IN OUT CIRCUIT DIAGRAM ...
Page 65: ...3 80 3 81 6 AUDIO IN OUT NON STD_VIDEO CIRCUIT DIAGRAM ...
Page 66: ...3 82 3 83 7 AUDIO DAC VIDEO_Y MIXER CIRCUIT DIAGRAM ...
Page 67: ...8 FRONT A V 1934 JACK CIRCUIT DIAGRAM 3 84 3 85 ...
Page 72: ...3 94 3 95 PRINTED CIRCUIT DIAGRAMS 1 MAIN P C BOARD TOP VIEW ...
Page 73: ...3 96 3 97 2 MAIN P C BOARD BOTTOM VIEW ...
Page 103: ...3 127 4 IC302 uPD76f0047 MICOM Pin Assignment ...
Page 125: ......
Page 127: ...3 151 3 152 2 DSP CIRCUIT DIAGRAM No Power No operation DSP IC RESET IC SDRAM R259 0Ω ...
Page 129: ...3 155 3 156 PRINTED CIRCUIT DIAGRAMS 1 MAIN P C BOARD LOCATION GUIDE ...
Page 152: ...MAINTENANCE INSPECTION PROCEDURE 4 22 GEAR F R GEAR AY P2 P3 F R Lever Tension Base Boss CAM ...
Page 161: ...MEMO ...
Page 163: ......